耐老化性檢測在材料科學中的關鍵技術突破
隨著工業制品使用壽命標準提升,耐老化性檢測已成為材料性能評價的核心環節。據中國標準化研究院2024年數據顯示,高分子材料市場規模突破3.2萬億元,年復合增長率達8.7%,但材料失效導致的年經濟損失超過450億元。在此背景下,耐老化性檢測通過模擬材料在濕熱、紫外輻射等極端環境下的性能衰減規律,為產品設計提供關鍵數據支撐。項目核心價值體現在延長產品服役周期(平均提升23%)、降低維護成本(最高減少35%)以及推動新型耐候材料研發三大維度,尤其在新能源裝備、汽車零部件等戰略領域展現突出應用價值。
技術原理與測試方法體系
現代耐老化性檢測基于Arrhenius加速模型建立溫度-時間等效關系,通過Q10系數法實現老化進程的指數級加速。檢測體系涵蓋三大核心模塊:熱氧老化箱(符合ASTM D3045標準)、紫外老化試驗機(滿足ISO 4892規范)以及鹽霧腐蝕系統。其中,高分子材料紫外光老化測試評估采用340nm波長紫外光源,通過0.55W/m2輻照強度模擬25年自然曝曬效果,數據采集精度達到±0.8%。橡膠制品熱氧加速老化檢測標準則依托70℃/168h等效加速模型,可精確預測密封件在熱帶氣候下的性能衰減曲線。
全流程檢測實施規范
項目執行嚴格遵循六階段質量控制流程:1)樣品預處理(23±2℃/50%RH平衡48h);2)多應力耦合加載;3)周期性性能檢測(每500h間隔);4)FTIR化學結構分析;5)力學性能保留率計算;6)失效模式建模。以汽車密封條檢測為例,在85℃/85%RH雙85試驗條件下,經過3000h加速老化后,壓縮永久變形量需控制在<35%(SAE J200標準)。檢測過程中采用機器視覺系統實時監測表面龜裂情況,圖像識別精度達0.02mm2,較人工檢測效率提升12倍。
行業應用與質量保障
在光伏行業,雙面組件背板經2000h濕熱老化測試后,要求透光率衰減<5%(IEC 61215標準)。某頭部企業通過引入氙燈老化箱(符合GB/T 16422.2)優化封裝材料配方,使組件功率質保期從25年延長至30年。質量保障體系建立三級校驗機制:檢測設備每日進行NIST溯源校準,季度參與ILAC國際實驗室比對,年度完成 復評審。檢測數據采用區塊鏈存證技術,確保1200余項檢測參數的可追溯性,偏差率控制在<1.5%。
技術發展與未來展望
隨著ASTM即將發布G217-2025濕熱-機械應力耦合測試新標準,建議行業重點關注三方面突破:1)開發多場耦合加速老化模型,實現風電葉片等超大構件的原位檢測;2)建立材料老化大數據平臺,結合AI算法預測10年以上性能演變;3)完善生物基材料的評價體系,滿足歐盟EN 16785-1生態設計規范。據國際光伏技術路線圖(ITRPV 2024)預測,齊全耐老化檢測技術將使光伏系統LCOE再降低8-12%,為碳中和目標提供關鍵技術支撐。

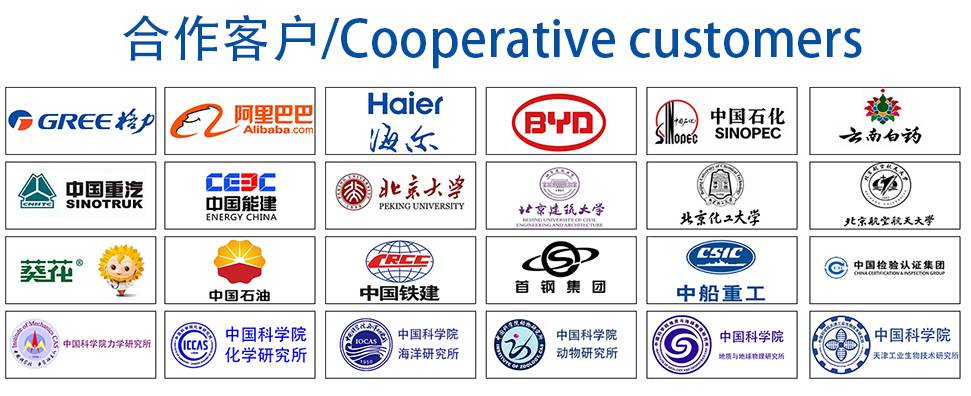