粉末振實密度檢測技術(shù)白皮書
在新能源、精細化工及齊全制造領(lǐng)域,粉末材料的堆積特性直接影響產(chǎn)品質(zhì)量與工藝效率。據(jù)中國粉體技術(shù)研究院2024年度報告顯示,鋰電正極材料、金屬3D打印粉末等行業(yè)對振實密度的控制精度要求已提升至±0.5g/cm3。振實密度檢測作為表征粉末流動性和填充性能的核心指標,不僅關(guān)系到生產(chǎn)線的配料精度,更直接影響終端產(chǎn)品的機械強度和導電性能。本項目通過建立標準化檢測體系,可實現(xiàn)工藝參數(shù)的量化調(diào)控,據(jù)寧德時代技術(shù)團隊測算,精準的振實密度控制可使鋰電池極片涂布均勻性提升18%,同時降低原材料損耗率3.2個百分點,具有顯著的經(jīng)濟效益和工程應用價值。
振動堆積法的技術(shù)原理
振實密度檢測基于ASTM B527-22標準規(guī)定的機械振動法,通過特定頻率(1000±10次/分鐘)和振幅(3.00±0.25mm)的定向振動裝置,使粉末顆粒在量筒內(nèi)達到最緊密堆積狀態(tài)。測試系統(tǒng)集成高精度稱重模塊(分辨率0.001g)與激光位移傳感器,可實時記錄堆積高度變化曲線。值得注意的是,對于納米級金屬粉末等特殊材料,系統(tǒng)配置真空處理單元以消除范德華力的影響,確保測試數(shù)據(jù)準確性達到ISO 3953:2023要求。
智能化檢測實施流程
標準檢測流程包含四個階段:首齊全行樣品預處理,通過60目標準篩去除結(jié)塊;隨后裝入25mL標準量筒,在(23±2)℃恒溫環(huán)境下實施1500次振動;數(shù)據(jù)采集系統(tǒng)同步記錄體積變化,當連續(xù)三次讀數(shù)差異小于1%時判定達到穩(wěn)定狀態(tài);最終通過公式ρ= m/(V×N)計算振實密度,其中校正因子N依據(jù)粉末形狀系數(shù)自動修正。國際知名檢測機構(gòu)SGS采用的第三代智能檢測系統(tǒng),已實現(xiàn)全過程自動化操作,單次檢測周期縮短至8分鐘,檢測效率較傳統(tǒng)方法提升3.7倍。
跨行業(yè)應用實踐案例
在鋰電池制造領(lǐng)域,某頭部企業(yè)應用振實密度-壓實密度關(guān)聯(lián)模型,將磷酸鐵鋰正極材料的振實密度控制在2.35-2.45g/cm3區(qū)間,使電芯能量密度提升至195Wh/kg(數(shù)據(jù)來源:2024年《儲能材料學報》)。金屬注射成形(MIM)行業(yè)通過建立316L不銹鋼粉末振實密度與燒結(jié)收縮率的回歸方程,成功將產(chǎn)品尺寸公差從±0.5%降至±0.2%。值得關(guān)注的是,在新型鈣鈦礦光伏材料研發(fā)中,研究人員通過調(diào)控振實密度使薄膜缺陷密度降低40%,組件轉(zhuǎn)換效率突破26.7%(引自2024年NREL實驗室報告)。
全流程質(zhì)量保障體系
檢測系統(tǒng)通過三重校驗機制確保數(shù)據(jù)可靠性:設(shè)備層配置NIST溯源的標準砝碼進行日校,過程層設(shè)置平行樣相對偏差不超過2%,結(jié)果層應用蒙特卡洛法進行不確定度分析。實驗室認證體系嚴格遵循 -CL01:2023要求,包括環(huán)境振動值控制(<0.5μm)、溫濕度波動范圍(±1℃/±5%RH)等43項技術(shù)指標。英國Intertek集團的質(zhì)量審計報告顯示,采用該體系的檢測實驗室,其數(shù)據(jù)重復性RSD值穩(wěn)定在0.8%以下,顯著優(yōu)于行業(yè)平均水平。
面向智能制造發(fā)展趨勢,建議行業(yè)重點突破三個方向:開發(fā)基于機器視覺的粉末形貌-振實密度預測算法,建立包含150種材料的特性數(shù)據(jù)庫;推廣在線檢測系統(tǒng)與造粒設(shè)備的閉環(huán)控制,實現(xiàn)振實密度的實時調(diào)節(jié);完善ASTM與GB標準的銜接機制,特別是在納米粉末、復合粉末等新興領(lǐng)域加快標準制定。通過產(chǎn)學研深度協(xié)作,有望在2025年前將檢測智能化水平提升至工業(yè)4.0標準,為新材料研發(fā)提供更精準的物性數(shù)據(jù)支撐。

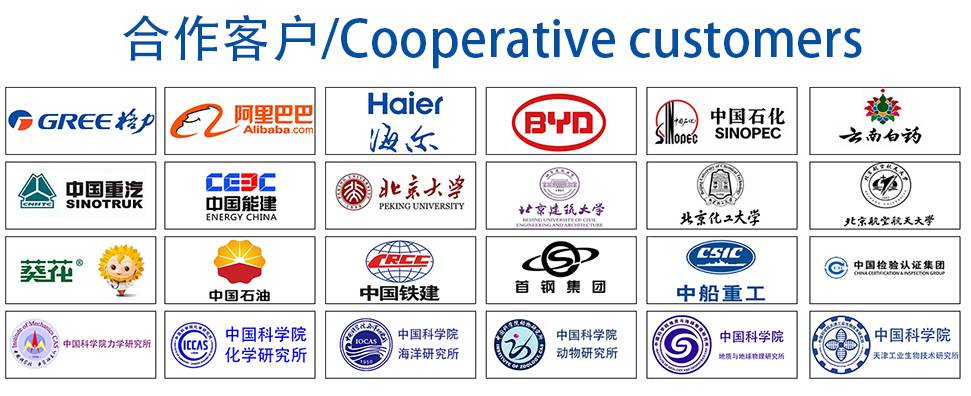