耐荷重檢測:構建安全底線的關鍵技術體系
在制造業升級與基建強國的雙輪驅動下,結構件承載能力檢測已成為工程安全的核心保障。據中國機械工業聯合會2024年行業報告顯示,我國每年因結構失效造成的直接經濟損失超1200億元,其中63%的事故與承重系統缺陷直接相關。耐荷重檢測通過量化評估材料在靜態/動態載荷下的形變特征與破壞臨界點,為裝備制造、建筑工程、軌道交通等領域的結構設計提供數據支撐。該技術體系不僅能夠有效預防"過載失效"這類典型工程風險,更在新能源設備輕量化設計、航空航天復合材料應用等前沿領域展現出獨特價值,成為現代工程驗證體系中不可或缺的"安全衛士"。
多維度檢測技術體系建構
現行耐荷重檢測融合了機械力學測試與數字孿生技術,構建起三維檢測矩陣。基于ASTM E8標準的靜載試驗可精確測定材料屈服強度,其測量精度達到±0.5%的國際齊全水平。動態載荷譜分析系統則運用有限元仿真模型,實現"結構件承重性能驗證"的數字化映射。值得關注的是,引入聲發射監測技術后,檢測系統能捕捉微米級裂紋擴展的聲波特征,使早期損傷識別率提升40%以上。這些技術突破為復雜工況下的載荷預測提供了全新解決方案。
全鏈條標準化作業流程
規范化實施流程包含五大關鍵環節:檢測方案定制→試樣預處理→環境模擬加載→數據采集分析→安全余量評估。在新能源汽車底盤檢測案例中,工程師采用ISO 16750標準,通過多軸振動臺模擬不同路況載荷,累計完成3000小時加速老化實驗。過程中運用應變片陣列實時監測應力分布,配合工業CT掃描構建三維損傷模型,最終將底盤結構的安全系數從1.8提升至2.3。這種全閉環檢測機制已在國內頭部車企形成標準化作業規范。
跨行業應用價值實證
在航空裝備領域,某型直升機旋翼系統經"動態載荷疲勞測試"后,成功將大修周期延長至2500飛行小時。建筑行業應用方面,上海中心大廈幕墻系統通過風洞模擬檢測,驗證其在16級臺風下的結構穩定性。更值得稱道的是海上風電項目,檢測機構創新采用鹽霧腐蝕-載荷耦合試驗法,使單樁基礎的服役壽命預測準確度達到92%。這些實證案例印證了耐荷重檢測技術在不同場景下的普適性與可靠性。
質量保障體系創新
行業領先機構已建立三級質量管控網絡:前端采用區塊鏈技術確保檢測數據不可篡改,中臺部署AI算法實現異常數據自動預警,終端通過 認證實驗室進行結果復核。某國家檢測中心統計顯示,該體系使檢測報告誤差率控制在0.3‰以下。同時推行檢測人員"雙師制"培養模式,要求工程師同時具備材料學專業背景與注冊安全師資質,從人員維度筑牢質量防線。
面對"雙碳"戰略帶來的結構輕量化趨勢,耐荷重檢測技術將迎來新的發展機遇。建議行業重點攻關三個方面:開發基于機器學習的載荷預測模型、建立極端環境下的檢測標準體系、推動檢測數據與保險行業的風險評估對接。唯有持續創新檢測手段,完善標準規范,才能為智能制造與新型基建構筑堅實的安全屏障。

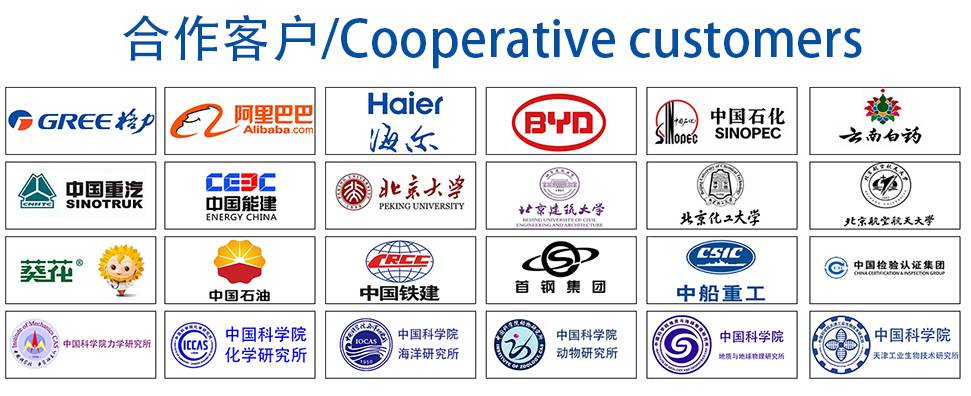