扭轉疲勞壽命檢測:核心檢測項目解析
一、扭轉疲勞檢測的核心項目
-
- 目的:測定材料的極限承載能力及塑性變形臨界點。
- 方法:通過靜態扭轉試驗機施加遞增扭矩,記錄扭矩-轉角曲線,確定材料的扭轉強度(?maxTmax?)和屈服扭矩(??Ty?)。
- 標準參考:ASTM E143(金屬材料剪切模量測試)、ISO 1352(金屬線材扭轉試驗)。
-
- 目的:評估材料在不同循環應力幅值下的壽命特性。
- 方法:
- 設定恒定或變幅扭矩載荷(如正弦波、梯形波),持續加載直至試樣斷裂。
- 記錄循環次數(?N)與對應的應力幅值(??τa?),繪制S-N曲線(應力-壽命曲線)。
- 關鍵參數:疲勞極限(無限壽命應力閾值)、裂紋萌生周期。
- 應用場景:齒輪軸、傳動軸、風電聯軸器等承受交變扭轉負載的部件。
-
- 目的:研究裂紋從萌生到斷裂的動態過程,預測剩余壽命。
- 方法:
- 使用預制裂紋試樣,在循環扭矩下監測裂紋長度隨循環次數的變化。
- 結合斷裂力學模型(如Paris公式:??/??=?(Δ?)?da/dN=C(ΔK)m),計算裂紋擴展速率。
- 設備需求:高精度顯微鏡或聲發射傳感器實時監測裂紋。
-
- 目的:分析疲勞失效的微觀機理(如晶界滑移、孿晶形成)。
- 技術手段:
- 掃描電鏡(SEM):觀察斷口形貌(疲勞輝紋、韌窩等)。
- 電子背散射衍射(EBSD):分析晶粒取向與變形局部化。
- 典型發現:高頻次載荷下可能誘發馬氏體相變(如高強鋼)。
-
- 目的:評估加工工藝(如噴丸、熱處理)對疲勞性能的影響。
- 檢測項:
- X射線衍射法:量化表面殘余應力分布。
- 硬度梯度測試:分析應力集中區域(如螺紋根部)。
二、檢測流程與設備要求
-
- 標準試樣:圓柱形(直徑6-12mm)、漏斗形(應力集中設計)。
- 表面處理:拋光至Ra≤0.8μm,避免劃痕引入應力集中。
-
- 動態扭轉試驗機:需具備高頻加載能力(≥20Hz)、扭矩精度±1%。
- 環境模擬裝置:溫度(-70℃~300℃)、腐蝕介質(如鹽霧)。
-
- 實時記錄扭矩、轉角、溫度等參數。
- 使用軟件(如nCode DesignLife)進行疲勞損傷累積分析。
三、行業標準與規范
- 國際標準:
- ASTM F1820(骨科植入物扭轉疲勞測試)
- ISO 12107(金屬材料疲勞試驗統計方案)
- 行業特殊要求:
- 汽車:SAE J2380(驅動軸扭轉耐久性)
- 風電:IEC 61400-4(風機齒輪箱測試)
四、案例應用:汽車傳動軸扭轉疲勞優化
- 問題:某車型傳動軸在10^6次循環后出現斷裂。
- 檢測分析:
- S-N曲線顯示疲勞極限低于設計值15%。
- SEM斷口分析發現未回火馬氏體導致脆性斷裂。
- 改進措施:調整熱處理工藝(提高回火溫度),表面噴丸強化。
- 結果:疲勞壽命提升至1.5×10^6次,符合SAE標準。
五、未來發展趨勢
- 多軸疲勞耦合測試:復合載荷(扭轉+彎曲+軸向)模擬真實工況。
- 數字孿生技術:結合CAE仿真與實測數據,實現壽命預測智能化。
- 新材料評估:碳纖維復合材料、高熵合金的扭轉疲勞特性研究。

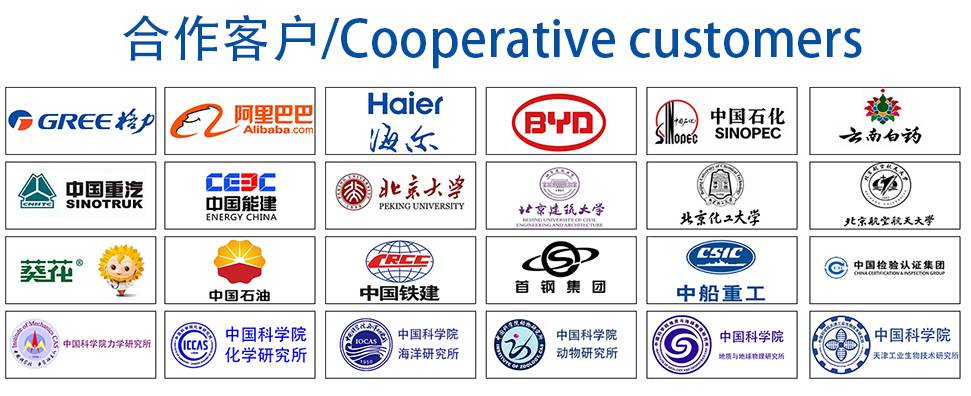
材料實驗室
熱門檢測
8
10
10
15
11
19
15
17
17
22
19
21
21
22
27
21
15
20
24
28
推薦檢測
聯系電話
400-635-0567