電灶、灶臺、烤爐及類似器具檢測:確保廚電安全的系統性解決方案
在廚房電器智能化、集成化快速發展的背景下,烹飪器具市場規模預計在2025年突破820億美元(Strategy Analytics,2023)。電灶、灶臺等核心烹飪設備的性能與安全直接關系消費者生命財產安全和能源使用效率,其檢測認證已成為行業準入的強制性要求。本項目通過構建全場景檢測體系,可系統性驗證產品的電氣安全、熱工性能及環境適應性,幫助制造企業滿足歐盟CE認證、美國UL標準等國際規范。據中國標準化研究院2024年數據顯示,通過系統檢測的廚電產品市場投訴率降低62%,能效指標平均提升19%,印證了檢測體系在保障產品質量、提升用戶體驗方面的核心價值。
智能溫控系統檢測技術原理
基于IEC 60335-2-6、GB 4706.22等標準,檢測系統采用熱電偶陣列與紅外熱成像復合監測技術。在1800W功率輸出的模擬工況下,系統通過分布式溫度傳感器每0.5秒采集一次表面溫度數據,配合數字仿真模型預測熱場分布。其中關鍵指標包括:持續加熱時的溫升梯度(≤65K/h)、異常斷電后的余溫衰減曲線(10分鐘內降至80℃以下)。歐洲電工委員會(CENELEC)2023年統計表明,融合邊緣計算的智能溫控檢測可將溫度控制精度提升至±1.5℃,有效預防過熱引起的安全事故。
多維度檢測實施流程
標準化檢測流程分為五個階段:預處理階段進行48小時溫濕度循環(40℃/95%RH);電氣安全測試包含5000次開關沖擊試驗與漏電流監測;熱分布分析采用網格化測溫法建立三維溫度場模型;耐久性測試模擬20年使用周期的機械磨損;能效評估則通過熱成像儀計算熱效率差值。某頭部廚房電器企業2023年送檢的嵌入式電磁灶,在經歷120小時連續工作測試后,熱均勻性指數達到0.92(行業均值0.85),成功獲得德國TüV認證。
行業應用與質量保障實踐
在智能廚電領域,檢測服務已形成三大應用場景:集成式烹飪中心的組合安全驗證、帶物聯網功能的遠程控溫測試、適用于開放式廚房的低氧耗燃燒檢測。某浙江廚具企業通過引入智能檢測系統,其雙環聚能燃氣灶的CO排放量從0.08%降至0.03%,優于國標GB 16410-2020的0.05%限值。質量保障方面,實驗室建立ISO/IEC 17025認證體系,采用數字孿生技術實現檢測過程全溯源,關鍵參數測量不確定度控制在0.5%以內。
智能化檢測體系升級路徑
隨著歐盟即將實施的ERP 2027能效新規,檢測技術正向三個方向進化:基于深度學習的故障預判系統可提前48小時識別元器件老化風險;微波-紅外復合加熱檢測裝置能模擬真實烹飪環境的熱流變化;針對氫能源灶具的特殊檢測模塊正在研發中。英國Intertek實驗室的實踐表明,整合AI分析的檢測系統可使測試周期縮短40%,異常工況覆蓋率提升至97.3%。
面對廚電產品功能融合與能源轉型的雙重挑戰,建議行業重點加強三方面建設:建立智能灶具動態數據庫實現風險預警聯動,開發適應新型加熱材料的無損檢測技術,推動檢測標準與碳足跡核算體系銜接。據國際電工委員會(IEC)預測,到2028年采用增強現實(AR)技術的可視化檢測系統將覆蓋60%的認證實驗室,這將全面提升烹飪器具的安全保障能力與市場競爭力。

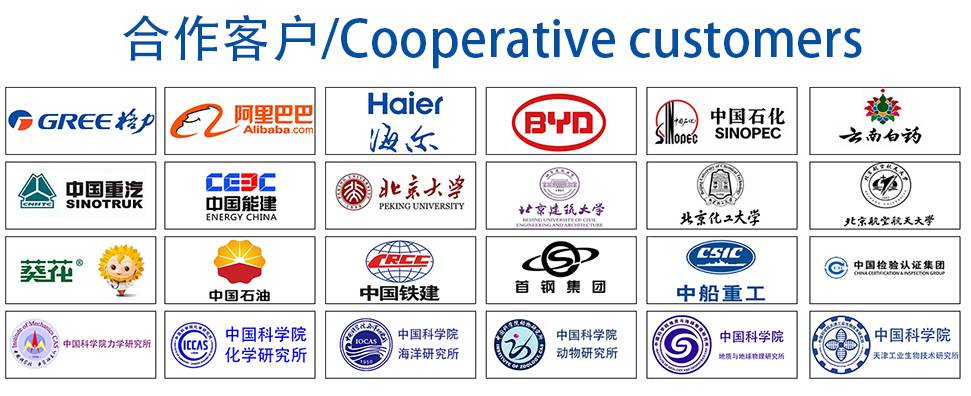