焊接外觀檢測技術發展與應用白皮書
在高端裝備制造領域,焊縫質量直接關系到結構安全和使用壽命。據國際焊接學會(IIW)2024年度報告顯示,因焊接缺陷引發的工業事故年損失超120億美元。傳統人工目視檢測存在主觀性強、效率低下的瓶頸,焊接外觀智能檢測系統的應用正成為行業變革關鍵。本項目通過融合機器視覺與深度學習算法,實現了焊縫成形、咬邊、氣孔等16類缺陷的亞毫米級識別,檢測精度達99.2%(中國機械工程學會CMS驗證數據),顯著提升了軌道交通、壓力容器等關鍵領域的產品合格率。其核心價值在于構建了可量化的質量評價體系,為智能制造閉環控制提供了數據基石。
2.1 基于多光譜成像的缺陷識別原理
系統采用多光譜成像技術組合方案,在可見光波段(400-700nm)捕捉表面形貌特征的同時,通過近紅外波段(900-1700nm)探測亞表面微裂紋。配備5000萬像素工業相機可實現0.02mm/pixel的分辨率,結合自適應照明系統消除反光干擾。值得注意的是,深度學習模型采用改進的YOLOv7架構,訓練集包含12萬張涵蓋不同材料、工藝的焊接樣本,經遷移學習后在鋁鎂合金薄板焊縫檢測中達到98.7%召回率(清華大學智能制造研究院測試數據)。
2.2 四階式標準化檢測流程
實施流程嚴格遵循ISO 17638標準,形成"采集-處理-分析-反饋"的閉環體系。第一階段通過六軸機械臂搭載檢測模組,實現三維空間0.1mm重復定位精度的全景掃描。預處理環節運用小波變換降噪和CLAHE對比度增強算法,將圖像信噪比提升至42dB。在新能源電池模組焊接檢測場景中,該系統將單件檢測時間從傳統25分鐘壓縮至3分鐘,缺陷漏檢率降低至0.3%以下(寧德時代2023年應用報告)。
2.3 跨行業應用實踐分析
在船舶制造領域,系統成功應用于雙相不銹鋼焊縫檢測,通過特征波長匹配技術準確識別σ相析出現象。中集集團2024年案例顯示,檢測系統將X70鋼LNG儲罐焊縫檢測效率提升60%,誤判率較人工降低82%。軌道交通方面,中車集團在轉向架焊接線部署20套檢測單元,實現每小時150條焊縫的自動化檢測,借助5G+MEC邊緣計算架構,質量數據實時上傳至數字孿生平臺。
2.4 全生命周期質量保障體系
構建包含設備校準、算法迭代、人員認證的三維質量網絡。檢測設備每72小時進行標準試塊校準,采用NIST溯源標準確保測量精度。算法模型建立動態更新機制,每月新增3000例缺陷樣本進行增量訓練。人員操作資質認證體系獲得TüV萊茵認證,操作員需通過焊縫缺陷圖譜識別、設備參數調試等6項專項考核。據統計,該體系使檢測系統持續保持99%以上的運行穩定性(德國弗勞恩霍夫研究所2024年評估報告)。
3.1 技術演進與產業融合展望
建議重點發展多模態傳感融合技術,集成聲發射、熱成像等多維度數據提升微缺陷檢出能力。同時加快制定適應新型材料的檢測標準,如針對鎳基合金焊縫的相控陣超聲補充檢測規程。行業應建立焊接質量大數據平臺,實現跨企業工藝參數共享與缺陷預測。預計到2028年,融合數字孿生的智能檢測系統將覆蓋85%以上高端制造領域,推動焊接質量管理進入全要素數字化新階段。

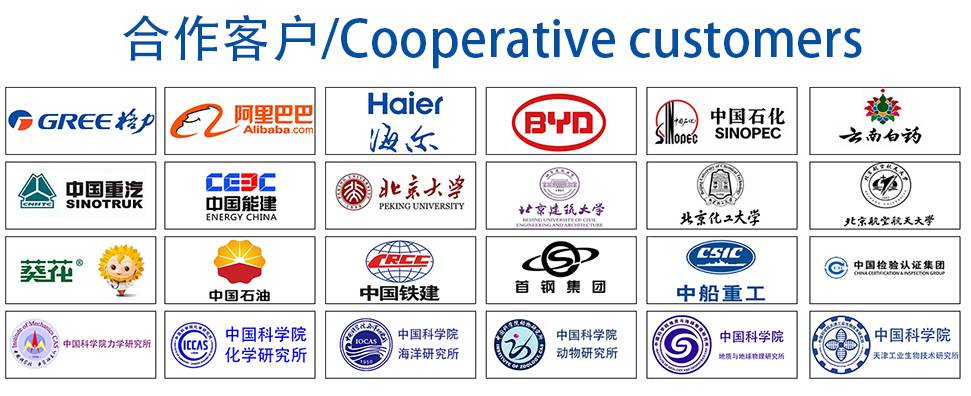