鋼質管道熔結環氧粉末外涂層檢測的重要性
鋼質管道作為石油、天然氣、化工等領域輸送介質的核心載體,其使用壽命和安全性直接關系到能源運輸系統的穩定運行。熔結環氧粉末(FBE)外涂層因其優異的防腐性能、附著力及耐化學腐蝕能力,被廣泛應用于管道外防腐工程。然而,涂層在施工、運輸及服役過程中可能因工藝缺陷、機械損傷或環境侵蝕導致性能下降。因此,針對FBE外涂層的系統化檢測是保障管道完整性、延長服役壽命的關鍵環節。通過科學的檢測手段,可及時發現涂層缺陷,評估其防護效能,為管道的維護、修復及壽命預測提供數據支持。
檢測項目及技術要求
1. 涂層厚度檢測
涂層厚度是評價防腐性能的基礎指標。依據標準(如ISO 21809-2、SY/T 0315),采用磁性測厚儀或超聲波測厚儀對管道表面進行多點測量。檢測時需覆蓋焊縫、彎頭等關鍵區域,確保厚度均勻性符合設計要求。單點最小厚度不應低于規定值的80%,平均厚度需滿足標準范圍(通常為300-500μm)。
2. 涂層附著力測試
通過劃格法或拉拔法評估涂層與鋼基體的結合強度。劃格法使用專用刀具在涂層表面劃出1mm×1mm方格,觀察涂層剝離情況;拉拔法則采用液壓或機械裝置垂直施加載荷,直至涂層脫離基材。附著力等級需達到ISO 2409標準的2級及以上,或拉拔強度不低于5MPa。
3. 針孔(漏點)檢測
利用電火花檢漏儀對涂層進行全表面掃描,檢測電壓根據涂層厚度設定(通常為3-5kV/mm)。當涂層存在針孔或裂紋時,儀器將發出報警信號并記錄缺陷位置。要求檢測漏點密度≤3個/㎡,單個漏點直徑不超過1mm。
4. 抗沖擊性能測試
模擬管道運輸及回填過程中的機械沖擊,采用落錘試驗法(如ASTM G14)。測試時設定沖擊能量(如10J),觀察涂層是否開裂或剝離。合格標準為沖擊后無可見裂紋,且漏點檢測無新增缺陷。
5. 耐化學腐蝕性檢測
通過浸泡試驗或鹽霧試驗評估涂層耐介質侵蝕能力。將試樣浸入特定濃度酸、堿或鹽溶液中(如10% H?SO?、5% NaCl),持續一定時間后檢查涂層是否起泡、脫落。依據NACE TM0174標準,要求涂層在72h內無明顯劣化現象。
6. 耐陰極剝離性能測試
模擬管道陰極保護條件下的涂層性能,按ASTM G8或GB/T 23257標準進行。在涂層表面預制人工缺陷,施加1.5V電壓并浸泡于電解液中28天,測量剝離半徑。合格標準為剝離距離≤8mm,且邊緣無分層或鼓包。
7. 外觀質量與均勻性檢驗
目視檢查涂層表面是否光滑平整,無流掛、橘皮、氣泡等缺陷。結合色差儀和光澤度儀,量化評價涂層顏色一致性與光澤度(通常要求光澤度≥60%)。對于補口區域,需重點檢查搭接處密封性及涂層連續性。
8. 綜合性能評估與報告
整合各項檢測數據,結合施工工藝、環境條件等參數,采用風險矩陣法評估涂層的整體防護等級。檢測報告需包含檢測方法、設備參數、缺陷分布圖及修復建議,為后續工程驗收或運維決策提供依據。
結語
鋼質管道FBE外涂層的系統性檢測是保障能源運輸安全的核心技術手段。通過多維度的檢測項目組合,能夠精準識別涂層缺陷、量化性能指標,從而降低管道腐蝕風險、延長使用壽命。未來,隨著智能檢測技術(如無人機巡檢、AI圖像識別)的普及,涂層檢測將向高效化、數字化方向持續發展。

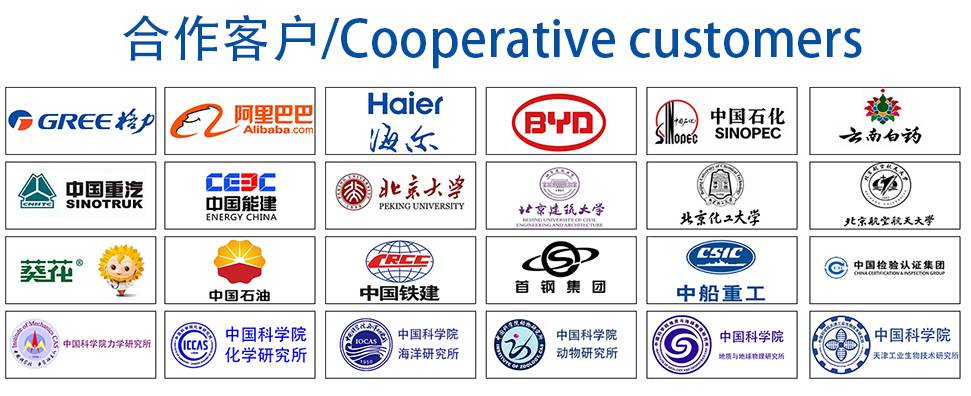