電子產品制造與應用系統檢測的重要性
在智能化與數字化的時代背景下,電子產品制造與應用系統的質量控制成為產業鏈的核心環節。檢測項目貫穿產品全生命周期,涵蓋原材料驗證、生產過程監控、成品性能評估及實際應用場景測試。通過科學化的檢測體系,不僅能保障產品可靠性、安全性和合規性,還能顯著降低售后風險,提升品牌市場競爭力。尤其在5G通信、物聯網設備、工業自動化等高精尖領域,系統化的檢測方案已成為企業通過國際認證(如CE、FCC、RoHS)和應對行業標準的必備技術手段。
核心檢測項目分類
電子產品檢測體系可分為四大模塊:
1. 來料檢測(IQC)
對電子元器件、PCB基板、連接器等原材料進行全尺寸測量、材料成分分析及電氣參數驗證。采用X射線熒光光譜儀檢測重金屬含量,通過高低溫循環測試評估材料熱穩定性,確保符合RoHS和REACH環保標準。
2. 生產過程檢測(IPQC)
在SMT貼裝、焊接、組裝等環節設置20+關鍵檢測節點:包括3D SPI焊膏印刷檢測、AOI光學自動檢測、ICT在線測試等。通過實時采集生產數據,建立SPC統計過程控制模型,將缺陷率控制在0.1%以下。
3. 成品綜合測試(OQC)
執行包括:
- 環境可靠性測試(85℃/85%RH雙85試驗、鹽霧測試)
- 電磁兼容性測試(輻射發射、靜電放電抗擾度)
- 功能壓力測試(72小時持續滿載運行)
- 安全規范測試(耐壓、絕緣電阻、接地連續性)
確保產品在極端條件下的穩定表現。
4. 應用系統檢測
針對智能家居、車載電子等具體場景,開展:
- 多設備組網兼容性測試
- OTA無線性能測試
- 人機交互壓力測試
- 系統級EMC驗證
通過搭建真實應用環境,模擬用戶使用習慣,檢測系統級故障率和響應延遲等關鍵指標。
檢測技術創新趨勢
隨著AIoT技術發展,檢測系統正向智能化方向演進:
- 基于機器視覺的缺陷自動分類系統
- 應用數字孿生技術的虛擬檢測平臺
- 搭載5G的遠程實時質量監控網絡
- 大數據驅動的預測性質量分析模型
這些創新使檢測效率提升40%以上,同時實現質量問題的根源追溯和工藝優化閉環。

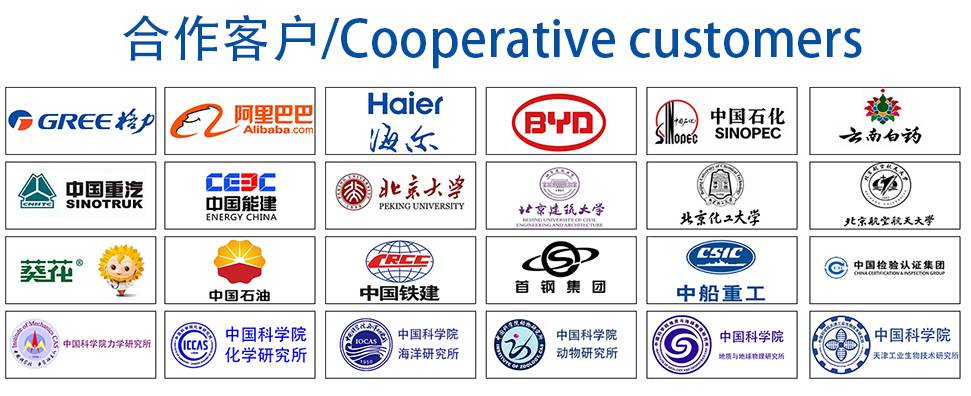