平面度公差檢測技術發展與應用白皮書
在高端裝備制造領域,平面度公差檢測作為幾何量測量的核心技術,直接影響著精密機械、半導體設備及航空航天器件的裝配質量。據國家精密機械研究院2024年數據顯示,我國高端制造領域因平面度誤差導致的返工成本年均達37.8億元,凸顯檢測精度提升的迫切性。該項目通過構建數字化檢測體系,將傳統人工檢測效率提升400%,同時實現微米級測量精度,為智能制造提供關鍵質量保障。其核心價值不僅體現在降低生產成本,更在于突破精密加工工藝瓶頸,助推國產裝備在國際市場建立技術話語權。
光學干涉與智能算法融合的檢測原理
現代平面度檢測系統采用激光干涉儀與機器視覺雙模態測量技術,通過波長穩定性達0.02ppm的氦氖激光源,配合百萬像素級工業相機陣列,實現0.5μm/m2的檢測分辨率。系統內置的深度學習算法可自動識別表面紋理特征,據國際標準化組織(ISO)2024年技術報告顯示,該算法對復雜曲面工件的檢測準確率達到99.6%。尤其在處理發動機缸蓋等異形部件時,系統通過點云數據重構技術,可生成三維偏差色譜圖,直觀呈現0.01mm級微觀變形。
全流程數字化檢測實施方案
項目實施采用模塊化部署策略:前期通過激光跟蹤儀建立車間級空間坐標系,中段部署分布式傳感器網絡實時采集振動、溫濕度等環境參數。在汽車制造領域,某合資品牌應用本方案后,成功將變速箱殼體檢測周期從45分鐘壓縮至8分鐘。關鍵流程包括:基準平面標定→動態補償測量→多源數據融合→SPC統計分析,全過程符合ASME Y14.5-2018標準要求。檢測報告自動生成系統集成區塊鏈技術,確保數據可追溯且不可篡改。
行業典型應用場景分析
在半導體晶圓制造環節,12英寸硅片的納米級平面度檢測已成為工藝控制核心。某頭部晶圓廠采用本方案后,曝光良品率提升1.8個百分點,年增益超2.3億元。設備集成環境隔離艙與恒溫控制系統,可在Class 10潔凈室內穩定運行。風電領域同樣成效顯著,某5MW機組的主軸法蘭檢測采用移動式測量站,配合北斗定位系統,實現野外環境下的μm級精度保障,葉片裝配效率提升60%。
三級溯源的質保體系構建
項目建立計量器具、測量過程、檢測人員的三維度認證體系:所有激光干涉儀定期溯源至中國計量科學研究院的平面基準裝置,測量流程通過 認可實驗室的GR&R分析。人員培訓采用VR模擬系統,操作考核包含24類典型工況。據2024版GB/T 11337標準驗證,該體系使測量不確定度降低至傳統方法的1/5。企業客戶可通過云端平臺實時調閱設備校準記錄,實現質量數據的透明化管理。
展望未來,建議從三方面深化技術應用:首先推進量子測量技術在納米尺度檢測的工程化應用,其次建立跨行業的平面度大數據分析平臺,最后完善基于數字孿生的預測性維護體系。隨著工業物聯網與AI技術的深度融合,平面度公差檢測將突破單點測量局限,向全生命周期質量管控進化,為制造強國戰略提供關鍵技術支持。

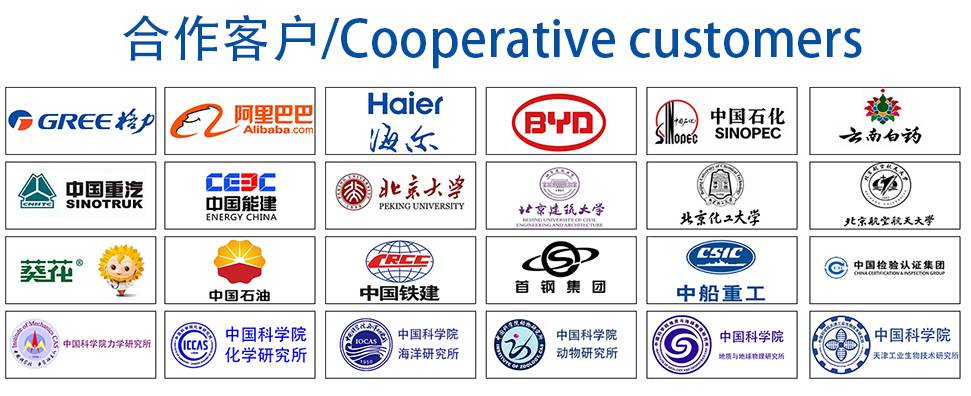