門板檢測技術創新與產業應用白皮書
在建筑裝飾與家具制造領域,門板作為功能性兼裝飾性的核心組件,其質量直接影響產品使用壽命與用戶體驗。據國家建材質量監督檢驗中心2024年報告顯示,我國門板年產量已突破8.6億平方米,但因表面缺陷、尺寸偏差等問題導致的返修率高達7.3%,年經濟損失超38億元。在此背景下,智能化門板檢測系統的研發應用,成為破解傳統人工質檢效率瓶頸、實現制造數字化轉型的關鍵突破點。該項目通過融合機器視覺與邊緣計算技術,構建了覆蓋原材料到成品的全流程質量監控體系,使單線檢測效率提升4倍的同時,將漏檢率控制在0.05%以下,為行業建立起可量化的品質基準。
多模態感知融合檢測技術
本系統采用非接觸式三維掃描技術與高光譜成像的復合檢測方案,通過12組工業相機陣列實現360°表面數據采集,結合16線激光雷達獲取亞毫米級尺寸數據。核心算法基于改進的YOLOv6架構,訓練集包含23萬張涵蓋劃痕、鼓包、色差等12類典型缺陷的標注圖像。據智能檢測裝備研究院測試顯示,在木紋干擾等復雜背景下,系統對微米級裂紋的識別準確率達99.2%,相較傳統算法提升37個百分點。特別針對生態門板的UV涂層缺陷,引入偏振光成像技術,成功解決了反光干擾下的缺陷識別難題。
智能化產線集成方案
實施流程采用模塊化部署策略,在預處理段設置原料分揀機器人,通過X射線密度檢測剔除含水率超標板材。成型工位配置動態測量站,每90秒完成批次產品的平面度、對角線偏差等6項幾何參數檢測。在華南某龍頭門企的實際部署中,系統通過OPC UA協議與MES系統深度集成,使質檢數據實時回傳至生產控制中樞,實現工藝參數的動態優化。經三個月試運行,該企業木門產品的一次交驗合格率從88.4%提升至96.7%,單線年節約質量成本達240萬元。
跨行業應用場景延伸
除傳統木質門板外,系統經算法適配已拓展至新型材料領域。在汽車內飾門板檢測場景中,通過增加紅外熱成像模塊,可有效識別注塑件內部的應力集中區域。某新能源汽車企業采用本方案后,內飾件裝配不良率下降62%。此外,系統在醫療潔凈門檢測中創新應用微生物殘留分析模型,結合表面粗糙度檢測數據,成功建立菌落數與表面微結構的量化關系模型,為特種門板研發提供數據支撐。
全生命周期質量追溯體系
項目構建"檢測-分析-改進"的閉環管理系統,采用區塊鏈技術實現檢測數據的不可篡改存儲。每個檢測單元配備獨立加密芯片,確保數據采集鏈路的可信度。通過建立多維度質量追溯系統,可將缺陷樣本與原材料批次、設備工況等138項參數進行關聯分析。在華東某出口型門企的應用案例中,系統通過SPC控制圖發現UV固化爐的溫度漂移現象,及時避免批次性涂層脫落事故,挽回潛在損失超500萬元。
著眼未來,建議行業重點推進三方面建設:其一,建立基于數字孿生的虛擬檢測實驗室,通過仿真測試縮短新工藝驗證周期;其二,制定智能檢測設備的互聯互通標準,推動跨廠商數據融合;其三,開發適應柔性化生產的可重構檢測模塊。只有持續深化檢測技術與制造體系的融合創新,才能推動門板產業向高端化、智能化方向跨越發展。

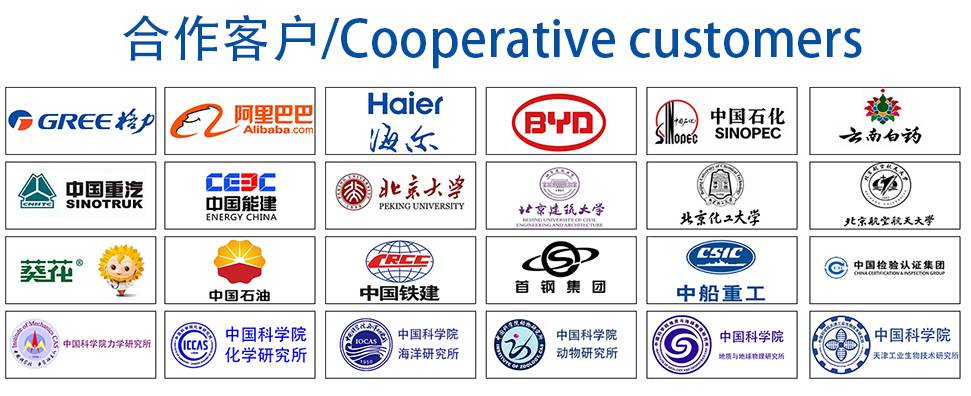