石化設備內壁用耐酸性防腐蝕涂料檢測的重要性
在石油化工行業中,設備內壁長期暴露于酸性介質、高溫、高壓及腐蝕性氣體的復雜環境中,極易發生腐蝕失效。一旦涂層性能不達標,可能導致設備泄漏、安全隱患和生產中斷,甚至引發重大事故。因此,針對石化設備內壁使用的耐酸性防腐蝕涂料進行系統性檢測,是保障設備安全運行、延長使用壽命的核心環節。檢測過程需涵蓋涂料的物理性能、化學穩定性、耐腐蝕能力及施工適應性等多個維度,以確保其滿足嚴苛工況下的技術要求。
關鍵檢測項目及方法
1. 耐酸性測試
通過模擬實際工況,將涂層樣品浸泡在不同濃度(如10%-50%的硫酸、鹽酸等)的酸性溶液中,觀察其在設定溫度(常溫至150℃)和時間周期(7-90天)下的變化。檢測指標包括涂層起泡、脫落、變色程度,并測定質量損失率。部分標準要求進行循環腐蝕試驗,交替暴露于酸液和干燥環境以驗證涂層抗滲透能力。
2. 附著力強度檢測
采用劃格法(ASTM D3359)或拉開法(ISO 4624)測定涂層與基材的結合力。對于曲面設備內壁,需使用專用夾具確保測試載荷垂直作用于涂層表面,數值應達到≥5MPa(環氧類涂料)或更高標準。同時需評估涂層的柔韌性(ASTM D522),避免因設備變形導致開裂。
3. 耐溫交變性能測試
通過高低溫循環試驗(如-30℃至200℃快速切換),驗證涂層在熱膨脹應力下的穩定性。重點檢測涂層是否出現龜裂、剝落或與基材分離現象,并利用掃描電鏡(SEM)分析微觀結構變化。
4. 涂層厚度與均勻性檢測
使用磁性測厚儀(ISO 2808)或渦流儀測量干膜厚度,確保達到設計值(通常150-500μm)。需在設備內壁不同位置(直管段、焊縫區、彎頭處)進行多點測量,厚度偏差需控制在±15%以內。針對多層涂裝體系,還需驗證層間結合力。
5. 環境適應性驗證
包括耐化學介質(原油、硫化物、有機溶劑等)浸泡試驗、耐鹽霧試驗(ASTM B117)、耐濕熱老化試驗等。對于海上平臺或臨海石化裝置,還需增加耐鹽霧-紫外線復合循環試驗,模擬海水飛濺與光照的協同腐蝕效應。
檢測標準與質量控制
檢測需嚴格遵循NACE TM0174、ISO 12944、GB/T 1771等國內外標準,同時結合設備設計參數(如介質PH值、流速、操作溫度)定制測試方案。建議采用第三方機構認證與廠內自檢結合的模式,并在施工后通過電化學阻抗譜(EIS)等無損檢測技術進行現場復驗,確保涂層系統的長效防護性能。
結論
耐酸性防腐蝕涂料的檢測是石化設備全生命周期管理的重要環節。通過科學的檢測體系,可有效篩選出滿足極端工況的涂層材料,降低設備維護成本并提升生產安全性。行業需持續推動檢測技術創新,例如引入人工智能輔助涂層缺陷識別、開發在線監測傳感器等,以應對更高標準的防腐需求。

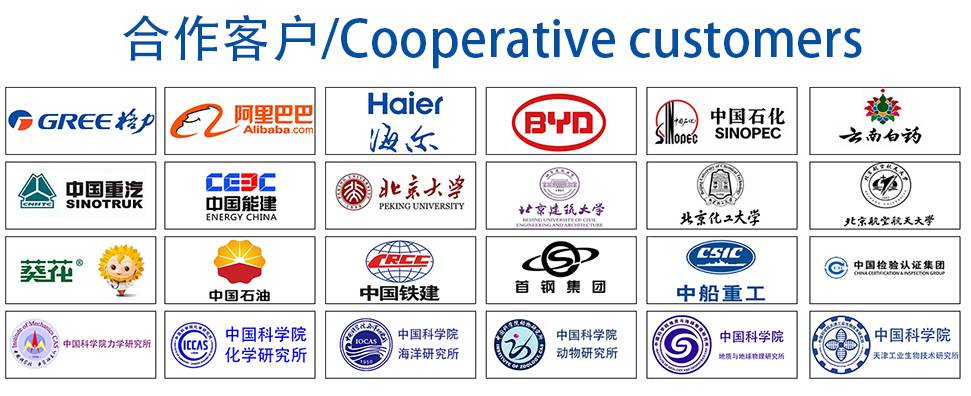