海上石油平臺用防腐涂料檢測的關鍵要點
海上石油平臺長期暴露于高鹽霧、高濕度、強紫外線及復雜化學介質的海洋環境中,其金屬結構的腐蝕問題尤為突出。據統計,每年因海洋腐蝕造成的經濟損失高達數千億美元。防腐涂料作為保護平臺設備與鋼結構的第一道防線,其性能直接影響平臺的安全性和使用壽命。因此,針對海上石油平臺用防腐涂料的檢測項目必須覆蓋物理性能、化學穩定性、環境適應性及耐久性等核心指標。嚴格的檢測不僅能確保涂料的防護效果,更能避免因涂層失效導致的設備損壞、生產中斷甚至安全事故。
1. 物理性能檢測
物理性能是衡量涂料與基材結合能力的基礎指標,主要包括附著力測試和涂層厚度檢測。通過劃格法(ASTM D3359)或拉開法(ISO 4624)評估涂層與基材的粘結強度,確保其能承受海洋環境中的機械沖擊。涂層厚度需使用磁性測厚儀或超聲波測厚儀進行多點測量,要求符合ISO 19840標準,避免因過薄導致防護不足或過厚引發開裂。
2. 耐環境腐蝕測試
鹽霧試驗(ASTM B117)模擬海洋高鹽霧環境,驗證涂料在長時間鹽霧侵蝕下的耐腐蝕性;耐水性測試(GB/T 1733)則通過浸水或冷凝水循環實驗,評估涂層的抗滲水能力。此外,耐化學介質測試(如耐酸、耐堿、耐油)需根據平臺作業環境選擇特定試劑進行浸泡或噴灑,確保涂層在復雜介質中穩定性。
3. 耐老化與耐候性評價
紫外老化試驗(ASTM G154)及氙燈加速老化試驗(ISO 11341)模擬長期紫外線照射和溫濕度變化,檢測涂層的粉化、變色和開裂情況。濕熱循環測試(GB/T 1740)則通過交替高溫高濕與低溫干燥環境,驗證涂層的抗膨脹收縮能力。
4. 電化學性能分析
針對含鋅等金屬填料的防腐涂料,需進行電化學阻抗譜(EIS)和開路電位測試(ASTM G5),量化涂層的緩蝕效率及陰極保護性能。這些數據可預測涂層在長期服役中的失效趨勢。
5. 環保與安全性能檢測
依據IMO《船舶涂料國際標準》及各國環保法規,需檢測涂料中重金屬(如鉛、鎘)、VOC含量及生物毒性。同時,需評估涂層的阻燃性(UL94標準)與抗靜電性能,避免火災或靜電引發事故。
綜上所述,海上石油平臺防腐涂料的檢測需構建多維度、全周期的評價體系。結合實驗室模擬測試與現場監測數據,方能確保涂料的長期防護效果,為平臺安全運營提供堅實保障。隨著智能涂層技術和在線檢測設備的應用,未來防腐涂料檢測將向數字化、實時化方向發展。

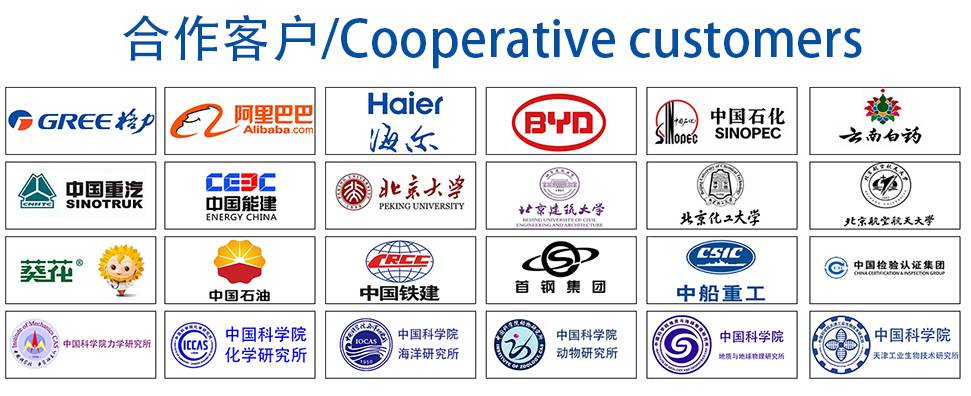