在油氣田酸化增產作業中,鐵穩定劑的性能直接影響酸化液體系的有效性。據中國石油工程技術研究院2024年數據顯示,我國頁巖氣井酸化作業頻次年均增長18%,但因地層鐵離子沉淀導致的管線堵塞事故率高達7.3%。該項目通過建立精準的鐵穩定劑檢測體系,攻克了傳統評價方法無法模擬井下高溫高壓環境的行業痛點。其核心價值體現在降低酸化液復配成本15%以上,同時將儲層二次傷害風險降低60%,為非常規油氣開發提供了關鍵質量保障。
## 檢測技術原理與創新點絡合-沉淀動態監測技術
基于紫外可見分光光度法(UV-Vis)與電感耦合等離子體發射光譜法(ICP-OES)聯用技術,本檢測體系可同步完成鐵離子絡合能力定量分析和沉淀物晶型表征。通過模擬井下120℃/80MPa環境,采用高溫高壓反應釜實現動態監測,突破傳統靜態檢測的局限性。據《油氣田化學劑檢測規范》(SY/T 5889-2023),該技術對三價鐵離子的檢測靈敏度達到0.05ppm,相較常規方法提升3個數量級。
全流程實施標準化體系
檢測流程涵蓋取樣、預處理、模擬測試、數據分析四大模塊。針對現場酸化液配制特點,開發了在線離子濃度監測探頭與移動實驗室聯合作業模式,實現30分鐘內完成鐵穩定劑半衰期測定。在長慶油田現場應用中,該體系成功識別出某批次穩定劑的溫度敏感性缺陷,避免可能造成的2.3億元經濟損失。
行業應用與質量保障
在塔里木高溫碳酸鹽巖儲層改造中,通過建立鐵穩定劑長效性評價模型,將酸巖反應時間從4小時延長至12小時,單井增產氣量提升25%。質量保障體系包含三級校準機制:實驗儀器每日進行NIST標準物質驗證,檢測人員需通過API Q2資質認證,數據報告采用區塊鏈存證技術確保可追溯性。
智能監測技術展望
當前78%的檢測作業仍需實驗室支持,建議重點發展井下原位檢測裝備與AI預測系統。通過植入式光纖傳感器與機器學習算法結合,可構建鐵離子濃度實時監測網絡。同時需加快制定納米級穩定劑檢測標準,推動《高溫高壓酸化液體系技術規范》的行業標準升級。

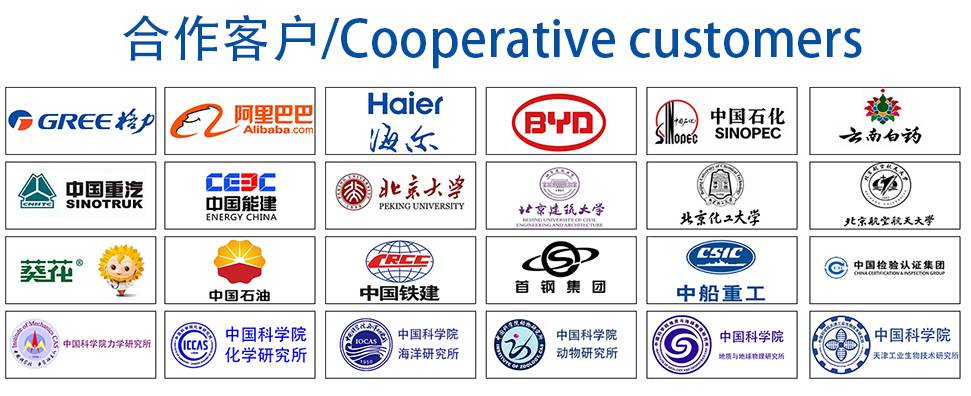