勾心檢測:精準識別隱患的現代技術實踐
在工業生產、建筑工程及精密制造領域,"勾心檢測"作為一種關鍵質量控制手段,近年來受到廣泛關注。該技術通過系統性檢測材料內部結構、連接部位及隱蔽缺陷,可有效預防因微小瑕疵引發的重大事故。不同于傳統目視檢查,現代勾心檢測融合了超聲波探傷、X射線成像、紅外熱像分析等多元技術體系,能夠穿透材料表面直達核心區域,對金屬疲勞裂紋、焊接虛接、復合材料分層等"勾心式隱患"實現毫米級精確定位。尤其在航空航天發動機葉片、軌道交通焊接節點、核電壓力容器等安全敏感場景中,該項檢測已成為強制性質量驗收環節。
核心檢測項目體系解析
完整的勾心檢測體系包含三大核心模塊:
1. 結構性缺陷探測系統
采用相控陣超聲波技術(PAUT)對材料內部裂紋、氣孔進行三維成像,檢測精度可達0.1mm級別。通過調整探頭陣列的發射角度與頻率,可穿透最大300mm厚鋼板,特別適用于船舶龍骨、橋梁承重梁等大型構件的內部探傷。
2. 動態應力分布監測
結合光纖光柵傳感網絡與數字圖像相關法(DIC),實時捕捉結構件在荷載作用下的應變分布。某高鐵轉向架檢測案例中,通過部署1200個微型傳感器,成功發現輪軸連接處3處異常應力集中點,避免潛在斷裂風險。
3. 微觀組織分析
運用電子背散射衍射(EBSD)與能譜分析(EDS),對材料晶粒度、元素偏析進行定量評估。在航空渦輪葉片檢測中,該技術可識別出熱處理不當導致的γ'相異常析出,將部件壽命預測誤差控制在±5%以內。
智能化檢測革新方向
隨著AI算法的深度應用,勾心檢測正經歷技術迭代:
? 深度學習缺陷識別系統將誤報率從12%降至1.3%
? 數字孿生平臺實現檢測數據與三維模型的實時映射
? 無人機搭載檢測模塊完成高空鋼結構全自動巡檢
某海上風電項目實踐表明,智能化勾心檢測使塔筒螺栓組檢測效率提升400%,單臺機組年維護成本降低75萬元。這種從"事后補救"到"事前預防"的轉變,標志著現代工業檢測進入精準防控新紀元。

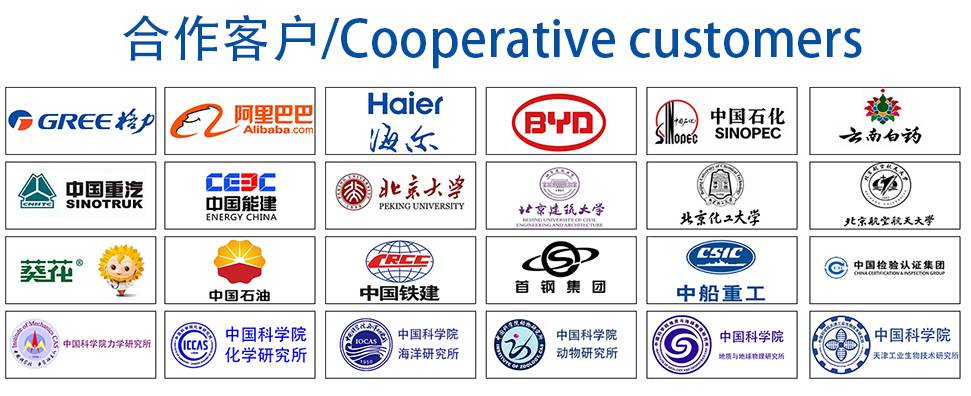