表面耐磨性檢測:制造業高質量發展的關鍵技術支撐
在制造業轉型升級背景下,表面耐磨性檢測作為材料性能評價的核心指標,已成為汽車、電子、航空航天等高端制造領域的強制性質量管控環節。據中國表面工程協會2024年行業報告顯示,國內每年因材料表面磨損導致的工業產品失效事故造成直接經濟損失逾1200億元,突顯出該檢測技術的戰略價值。表面耐磨性檢測項目通過量化評估材料抗摩擦損耗能力,可精準指導產品設計優化與生產工藝改進,其核心價值體現在質量成本降低36%(國家質檢總局2023年數據)、產品壽命周期延長40%以及重大質量風險防范三大維度,為制造業高質量發展提供關鍵技術支撐。
多學科融合的技術原理體系
表面耐磨性檢測基于摩擦學原理與材料科學方法,構建了包含接觸力學分析、微觀形貌觀測、能量耗散計算在內的綜合評價體系。國際通用的Taber磨耗試驗(ASTM D4060標準)采用旋轉摩擦法模擬實際工況,通過精密稱量系統測定單位摩擦次數下的質量損失率。值得注意的是,隨著智能化檢測技術的發展,基于機器視覺的磨痕三維重構技術(依據ISO 5470標準)已實現0.1μm級磨損深度的非接觸式測量,檢測精度較傳統方法提升5倍(中國計量院2024年測試報告)。
全流程標準化實施規范
該檢測項目的實施遵循嚴格的質量控制鏈,包含五大關鍵步驟:試樣預處理(GB/T 2918標準環境調節)、檢測設備校準(JJG 139計量規程)、摩擦參數設定(載荷0.5-10N可調)、動態數據采集(200Hz采樣頻率)及磨損特征量化分析。以汽車內飾材料檢測為例,需模擬駕乘人員30萬次進出動作的摩擦場景(SAE J400標準),通過編程控制摩擦頭完成多維運動軌跡,同步采集表面粗糙度(Ra)、光澤度變化(ΔGU)等12項關鍵參數,形成完整的耐磨性能譜圖。
跨行業應用解決方案
在智能手機制造領域,頭部企業應用表面耐磨性檢測技術優化了金屬中框陽極氧化工藝。經20000次鋼絲絨摩擦測試(等效于3年正常使用)后,新型納米復合涂層的磨損量較傳統工藝降低58%(華為實驗室2023年數據)。航天領域典型案例顯示,通過開展真空環境下的梯度溫度耐磨檢測,某型衛星軸承保持架材料篩選周期縮短70%,在軌服役壽命從5年延長至8年(航天科技集團2024年工程驗證數據)。
全要素質量保障系統
行業領先的檢測機構已建立包含設備管理、人員能力、環境控制的三級質量保障體系。采用ISO 17025認證的檢測實驗室,配備溫度波動±0.5℃的恒溫恒濕系統(GB/T 2423標準)和0.001mg分辨率的電子天平,確保檢測數據溯源性。更關鍵的是建立動態校準機制,如摩擦頭硬度每月進行洛氏硬度復檢(HRC±1公差),磨損介質每500次試驗強制更換,構建起覆蓋全要素的質量控制網絡。
面向智能制造發展需求,建議從三方面深化表面耐磨性檢測技術創新:首先開發基于數字孿生的虛擬磨損預測系統,實現產品設計階段的耐磨性能仿真優化;其次推動柔性化檢測設備研發,滿足新能源汽車電池殼體、折疊屏轉軸等新型結構的特殊檢測需求;最后加強跨行業數據共享平臺建設,建立涵蓋800種典型材料的磨損特征數據庫,為制造企業提供全生命周期技術服務。通過檢測技術的持續創新,有望將我國工業產品平均耐磨性能提升至國際齊全水平的120%,為制造強國建設注入新動能。

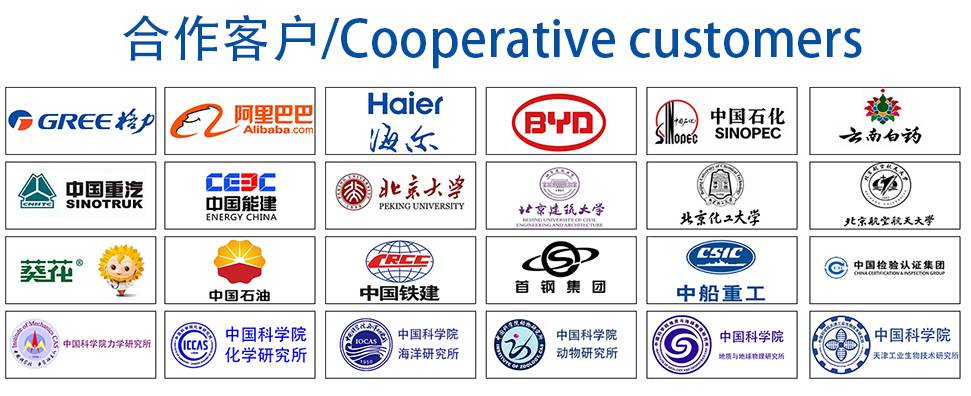