工業機器人檢測項目解析:關鍵技術與應用價值
隨著智能制造時代的加速到來,工業機器人已廣泛應用于汽車制造、3C電子、食品加工等領域。作為現代工廠的"核心勞動力",機器人系統運行的精度、穩定性和安全性直接關系到生產效率和產品質量。據國際機器人聯合會(IFR)數據顯示,2022年工業機器人安裝量突破51.7萬臺,但仍有23%的企業因機器人性能問題導致產線停擺。這凸顯了工業機器人檢測作為質量保障體系的重要性,通過系統化檢測可有效預防設備故障,延長使用壽命,降低維護成本達40%以上。
核心檢測維度與技術方案
現代工業機器人檢測體系包含五大關鍵模塊:
1. 運動精度檢測
采用激光跟蹤儀配合六維力傳感器,對重復定位精度進行μm級測量。依據ISO 9283標準,在負載狀態下檢測TCP(工具中心點)的空間軌跡偏差。某汽車焊裝線實測顯示,經過校準的機器人焊接軌跡誤差從±0.15mm降至±0.03mm。
2. 動態性能測試
通過多普勒振動分析儀和高速攝像系統,捕捉機械臂在最大加速度下的振動頻譜。某SCARA機器人經諧波減速器振動檢測,發現200Hz異常諧波,及時更換減速器齒輪避免批量質量事故。
3. 安全功能驗證
基于IEC 61508安全標準,對急停響應時間、碰撞檢測靈敏度進行測試。某協作機器人通過三維力覺傳感器陣列驗證,在接觸力超過150N時可在0.1秒內完成急停。
4. 環境適應性檢測
在溫濕度綜合試驗箱中模擬-20℃至60℃極限工況,檢測密封件的耐候性能。某食品行業碼垛機器人經72小時鹽霧測試后,腕部軸承防護等級從IP54提升至IP67。
5. 通信與軟件測試
使用PROFINET/EtherCAT協議分析儀,驗證控制系統的實時響應性能。某半導體搬運機器人經總線周期測試,將通訊抖動從±15μs優化至±2μs,提升晶圓傳輸合格率3個百分點。
檢測技術演進與行業實踐
當前檢測技術正朝著智能化方向發展,基于數字孿生的預測性維護系統已開始應用。某家電企業通過部署振動傳感器網絡,結合機器學習算法,提前48小時預警減速器故障,減少停機損失280萬元/年。第三方檢測機構的數據顯示,經過系統檢測的工業機器人平均無故障時間(MTBF)可達6萬小時,較未檢測設備提升65%。
隨著工業4.0的深入實施,機器人檢測已從單一設備檢測發展為整線智能診斷。建議企業在選擇檢測服務時,優先考慮具備CMA/ 資質的機構,并建立全生命周期檢測檔案,為智能制造轉型提供可靠的技術保障。

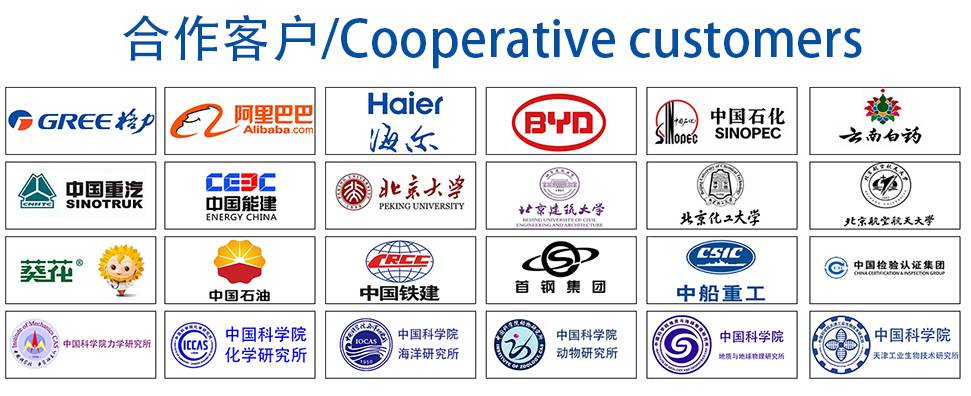