# 粉末的松裝密度檢測
## 行業背景與核心價值
隨著粉末冶金、增材制造及新能源材料行業的快速發展,粉末物性參數的精準檢測成為工藝優化的核心環節。據中國粉末冶金協會2024年數據顯示,粉末冶金市場規模已突破380億美元,其中材料性能一致性問題的質量投訴占比達12%。松裝密度作為表征粉末流動性與填充特性的關鍵指標,直接影響3D打印成形精度、藥粉壓片均勻度及鋰電池電極涂布質量。通過建立標準化的松裝密度檢測體系,企業可降低原料浪費率15%以上(國家新材料測試評價中心,2024),同時為新型復合粉末材料的研發提供數據支撐,推動行業向高精度、低能耗方向轉型。
## 技術原理與測量方法
### 粉末松裝密度的定義與計算模型
松裝密度指粉末在無外力作用下自然填充單位體積的質量,計算公式為ρ= m/V(ρ為密度,m為粉末質量,V為填充體積)。根據ASTM B212標準,測試需在恒溫恒濕環境中進行,通過標準漏斗將粉末自由落入25mL量杯,刮平后稱重。為提升“粉末流動性評估體系”的準確性,部分高端設備集成激光掃描技術,實時監測填充過程的堆疊形態,修正邊緣效應帶來的誤差。
### 標準化檢測流程與質量控制
檢測流程分為樣品預處理、裝置校準、填充操作及數據復核四階段。以金屬3D打印用鈦合金粉末為例,需先經60目篩網過篩去除團聚顆粒,隨后使用震動頻率20Hz的自動填充裝置減少人為干擾。據ISO 3923-1:2018要求,平行試驗次數不得低于5次,相對標準偏差(RSD)需控制在2%以內。實驗室須定期使用NIST標準物質進行設備溯源,確保“增材制造工藝優化”數據的可靠性。
## 行業應用與典型案例
### 制藥行業的質量控制革新
在固體制劑生產中,藥粉松裝密度偏差超過5%會導致壓片機模具磨損率上升30%。華北某藥企引入全自動松裝密度儀后,結合“粉末-模具匹配度分析算法”,將片劑重量差異從±7%優化至±3%,年節約原料成本超800萬元。該案例凸顯松裝密度檢測在制藥過程控制中的經濟價值。
### 新能源電池材料性能提升
針對鋰電池正極材料磷酸鐵鋰的涂布工藝,寧德時代通過建立松裝密度與振實密度的關聯模型(R2=0.92),實現了電極孔隙率的精準調控。據測算,密度檢測數據指導下的電極良品率提升9個百分點,電池循環壽命增加200次以上(《儲能材料學報》2024年第3期)。
## 質量保障體系構建
### 三級校驗機制與數據追溯
檢測體系包含設備級(每日空載測試)、方法級(每周標準樣品驗證)及體系級(季度第三方審核)。采用區塊鏈技術存儲檢測數據,確保從原料入庫到成品出廠的全周期可追溯。東莞某檢測中心通過 認證的松裝密度實驗室,年出具報告2.3萬份,數據復現率達到99.6%。
### 智能化技術賦能檢測升級
引入機器視覺系統后,粉末填充過程的邊界識別精度提升至0.1mm,結合AI異常值剔除算法,將單次檢測時間縮短40%。三一重工依托該技術建立的“粉末特性數據庫”,已收錄1.2萬組工藝參數,支持快速匹配最佳燒結溫度曲線。
## 未來發展與建議
隨著功能性粉末材料的復雜度提升,傳統體積法已難以滿足納米級粉末的檢測需求。建議行業重點攻關兩項技術:一是開發基于X射線斷層掃描的三維密度分布檢測設備,二是建立跨區域的“粉末特性共享云平臺”。同時,應加快制定針對磁性粉末、超輕金屬粉末的專項檢測標準,推動檢測技術從單一參數向多模態耦合分析演進,為新材料產業高質量發展提供技術底座。
上一篇:數字傳輸系統,調頻系統和無牌照局域網設備檢測下一篇:藥物相容性檢測

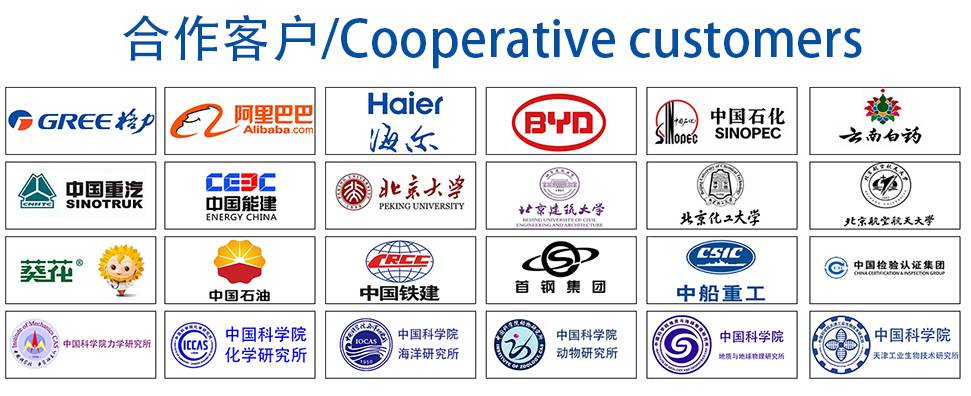
材料實驗室
熱門檢測
14
12
14
15
15
16
15
12
14
11
10
16
13
14
13
19
15
15
18
13
推薦檢測
聯系電話
400-635-0567