焊縫及熔敷金屬檢測的重要性
焊縫及熔敷金屬檢測是確保焊接結構安全性和可靠性的核心環節。在工業制造、建筑工程、管道輸送及壓力容器等領域中,焊縫質量直接關系到設備的承壓能力、抗疲勞性能和使用壽命。熔敷金屬作為焊接過程中形成的金屬層,其成分、力學性能和微觀組織直接影響焊縫的整體性能。因此,通過科學的檢測手段評估焊縫及熔敷金屬的質量,能夠有效避免因焊接缺陷導致的應力集中、裂紋擴展甚至結構失效,對保障工程安全、降低運維成本具有重要意義。
主要檢測項目及方法
1. 化學成分分析
通過光譜儀或化學滴定法檢測熔敷金屬的化學成分,確保其符合設計要求的合金元素比例(如C、Mn、Si等)。例如,在低合金鋼焊接中,需嚴格控制硫、磷等雜質含量以避免熱裂紋。
2. 力學性能測試
包括拉伸試驗(測定抗拉強度、屈服強度)、沖擊試驗(評估低溫韌性)及彎曲試驗(檢驗塑性變形能力)。依據標準如GB/T 2651-2008,通過試樣模擬實際工況驗證焊縫的承載能力。
3. 金相組織檢驗
采用金相顯微鏡或掃描電鏡(SEM)觀察焊縫及熱影響區的微觀組織,分析晶粒尺寸、相組成及夾雜物分布,判斷是否存在過熱、未熔合等冶金缺陷。
4. 無損檢測(NDT)
綜合應用超聲波檢測(UT)、射線檢測(RT)及磁粉檢測(MT)等技術,定位焊縫內部的裂紋、氣孔、夾渣等缺陷。例如,射線檢測可發現尺寸≥2%壁厚的體積型缺陷,靈敏度達ISO 17636標準。
5. 宏觀與微觀缺陷分析
通過宏觀腐蝕試驗(如酸蝕法)檢查焊縫截面是否存在咬邊、焊瘤等宏觀缺陷,同時結合微觀硬度測試(維氏硬度計)評估熱影響區的軟化或硬化現象。
6. 耐腐蝕性評估
針對特定工況(如海洋環境、高溫高壓),開展鹽霧試驗、晶間腐蝕試驗或應力腐蝕試驗,驗證熔敷金屬的耐蝕性能是否符合NACE MR0175等標準要求。
檢測標準與技術發展
國內外主流標準如ASME BPVC Section IX、ISO 5817及GB/T 3323-2005,均對檢測方法和驗收指標作出明確規定。近年來,隨著智能檢測技術(如相控陣超聲、數字射線成像)及大數據分析的應用,檢測效率和精度顯著提升,為焊接質量控制提供了更可靠的技術保障。

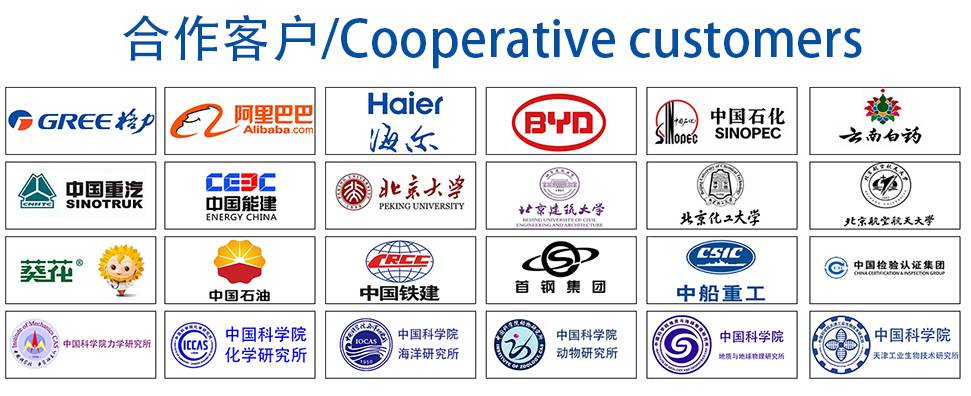