油氣輸送用鋼制感應加熱彎管檢測的重要性
在油氣長輸管道工程中,鋼制感應加熱彎管作為管道轉向的核心組件,承擔著輸送介質轉向、補償位移及適應地形變化的重要作用。其質量直接關系到管道的安全運行和使用壽命。由于彎管在制造過程中需經歷高溫加熱、塑性成形及冷卻工藝,可能產生材料性能劣化、幾何缺陷或殘余應力等問題。因此,針對油氣輸送用鋼制感應加熱彎管的檢測項目需涵蓋材料性能、工藝質量及安全可靠性等多維度指標,以確保其滿足API 5L、GB/T 29168等國內外標準要求。
關鍵檢測項目及方法
1. 材料性能檢測
包括化學成分分析(光譜檢測法)、拉伸試驗(屈服強度、抗拉強度)、沖擊韌性測試(夏比V型缺口試驗)及硬度檢測(布氏/洛氏硬度計),重點關注加熱區域與母材的性能一致性,確保彎管在高壓、低溫等工況下的力學穩定性。
2. 工藝質量檢測
通過三維激光掃描或專用量具對彎管尺寸公差(彎曲半徑、橢圓度、壁厚減薄率)進行精確測量,同時檢驗表面裂紋、褶皺等缺陷。彎曲角度偏差需控制在±0.5°以內,過渡區曲率半徑應符合設計要求。
3. 無損檢測(NDT)
采用超聲波檢測(UT)排查內部夾雜、分層缺陷;射線檢測(RT)驗證焊縫質量;磁粉檢測(MT)和滲透檢測(PT)用于表面及近表面裂紋篩查。重點檢測加熱區、背弧減薄區等高風險部位。
4. 防腐層檢測
對環氧涂層或3PE防腐層進行厚度測量(磁性測厚儀)、附著力測試(劃格法)及耐陰極剝離試驗,確保防腐體系在土壤應力、濕度變化等環境下的完整性。
5. 型式試驗與出廠檢驗
包括水壓試驗(1.5倍設計壓力保壓)、疲勞試驗(模擬交變應力)及金相組織分析(觀察奧氏體晶粒度變化)。出廠前需逐件進行外觀檢查、尺寸復核及硬度抽檢,并出具符合ASME B16.49的檢測報告。
檢測技術的發展趨勢
隨著智能管道建設的推進,數字射線成像(DR)、相控陣超聲波檢測(PAUT)等齊全技術逐步應用,結合大數據分析可實現缺陷的智能判讀。同時,殘余應力測定(X射線衍射法)和應力腐蝕試驗(慢應變速率試驗)等專項檢測,為高鋼級彎管的性能評估提供更全面支撐。

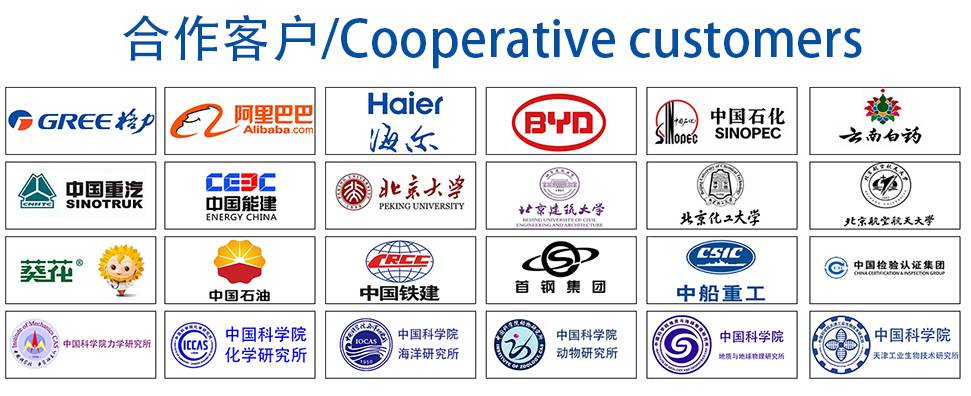