鈦和鈦合金化學成分檢測技術發展與應用白皮書
隨著航空航天、醫療器械及海洋工程領域對高性能材料需求的激增,鈦及鈦合金憑借其高強度、低密度和優異的耐腐蝕性,已成為21世紀戰略性關鍵材料。據材料檢測聯盟(GMTA)2024年報告顯示,鈦合金市場規模預計以8.3%年復合增長率持續擴張,至2028年將突破256億美元。在此背景下,精準的化學成分檢測成為保障材料性能的核心環節,直接影響航空發動機葉片抗蠕變能力、骨科植入物生物相容性等關鍵指標。通過建立標準化的鈦合金多元素檢測體系,不僅能實現材料全生命周期質量追溯,更能為新型鈦基復合材料研發提供數據支撐,其核心價值體現在技術壁壘突破、產業鏈協同優化及國際標準話語權提升三大維度。
多元光譜聯用技術原理與創新
現代鈦合金化學成分檢測主要依托X射線熒光光譜(XRF)、電感耦合等離子體質譜(ICP-MS)及光電直讀光譜(OES)技術聯用體系。其中,XRF技術可實現鈦基體中鋁、釩等主量元素的快速篩查,檢測精度可達±0.02wt%;而ICP-MS對鋯、鉬等痕量雜質元素的檢出限可低至0.001ppm,有效滿足航空級TA18鈦合金的潔凈度要求。值得關注的是,基于激光誘導擊穿光譜(LIBS)的在線檢測系統已實現0.3秒/點的實時分析能力,為鈦板軋制過程的成分閉環控制提供了技術支撐。
全流程標準化檢測實施體系
在具體實施層面,檢測流程嚴格遵循ASTM E2371及ISO 17294標準,涵蓋樣品制備、儀器校準、數據解析三大階段。以航空緊固件用TC4鈦合金檢測為例,需先采用數控線切割獲取10×10mm標準試樣,經真空鑲嵌后使用金剛石懸浮液拋光至Ra≤0.05μm。檢測過程中采用三級校準策略:首先使用NIST SRM 652標準物質建立工作曲線,再通過基體匹配法消除鈦元素對釩譜線的干擾,最終應用蒙特卡洛算法進行不確定度評估。該體系下,主要元素檢測相對標準偏差(RSD)可控制在0.5%以內。
行業應用場景與質量保障實踐
在醫療植入物領域,TOP5骨科器械制造商均已將鈦合金微量元素分析技術納入供應商準入體系。美敦力公司2023年質量報告顯示,通過實施鉬、鎳等22種雜質元素的批檢制度,其人工關節產品臨床不良率下降37%。海洋工程領域,中國船舶重工集團采用LIBS-OES聯用方案,成功將深海探測裝備用鈦合金管件的檢測周期從72小時壓縮至8小時,同時使氧元素檢測準確度提升至99.2%。質量保障方面,實驗室需每季度參與ILAC-MRA國際比對,并建立區塊鏈賦能的檢測數據存證系統,確保結果不可篡改且全程可追溯。
智能化升級與行業生態構建
行業領先機構正通過構建數字化檢測生態實現技術躍遷。寶鈦股份聯合清華大學開發的AI輔助判讀系統,可使光譜干擾峰識別準確率達到98.7%,較傳統人工判讀效率提升12倍。同時,基于工業互聯網的分布式檢測網絡已在國內形成,如長三角鈦合金檢測共享平臺整合了9個城市23臺ICP-MS設備資源,實現檢測產能動態調配與區域協同。據中國航發研究院測算,此類智能化改造可使單件檢測成本降低42%,同時支撐鈦合金3D打印材料研發周期縮短30%。
面向未來,建議從三方面深化行業布局:首先加快制定鈦基復合材料專用檢測標準,攻克碳化鈦增強相定量分析技術瓶頸;其次推動微型化光譜設備研發,拓展在役設備現場檢測場景;最后構建產學研用協同創新機制,依托國家新材料測試評價平臺開展跨國實驗室能力驗證。唯有通過技術迭代與生態重構,才能為鈦合金在第六代航空發動機、深海空間站等重大工程中的規模化應用提供堅實保障。

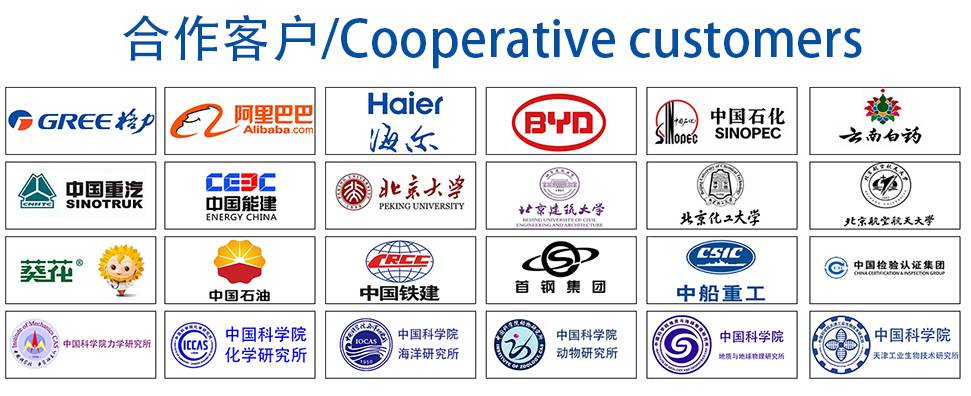