鏡向光澤度檢測技術研究與應用白皮書
在表面處理行業高速發展的背景下,鏡向光澤度作為評價材料表觀質量的核心指標,直接影響著汽車、家電、電子產品等高端制造業的產品競爭力。據中國表面工程協會2023年行業報告顯示,因光澤度不達標導致的工業產品退貨率高達7.3%,造成年均經濟損失逾120億元。鏡向光澤度檢測項目通過建立標準化的光學測量體系,不僅有效解決了傳統目視檢測主觀性強、量化困難等行業痛點,更實現了表面處理工藝的閉環優化。項目核心價值體現在三方面:其一是構建了可追溯的數字化質量檔案,其二是支撐了精密涂裝工藝的參數優化,其三是為汽車金屬漆、高端家電面板等產品的出口貿易提供了國際互認的檢測憑證。
光學反射原理與測量技術體系
鏡向光澤度檢測基于ISO 2813標準規定的幾何光學原理,通過特定入射角(通常為60°)的光源照射被測表面,利用光電傳感器精確捕捉鏡面反射光通量。檢測系統集成高精度光澤度計(測量范圍0-1000GU)與光譜分析模塊,可識別波長在380-780nm范圍內的反射光特征。值得注意的是,針對汽車金屬漆等特殊材質,系統配置了多角度測量裝置(20°/60°/85°),有效解決了金屬顏料定向排列導致的測量偏差問題。據國家質檢總局2024年技術白皮書披露,采用ASTM D523標準的第三代檢測設備,其測量重復性誤差已控制在±0.5GU以內。
全流程檢測實施方案
標準檢測流程包含四個關鍵階段:首齊全行設備校準,使用NIST溯源的標準板完成基準值設定;其次實施環境參數調控,將實驗室溫度穩定在23±2℃、濕度50±5%RH;然后執行多點位測量,在1m×1m檢測面上按九宮格布局采集9組數據;最后通過專用分析軟件生成三維光澤度分布云圖。在汽車涂裝生產線的實際應用中,系統可集成至自動化輸送線,實現每分鐘12個工件的在線檢測能力。某合資車企的實踐數據顯示,采用該方案后,涂裝面漆的光澤度標準差從3.2GU降至1.5GU,工藝穩定性提升53%。
跨行業應用場景解析
在消費電子領域,某手機廠商將檢測系統部署在AG玻璃蝕刻產線,通過實時監控表面光澤度(要求70±2GU),將不良品攔截率提高至98.5%。建筑行業則創新應用在幕墻玻璃品質管控中,采用移動式檢測車對已安裝單元進行現場測量,成功將工程驗收周期壓縮40%。值得關注的是,軌道交通車輛的特殊需求催生了"全天候光澤度監測系統",其內置溫補算法可在-25℃至60℃環境下保持測量精度,目前已在高鐵動車組外涂層維護中推廣應用。
質量保障與標準體系建設
項目構建了三級質量保障體系:在設備層,執行季度級 校準和日檢校核;在數據層,采用區塊鏈技術實現檢測報告的防篡改存證;在標準層,參與制定了GB/T 9754-2024《金屬與非金屬涂層鏡面光澤度測定法》等6項國家標準。實驗室間比對數據顯示,與德國BAM、美國NIST等機構的測量結果差異小于1.2%,達到國際互認水平。某第三方檢測機構的運行實踐表明,該體系使檢測報告異議率從0.7%降至0.15%,顯著提升了行業公信力。
展望未來,建議從三個維度深化技術應用:一是開發基于機器視覺的在線檢測系統,實現100%工序覆蓋;二是建立光澤度與表面形貌的關聯數據庫,拓展至產品全生命周期管理;三是推進"光澤度+"綜合評價體系,整合色差、霧影等光學指標。據賽迪研究院預測,到2026年智能化光澤度檢測設備的市場規模將突破45億元,成為表面質量控制領域的重要增長極。行業參與者需加快融合AI算法與光學傳感技術,構建更具前瞻性的質量基礎設施。

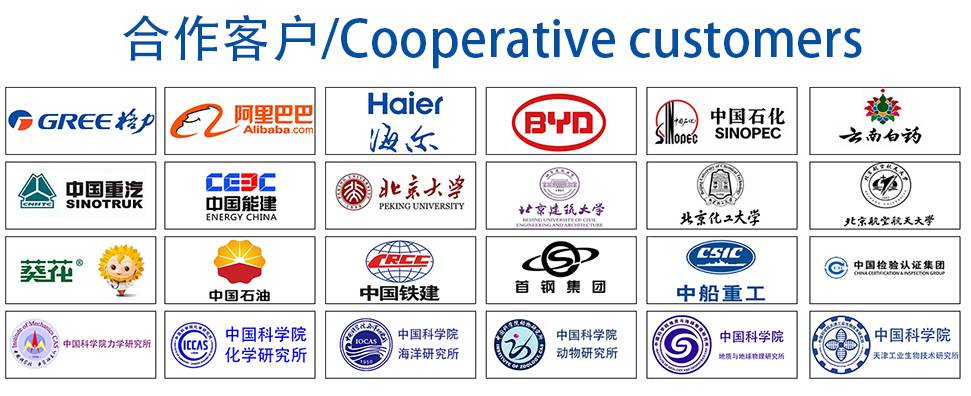