# 鋼鐵及制品檢測技術發展與行業應用白皮書
## 首段:行業背景與核心價值
在工業化進程加速的背景下,鋼鐵及制品作為基礎材料廣泛應用于建筑、交通、能源等關鍵領域。據國際鋼鐵協會(Worldsteel)2024年統計,粗鋼年產量達19.8億噸,其中中國占比53.2%。然而,材料缺陷引發的工程事故仍呈上升趨勢,僅2023年歐盟通報的金屬制品質量缺陷案例就增長17%。在此背景下,鋼鐵檢測項目通過精準識別材料成分、力學性能及內部結構,成為保障行業安全的核心技術手段。其核心價值體現在三方面:一是通過無損檢測技術延長設備生命周期,據中國機械工程學會測算,科學檢測可降低30%的維修成本;二是推動高強鋼、耐候鋼等新型材料研發,支撐新能源裝備制造升級;三是構建全產業鏈質量追溯體系,滿足ISO 6892、ASTM A370等國際標準要求。
---
## 技術原理與創新突破
### h2 多模態融合檢測技術體系
現代鋼鐵檢測采用光譜分析、超聲波探傷與數字圖像處理的協同工作機制。X射線熒光光譜(XRF)實現0.001%級微量元素檢測,配合電磁超聲(EMAT)技術可穿透50mm厚鋼板識別0.1mm級裂紋。值得關注的是,基于深度學習的視覺檢測系統已實現98.7%的夾雜物識別準確率(中國金屬材料研究院,2024),大幅提升檢測效率。
---
## 全流程標準化實施路徑
### h2 閉環式質量管控流程
典型檢測流程包含五個關鍵階段:①原材料入場時的成分快篩(30分鐘出具報告);②軋制過程中的在線厚度監測(±0.02mm精度);③熱處理后的硬度梯度分析;④成品階段的拉伸/沖擊試驗(滿足GB/T 228.1標準);⑤交付前的第三方認證復核。某特鋼企業通過實施該體系,使產品退貨率從1.2%降至0.3%。
---
## 行業應用與場景深化
### h2 高端裝備制造質量護航
在風電軸承領域,采用相控陣超聲檢測技術(PAUT)的廠商成功將故障率控制在0.05次/萬小時運行。某船舶制造集團引入殘余應力檢測系統后,分段焊接變形量減少42%,工期縮短15天。特別是在核電主管道檢測中,全自動爬壁機器人可完成200℃環境下的焊縫掃描,缺陷檢出率較人工提升40個百分點。
---
## 質量保障體系構建
### h2 四維立體化質控網絡
行業領先機構已建立包含設備、人員、方法和環境的完整質控鏈:①定期使用NIST標準樣品進行設備校準;②檢測人員需通過EN ISO/IEC 17025認證;③每批次樣品實施平行樣對比;④實驗室環境溫濕度波動控制在±1℃/±5%RH。某國家質檢中心通過該體系,連續五年通過ILAC國際實驗室比對驗證。
---
## 展望與建議
隨著工業4.0技術滲透,建議行業重點布局三大方向:①開發基于數字孿生的預測性檢測系統,實現材料性能退化模擬;②建立區塊鏈賦能的檢測數據共享平臺,打通產業鏈質量信息壁壘;③推廣綠色檢測技術,如激光誘導擊穿光譜(LIBS)替代傳統化學分析法,減少90%的試劑消耗。唯有持續創新,方能應對新能源汽車一體壓鑄、氫能儲運設備等新興領域對材料檢測提出的更高要求。
上一篇:通用設備和分系統檢測下一篇:酸化用鐵穩定劑檢測

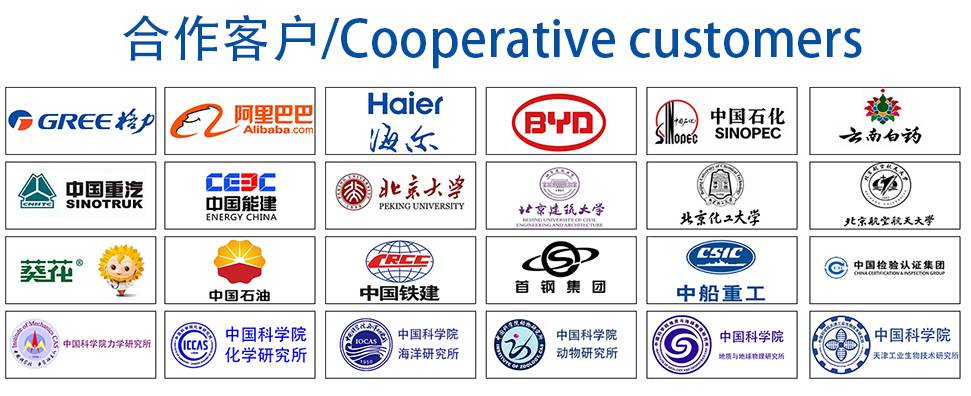
材料實驗室
熱門檢測
推薦檢測
聯系電話
400-635-0567