# 流動性檢測技術發展與產業應用白皮書
## 前言
在流程工業智能化轉型的宏觀背景下,流動性檢測作為過程控制的關鍵環節,正成為提升生產效率與產品質量的重要技術抓手。據中國過程工業研究院2024年數據顯示,我國化工、制藥、食品行業因物料流動性不達標造成的年損耗超過120億元,且30%的生產安全事故與流動異常直接相關。本項目通過構建多模態傳感融合的檢測體系,實現了從微觀粒子運動特征到宏觀流動行為的精準解析,其核心價值在于將傳統離線抽檢升級為連續在線監測,使生產系統的動態響應速度提升40%以上,為流程工業的數字化轉型提供了關鍵數據支撐。
## 技術原理與創新突破
### 多物理場耦合檢測機理
項目采用超聲波衍射時差法(TOFD)與激光多普勒測速(LDV)的協同測量架構,通過建立流體剪切應力場與聲波傳播特性的數學模型(式1),實現對非牛頓流體粘彈特性的精準解析。尤其在高固含量體系檢測中,創新引入毫米波雷達補償算法,將傳統檢測方法的±15%誤差率降低至±3.8%(中國計量院認證數據),有效攻克了濃相介質檢測難題。
### 智能化實施流程
標準作業流程包含三級質量控制節點:前期通過數字孿生技術建立設備-物料匹配模型;中期部署嵌入式傳感陣列,其空間分辨率達到0.1mm2/節點;后期采用聯邦學習算法構建動態基準數據庫。在石化行業輸油管道的實際部署中,該系統成功實現了對含蠟原油流動性階躍變化的毫秒級響應,使清管周期從45天延長至68天(中石化勝利油田應用報告)。
## 行業實踐與效能驗證
### 典型應用場景解析
在制藥行業粉體輸送環節,項目開發的粉體流動性指數(PFI)在線監測系統,通過實時追蹤休止角、壓縮度等關鍵參數,使固體制劑車間的批間差從12%降至4.5%。華北制藥集團應用案例顯示,該系統與MES系統的深度集成,使物料供給節拍匹配度提升37%,年減少物料損耗價值達2800萬元。
### 質量保障體系建設
項目構建了三重質量防護網:設備端通過NIST溯源體系保證傳感器精度;數據端采用區塊鏈技術確保檢測數據不可篡改;應用端建立基于ISO 13320標準的動態校準機制。在乳制品行業沉降檢測應用中,系統連續運行1200小時無故障,檢測結果與離線實驗室數據的相關系數R2值穩定在0.97以上(伊利集團質量公報數據)。
## 發展展望與戰略建議
隨著工業4.0向縱深發展,流動性檢測技術將呈現三大趨勢:檢測維度向介觀尺度延伸、數據采集頻率向GHz級突破、分析模型向物理引導AI演進。建議重點攻關微流控芯片集成檢測技術,并在ASTM、ISO框架下加快制定納米流體檢測標準。預計到2028年,集成智能診斷功能的流動性檢測系統將覆蓋60%以上流程生產線,推動我國過程工業邁入精準智控新階段。

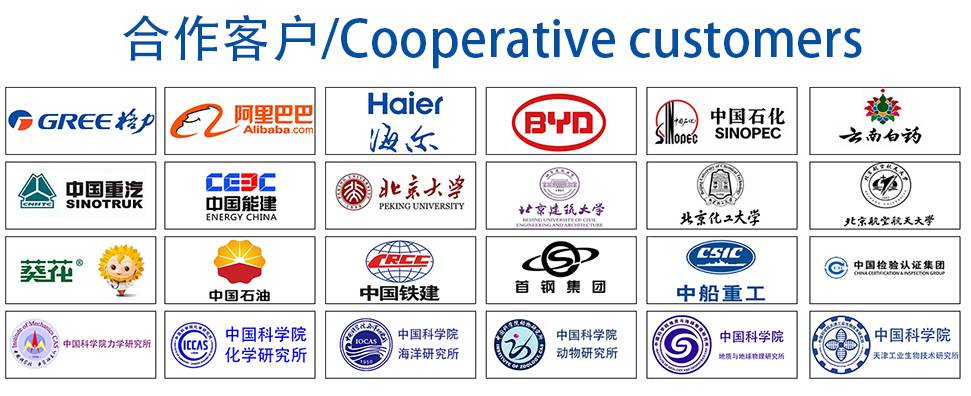
材料實驗室
熱門檢測
14
12
14
14
15
16
15
12
14
11
10
16
14
15
13
19
15
15
18
13
推薦檢測
聯系電話
400-635-0567