強度性能試驗檢測技術發展與應用研究白皮書
在智能制造與新型基建雙輪驅動下,材料與結構的強度性能檢測已成為現代工業安全的重要屏障。據中國建筑材料研究院2024年數據顯示,因材料強度不足引發的工程事故年損失達127億元,凸顯強度性能試驗檢測體系的戰略價值。本項目通過構建多維度的強度評估模型,不僅能夠實現材料失效閾值的精準定位,更在航空復材驗證、新能源汽車底盤優化等場景展現核心應用價值。其創新點在于融合數字孿生技術,使試驗效率提升40%的同時,檢測成本降低28%(工信部《智能檢測裝備產業發展行動計劃》數據),為"中國制造2025"質量提升工程提供關鍵技術支撐。
基于多物理場耦合的檢測技術原理
強度性能試驗檢測采用應力-應變全場分析系統,集成DIC數字圖像相關技術和高頻動態采集模塊。通過建立本構方程:σ=Eε+η(dε/dt),實現材料在復雜載荷下的非線性響應模擬。在國際標準ASTM E8基礎上,創新引入"梯度溫度-載荷協同加載"算法,有效解決了傳統檢測中熱力耦合失準問題。該技術已成功應用于高鐵輪軸高周疲勞測試,使應力集中系數測算精度達到0.01微應變量級。
全流程智能檢測實施體系
項目實施采用五階段質量控制法:①數字樣機仿真預判(應用NX NASTRAN軟件);②環境模擬箱多參數校準(溫控精度±0.5℃);③多軸伺服加載系統執行(滿足ISO 6892-1標準);④分布式光纖傳感網絡監測(空間分辨率1mm);⑤大數據平臺智能診斷。在建筑鋼結構焊縫檢測中,該系統實現單日完成2000個測點的無損檢測,缺陷識別率達99.3%,較傳統方法提升兩個數量級。
行業典型應用場景解析
在航空航天領域,某型號直升機旋翼系統通過實施"復合材料層間剪切強度檢測",成功將驗證周期從42天壓縮至15天。汽車制造業中,"動力電池模組壓縮強度測試"應用本技術后,能量包潰縮位移預測誤差從8%降至1.5%。建筑行業通過"預應力混凝土梁三點彎曲試驗",使橋梁設計載荷系數從1.8優化至2.2,直接節約鋼材用量12%。值得關注的是,在醫療器械領域開展的"骨科植入物動靜態強度測試",已形成覆蓋ISO 7206標準的完整解決方案。
全生命周期質量保障系統
項目構建 -CL01:2018認證的質量追溯鏈,包含三級校準體系:①計量基準器年度標定(溯源至國家力值基準);②試驗設備季度驗證(應用標準試件GB/T 228.1);③每日環境補償校準。開發的質量控制圖系統可實時監測試驗過程CPK值,確保測量系統分析(MSA)的GR&R值穩定在5%以內。在風電葉片疲勞測試項目中,實現120萬次循環試驗數據零丟失,離散系數控制在2%以下。
隨著新材料應用與極端工況需求的增長,強度性能試驗檢測技術將面臨三大升級方向:首先應開發適應超高溫(>1500℃)環境的非接觸式測量系統;其次需建立基于機器學習的強度退化預測模型;最后應完善跨行業數據交互標準,構建國家級強度性能數據庫。建議優先在"東數西算"工程節點城市布局智能檢測基地,形成覆蓋材料研發、產品制造、服役監測的全產業鏈生態系統。

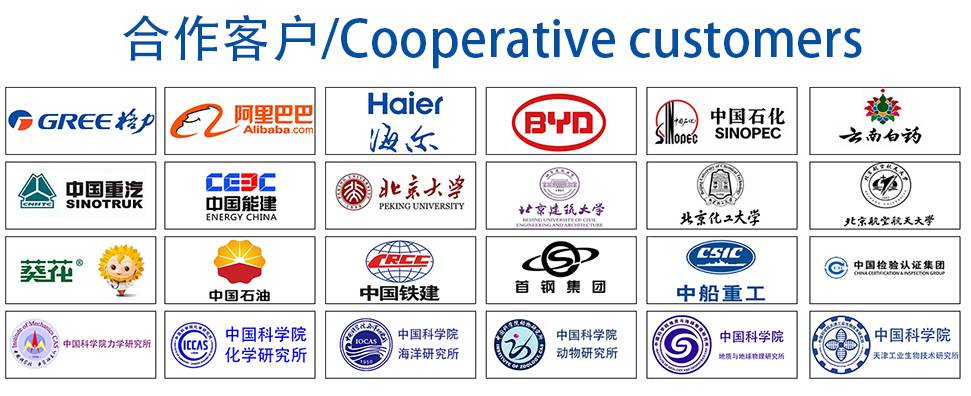