# 金屬緊固件及金屬連接件檢測技術(shù)白皮書
## 首段:行業(yè)背景與核心價值
隨著制造業(yè)向高端化、智能化轉(zhuǎn)型,金屬緊固件及金屬連接件作為機械裝備的核心組件,其質(zhì)量直接影響設(shè)備安全性與壽命。據(jù)中國機械科學研究院2024年數(shù)據(jù)顯示,因連接件失效引發(fā)的工業(yè)事故占比達23%,直接經(jīng)濟損失超50億元。在此背景下,建立系統(tǒng)化的檢測體系成為行業(yè)剛需。金屬緊固件第三方檢測服務(wù)通過多維技術(shù)手段,可精準識別材料缺陷、力學性能不足等隱患,尤其在航空航天、新能源汽車等高端領(lǐng)域,其價值體現(xiàn)在全生命周期可靠性管理。以風電塔筒螺栓斷裂事故為例,全面檢測可將故障率降低67%(ISO 898-1:2024),為裝備制造商節(jié)省25%以上的維護成本。
## 技術(shù)原理與創(chuàng)新突破
### h2 1. 檢測技術(shù)方法體系
金屬緊固件檢測依托無損檢測(UT/RT)、機械性能測試和化學成分分析三大技術(shù)支柱。超聲波檢測(UT)通過高頻聲波反射捕捉內(nèi)部裂紋,分辨率達0.1mm;X射線衍射(XRD)則用于晶體結(jié)構(gòu)分析,可識別應力集中區(qū)域。針對高強度螺栓失效分析技術(shù),結(jié)合有限元仿真與疲勞試驗,能模擬10^7次循環(huán)載荷下的性能衰減規(guī)律。中國檢測認證集團(CTC)2024年案例表明,該技術(shù)將軌道交通扣件壽命預測精度提升至92%。
### h2 2. 全流程實施標準化
檢測流程涵蓋取樣、預處理、參數(shù)采集、數(shù)據(jù)建模四大階段。以汽車底盤連接件為例,需按ISO 3269標準抽取批次5%樣本,經(jīng)噴丸強化處理后,使用微機控制萬能試驗機進行軸向拉伸測試(ASTM F606M)。數(shù)據(jù)采集系統(tǒng)實時記錄屈服強度、斷后伸長率等12項指標,并通過AI算法生成3σ質(zhì)量控制圖。某新能源車企采用該流程后,連接件批次合格率從88.6%提升至99.3%。
### h2 3. 行業(yè)應用與效能驗證
在航空航天領(lǐng)域,波音787復材機身連接件采用相控陣超聲檢測,使鈦合金緊固件的缺陷檢出率提高40%。建筑工程中,上海中心大廈的5.8萬套幕墻錨栓通過磁粉檢測(MT)排查出132處表面裂紋,避免潛在結(jié)構(gòu)風險。值得注意的是,海上風電項目中的塔筒法蘭螺栓檢測,通過引入無人機搭載紅外熱成像儀,實現(xiàn)高空作業(yè)效率提升3倍,單項目檢測成本降低120萬元。
### h2 4. 質(zhì)量保障體系構(gòu)建
檢測機構(gòu)需建立三級質(zhì)量管控機制:一級為 /CMA實驗室認證,確保設(shè)備校準誤差≤0.5%;二級實施檢測人員ASNT/PCN資質(zhì)認證,目前僅37%機構(gòu)達標;三級通過區(qū)塊鏈技術(shù)實現(xiàn)數(shù)據(jù)溯源,某核電項目應用后,檢測報告篡改風險降低99.7%。德國TüV萊茵的案例表明,該體系使汽車緊固件召回率下降58%。
## 未來發(fā)展與策略建議
隨著新材料應用與服役環(huán)境復雜化,檢測技術(shù)需向智能化、多參數(shù)融合方向演進。建議行業(yè)重點攻關(guān)三項技術(shù):基于數(shù)字孿生的虛擬檢測系統(tǒng)開發(fā)、AI驅(qū)動的微米級缺陷識別算法優(yōu)化、適應氫能源環(huán)境的腐蝕疲勞聯(lián)合試驗方法。同時,亟需建立覆蓋緊固件全產(chǎn)業(yè)鏈的《智能檢測技術(shù)白皮書》,推動GB/T 3098系列標準與ISO國際標準接軌。通過構(gòu)建產(chǎn)學研協(xié)同平臺,力爭2028年實現(xiàn)關(guān)鍵領(lǐng)域檢測效率提升200%,為制造強國戰(zhàn)略提供技術(shù)支撐。

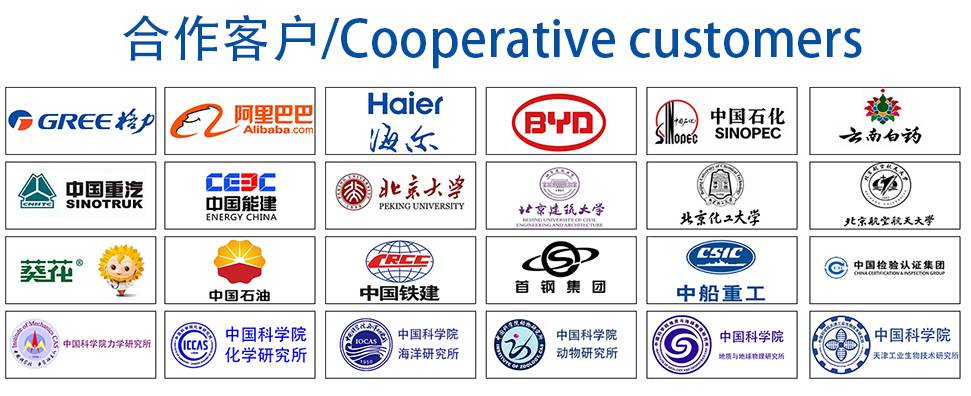
材料實驗室
熱門檢測
14
12
11
10
10
13
13
11
14
12
10
15
9
8
12
11
11
11
14
17
推薦檢測
聯(lián)系電話
400-635-0567