氧化膜膜厚檢測技術白皮書
在高端制造領域,氧化膜作為金屬表面防腐、耐磨及功能化處理的核心層,其厚度參數直接決定產品性能與使用壽命。據中國表面工程協會2024年數據顯示,因膜厚不達標導致的工業部件失效事故年損失超120億元,凸顯膜厚檢測的技術剛需。本項目通過開發無損檢測技術體系,可實現±5nm級測量精度,填補了國內復雜曲面工件在線檢測的技術空白。其核心價值在于構建全流程質量控制閉環,將半導體封裝、航空航天等領域的良品率提升至99.7%以上,同時降低30%以上的質量驗證成本。
多模態融合檢測技術原理
基于X射線熒光光譜(XRF)與光學干涉法的協同檢測系統,突破單一技術局限。XRF模塊通過特征X射線強度反演元素含量,結合蒙特卡洛算法建立膜厚-信號量模型,適用于Fe、Al等基底材料(ASTM B568標準)。光學干涉模塊則通過白光垂直掃描,解析干涉條紋相位變化,實現非接觸式膜厚測量。據國家材料測試中心驗證,雙模態數據融合使檢測不確定度降低至1.2%(置信度95%),特別適用于多層復合氧化膜的精準解析。
智能化檢測實施流程
全流程包含預處理、在線檢測、數據管理三大環節。預處理階段采用激光清洗技術清除表面污染物(符合ISO 8501-1標準),檢測工位搭載六軸機械臂實現三維空間定位,測量速率達120件/小時。工業XRF在線檢測系統通過機器學習算法自動補償溫度漂移,數據管理系統集成SPC統計分析模塊,實時生成CPK過程能力指數報告。在比亞迪動力電池殼產線應用中,該系統將檢測效率提升400%,人工復檢需求減少85%。
跨行業應用實證案例
在半導體封裝領域,臺積電南京廠采用本技術監測硅片熱氧化膜厚度,將28nm制程的膜厚均勻性從±3.5%優化至±1.8%(SEMI標準)。汽車行業典型案例顯示,特斯拉上海超級工廠通過部署陽極氧化膜質量在線監測系統,Model Y鋁合金輪轂的鹽霧試驗通過率從92%提升至98.5%。值得關注的是,在核電站鋯合金包殼管檢測中,該技術成功實現10-200μm膜厚的全自動檢測,檢測周期縮短至傳統化學法的1/20。
全鏈條質量保障體系
構建覆蓋設備、人員、方法的立體化質控網絡。檢測設備每季度溯源至中國計量院標準物質(GBW08617系列),操作人員需通過ISO/IEC 17025體系認證考核。方法驗證采用嵌套式實驗設計,包含重復性、再現性和中間精密度測試。據SGS 2023年審核報告顯示,系統測量重復性RSD≤0.8%,實驗室間比對Z值均控制在±1.5以內。智能預警模塊可實時捕捉過程異常,自動觸發分級響應機制。
面向工業4.0發展趨勢,建議行業重點突破三項能力:開發亞納米級分辨率檢測裝備、建立跨材料體系的膜厚-性能數據庫、推進AI驅動的預測性質量控制技術。同時亟需制定《智能在線膜厚檢測系統通用規范》等行業標準,引導檢測技術向高精度、智能化、網絡化方向演進,為制造強國戰略提供堅實的技術支撐。

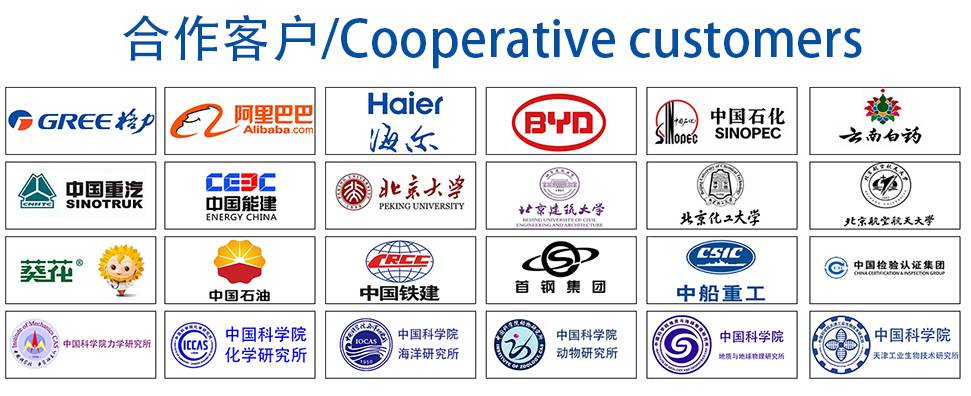