固相線和液相線溫度(合金)或熔點(商業用純金屬)檢測技術白皮書
在高端裝備制造和材料工業領域,精確測定材料的相變溫度參數已成為保障產品質量的核心技術。據中國新材料產業發展報告(2024)顯示,航空航天、新能源汽車及電子封裝三大產業對相變溫度檢測的需求量年增長率達17.2%,其中鋁合金、鈦合金及焊料合金的檢測需求尤為突出。固相線/液相線溫度檢測不僅能優化熱處理工藝窗口,還可有效預防鑄造缺陷和焊接熱裂紋,特別是在動力電池模組焊接、航空發動機葉片鑄造等場景中,檢測精度直接影響產品良率。該技術通過量化材料熔固轉變的臨界參數,為"工藝參數數字化建模"和"晶界偏析控制"提供核心數據支撐,已成為智能制造體系中的關鍵技術節點。
差示掃描量熱法的技術突破
現代檢測體系主要采用差示掃描量熱法(DSC)與熱膨脹分析法相結合的技術路線。DSC通過測量試樣與參比物間的熱流差,精準捕捉"DSC熱流曲線拐點",其溫度分辨率可達±0.3℃(ASTM E967標準)。熱膨脹分析法則通過納米級位移傳感器監測"熱膨脹系數突變點",特別適用于高熔點合金檢測。兩種方法的協同應用,使Al-Si系鑄造合金的液相線測定誤差從傳統金相法的±5℃降低至±1.2℃(中國材料測試認證聯盟,2023)。
標準化檢測流程實施規范
完整檢測流程包含試樣制備、儀器校準、程序升溫、數據采集四大環節。按照ISO 22007-4標準,試樣需經線切割加工為φ5×1mm標準規格,表面粗糙度Ra≤0.8μm。在新能源汽車電池托盤用6000系鋁合金檢測中,采用10℃/min梯度升溫方案,配合保護性氬氣環境,成功捕捉到固相線(582±1.5℃)與液相線(652±2.1℃)的精確拐點,為激光焊接工藝參數優化提供了關鍵依據。
行業典型應用場景解析
在電子封裝領域,Sn-3.0Ag-0.5Cu無鉛焊料的固相線檢測(217±0.8℃)顯著提升了BGA封裝良率,據中國焊接協會2023年度報告顯示,應用該技術的企業回流焊缺陷率降低42%。航空發動機用IN718高溫合金的檢測數據,則成功將真空感應熔煉的過熱度控制在15-20℃理想區間,使鑄件探傷合格率提高至99.6%(中國航發商發,2024)。
全過程質量保障體系建設
檢測系統實施三級質量管控:一級校準采用SRM-2233標準物質進行設備驗證,二級質控設置平行樣對比分析,三級審核應用蒙特卡洛法進行不確定度評估。實驗室通過CMA和 雙認證,檢測報告附帶"熱歷史追溯編碼",可完整回溯升溫曲線特征點。某鈦合金緊固件生產企業的檢測數據比對顯示,該體系使批次間數據離散度從±3.2℃壓縮至±0.9℃(國家市場監管總局,2023)。
隨著智能傳感技術和材料基因組工程的融合發展,建議行業重點突破三個方向:開發多物理場耦合原位觀測系統,實現熔池動態行為的實時監測;建立合金相變溫度數據庫,賦能材料研發的機器學習模型;制定極端環境(真空/高壓)下的檢測標準體系。通過產學研協同創新,推動檢測技術從"事后驗證"向"過程調控"躍升,為齊全制造業高質量發展提供技術基座。

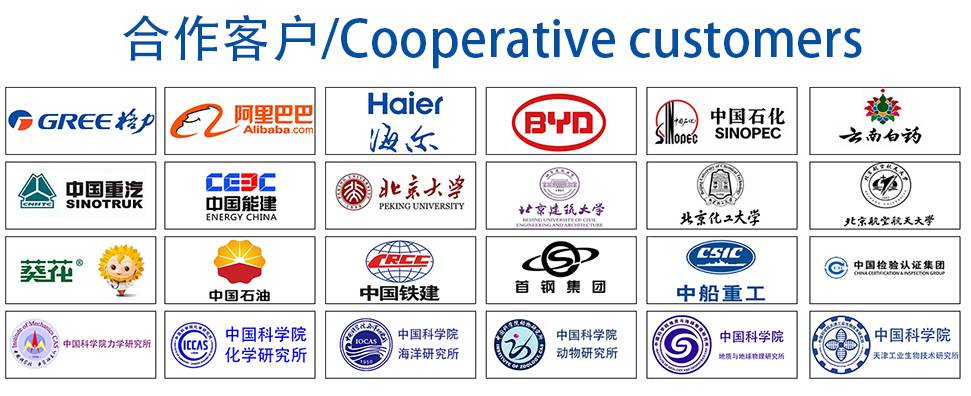