橡膠密封圈檢測:確保工業密封性能的關鍵環節
橡膠密封圈作為工業設備、汽車制造、航空航天等領域中不可或缺的密封元件,其性能直接影響設備的安全性、使用壽命和運行效率。隨著應用場景的復雜化,橡膠密封圈需在高溫、高壓、腐蝕性介質等極端條件下保持穩定密封。因此,建立科學的檢測體系對密封圈的物理性能、化學穩定性及耐久性進行全面評估,成為保障產品質量的核心環節。從原材料選擇到成品出廠,檢測項目覆蓋尺寸精度、力學特性、耐環境老化能力等多維度指標,確保密封圈滿足ISO 3601、ASTM D2000等行業標準要求。
核心檢測項目及方法解析
1. 物理性能檢測
包括尺寸公差測量(內徑、線徑、圓度)、硬度測試(邵氏A型硬度計)、拉伸強度/斷裂伸長率(萬能材料試驗機)、壓縮永久變形率(高溫壓縮裝置)等。其中壓縮永久變形率是衡量密封圈彈性恢復能力的關鍵指標,直接影響長期密封效果。
2. 耐化學介質性能檢測
通過浸泡法模擬橡膠在不同油類、酸堿溶液、溶劑中的體積變化率和硬度變化,評估材料的耐介質腐蝕能力。例如液壓油相容性測試需參照GB/T 1690標準,檢測時長通常為70小時至168小時。
3. 熱老化與耐候性檢測
熱空氣老化試驗(70°C-150°C,48-168小時)用于驗證高溫環境下密封圈性能衰減情況,紫外線老化箱則模擬戶外光照條件下的材料劣化趨勢,評估龜裂、硬化等缺陷發生概率。
4. 低溫性能測試
采用低溫脆性試驗機檢測密封圈在-40°C至-70°C環境中的柔韌性,TR試驗(溫度回縮測試)可量化材料低溫收縮后的恢復性能,避免極端寒冷工況下的密封失效。
5. 動態密封性能驗證
通過旋轉密封試驗臺模擬實際工作狀態,連續監測密封圈在交變壓力、轉速下的泄漏量及磨損情況,并結合有限元分析優化密封結構設計。
行業標準與質量控制體系
橡膠密封圈檢測需嚴格執行ISO 3601-1(流體動力系統密封件)、GB/T 3452.1(液壓氣動用O形圈)等標準。企業應建立從原料入庫(橡膠門尼黏度、硫化曲線檢測)到過程控制(模壓硫化參數監控)、成品全檢(100%氣密性測試)的完整質控鏈,同時配合第三方實驗室開展周期性型式試驗,確保產品符合UL、FDA等特殊領域認證要求。
結語
隨著智能制造技術的升級,橡膠密封圈檢測正朝著自動化(機器視覺尺寸檢測)、智能化(AI異常數據預警)方向發展。通過多維度的科學檢測與持續工藝優化,可顯著提升密封圈在新能源、半導體等高端產業的適配性,為工業設備安全運行提供可靠保障。

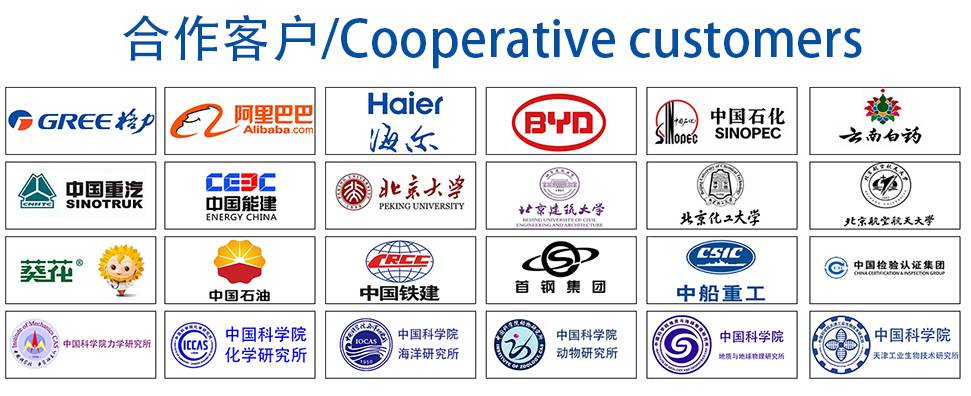