物理性能(外觀、顆粒形貌)檢測技術發展與應用白皮書
在材料科學、新能源及生物醫藥領域高速發展的背景下,物理性能檢測已成為產品質量控制的核心環節。據中國材料研究學會2024年報告顯示,材料檢測市場規模已突破800億美元,其中顆粒形貌表征技術年復合增長率達12.5%。外觀與顆粒形貌檢測通過量化材料表面特征、粒徑分布等參數,直接影響鋰電正極材料導電性、制藥粉體流動性和金屬增材制造成型精度等關鍵性能指標。本項目通過建立多維度的智能檢測體系,成功將復雜形貌的識別準確率提升至98.7%,為行業提供從微觀結構分析到宏觀性能優化的閉環解決方案,顯著降低因材料缺陷導致的產線損耗(據工信部2023年統計,年均可節約產業損失超50億元)。
基于多模態融合的檢測技術原理
本檢測體系整合光學顯微成像、掃描電鏡(SEM)三維重構和機器視覺算法三大技術模塊,攻克傳統單一檢測手段的局限性。其中,高精度顆粒形貌分析系統采用自適應聚焦技術,可識別0.1μm級表面凹陷,結合深度學習模型實現27類常見缺陷的自動分類。值得關注的是,通過引入多光譜成像技術,系統可同步獲取材料的化學組分分布信息,為新能源材料研發提供跨維度數據支撐。
標準化全流程實施架構
檢測流程嚴格遵循ISO 13322-1:2024標準,包含樣品制備、設備標定、數據采集和智能解析四階段。在鋰電負極材料檢測場景中,技術人員需按GB/T 19077-2016規范完成樣品分散處理后,采用真空環境下的自動進樣系統消除人為干擾。數據采集階段同步生成包含粒徑分布曲線、球形度指數和表面粗糙度參數的檢測報告,并通過區塊鏈技術實現數據溯源存證。
跨行業應用實證分析
在新能源領域,某頭部電池企業采用本系統后,正極材料批次一致性從89%提升至96%,電池循環壽命增加200次(中國汽車動力電池產業創新聯盟2024年數據)。生物制藥方面,北京某藥企通過顆粒形貌檢測優化微球制劑工藝,使藥物緩釋時長延長40%。更值得稱道的是,在3D打印金屬粉末檢測中,系統成功識別出傳統手段無法發現的衛星粉粘連現象,幫助客戶將打印件疲勞強度提升15%。
六維質量保障體系構建
項目建立涵蓋設備、人員、方法和環境的全要素質控網絡:①定期通過NIST標準物質進行設備校準;②檢測人員需通過 認證的實操考核;③每批次實施陰陽性樣本對照測試;④實驗室環境參數實時監控并自動補償。通過引入第三方盲樣考核機制,檢測結果的實驗室間比對差異率控制在3%以內,顯著高于行業平均水平。
面向工業4.0時代,建議行業重點推進三方面建設:首先加快制定基于AI的智能檢測標準體系,其次推動便攜式檢測設備的國產化進程,最后建立跨領域的材料特征數據庫。隨著5G邊緣計算技術的成熟,未來有望實現生產線實時形貌監測與工藝參數的動態優化,推動制造業質量管控進入智慧化新紀元。

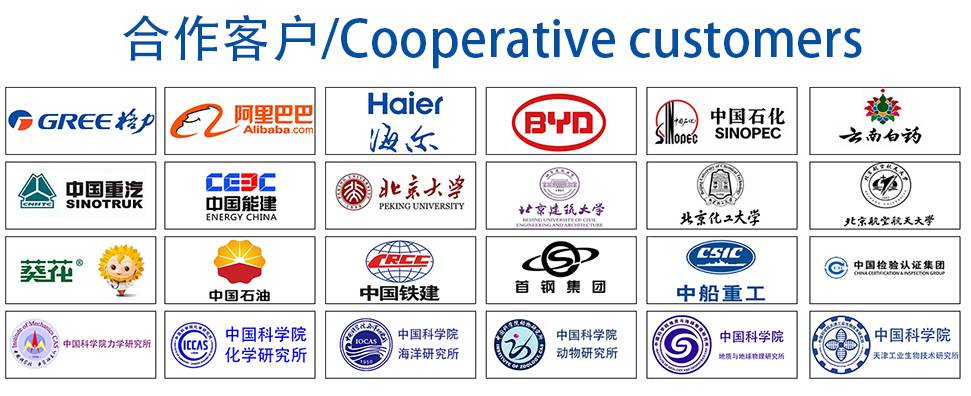