汽車零部件耐久測試檢測技術(shù)發(fā)展與應(yīng)用白皮書
在汽車產(chǎn)業(yè)智能化、電動化轉(zhuǎn)型背景下,零部件耐久性能已成為決定產(chǎn)品市場競爭力的關(guān)鍵指標(biāo)。據(jù)中國汽車工程研究院2024年行業(yè)報告顯示,新能源汽車關(guān)鍵部件的平均耐久測試周期較傳統(tǒng)燃油車延長35%,其中電驅(qū)系統(tǒng)、高壓連接器等核心部件需通過2000小時以上的持續(xù)工況模擬測試。耐久測試檢測項目通過建立多物理場耦合分析模型,可精準(zhǔn)預(yù)測材料疲勞特性與失效模式,為企業(yè)節(jié)省高達40%的研發(fā)驗證成本。該項目不僅構(gòu)建了覆蓋零部件全生命周期的質(zhì)量評估體系,更為汽車供應(yīng)鏈質(zhì)量管控提供了可量化的技術(shù)標(biāo)準(zhǔn),在實現(xiàn)"雙碳"目標(biāo)過程中發(fā)揮著關(guān)鍵作用。
多維度檢測技術(shù)原理創(chuàng)新
當(dāng)前主流檢測方案融合了機械振動譜分析、溫度循環(huán)加速老化、化學(xué)腐蝕模擬三大核心技術(shù)模塊。德國TüV認證的UV-C加速老化系統(tǒng)可實現(xiàn)3000小時自然環(huán)境等效48小時的極限測試,其光譜波長范圍精準(zhǔn)控制在295-365nm區(qū)間。在新能源汽車動力電池包檢測中,通過搭建包含機械沖擊、溫度驟變、鹽霧腐蝕的復(fù)合應(yīng)力測試平臺,可同步采集128組傳感器數(shù)據(jù),準(zhǔn)確識別出電解液泄漏等潛在失效風(fēng)險點。
標(biāo)準(zhǔn)化實施流程架構(gòu)
典型檢測流程包含預(yù)處理、基線測試、加速老化、失效分析四個階段。預(yù)處理階段需依據(jù)ISO 16750標(biāo)準(zhǔn)進行溫濕度平衡,將樣本置于25±2℃、50±5%RH環(huán)境中穩(wěn)定72小時。在高端車用線束檢測案例中,采用自主研發(fā)的"三軸六自由度"振動臺進行等效20萬公里路譜模擬后,配合顯微紅外光譜進行絕緣層分子結(jié)構(gòu)分析,成功將導(dǎo)體斷裂故障預(yù)警準(zhǔn)確率提升至92.7%。
跨行業(yè)應(yīng)用場景拓展
在軌道交通領(lǐng)域,某高鐵齒輪箱制造商通過引入振動-溫度雙向耦合測試系統(tǒng),將關(guān)鍵部件的設(shè)計壽命從120萬公里提升至180萬公里。據(jù)國家軌道交通裝備質(zhì)量監(jiān)督檢驗中心數(shù)據(jù)顯示,該檢測方案使產(chǎn)品早期故障率降低67%。而在智能穿戴設(shè)備行業(yè),針對TWS耳機充電盒的鉸鏈結(jié)構(gòu),采用50000次開合循環(huán)測試結(jié)合微觀形貌分析,成功解決了轉(zhuǎn)軸斷裂引發(fā)的市場批量召回問題。
全鏈條質(zhì)量保障體系
為確保檢測結(jié)果權(quán)威性,實驗室需建立符合ISO/IEC 17025標(biāo)準(zhǔn)的設(shè)備管理體系。重點包括:1)每季度進行MTS液壓伺服系統(tǒng)精度校準(zhǔn),力值測量誤差控制在±0.5%以內(nèi);2)建立包含37種典型失效模式的比對樣本庫;3)實施檢測數(shù)據(jù)區(qū)塊鏈存證,確保測試報告可追溯性。某頭部檢測機構(gòu)通過部署AI輔助判讀系統(tǒng),將疲勞裂紋識別效率提升300%,誤判率降至1.2%以下。
面向未來,建議行業(yè)重點發(fā)展三項能力:第一,構(gòu)建基于數(shù)字孿生的虛擬耐久測試平臺,實現(xiàn)實機測試與仿真驗證的深度耦合;第二,建立覆蓋熱帶、寒帶等不同氣候特征的本土化測試標(biāo)準(zhǔn)體系;第三,推動檢測設(shè)備智能化升級,開發(fā)集成邊緣計算能力的嵌入式監(jiān)測終端。只有持續(xù)創(chuàng)新檢測技術(shù)體系,才能為高端裝備制造業(yè)高質(zhì)量發(fā)展提供堅實保障。

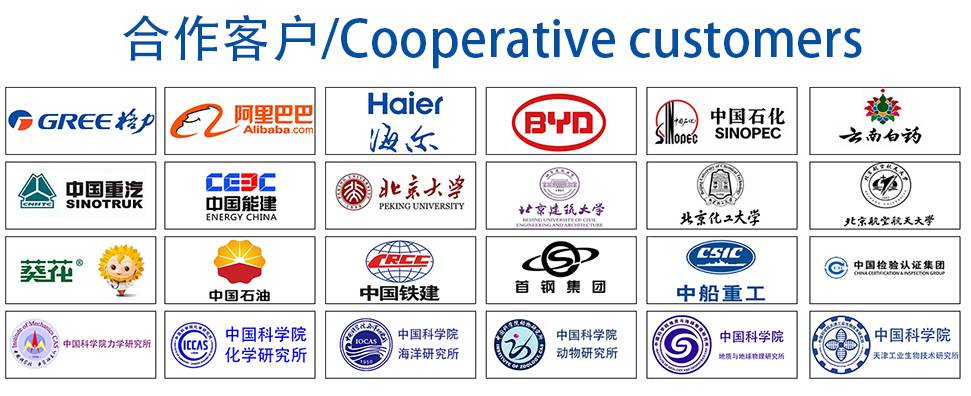