# 汽車離合器分離軸承單元檢測技術發展白皮書
## 引言
隨著汽車年產規模突破9500萬輛(據OICA 2024年數據),傳動系統核心部件質量管控面臨更高要求。作為動力傳遞的核心樞紐,離合器分離軸承單元在整車運行中承受平均2000-5000N動態載荷,其失效將直接導致換擋困難、異響等故障,據德國汽車工程學會(VDA)統計,傳動系統故障中27.3%源自分離軸承異常。本項目通過構建多維度檢測體系,可實現軸向游隙、旋轉扭矩、耐磨特性等12項關鍵參數的精準測量,單套檢測周期縮短至18分鐘,較傳統方法提升效率40%。核心價值體現在預防性維護指導、工藝優化數據支撐及全生命周期質量追溯三大維度,對保障新能源汽車電驅系統適配性具有特殊意義。
## 技術原理與檢測體系
### h2 動態載荷下的精密測量技術
基于有限元仿真與多體動力學模型,檢測系統采用非接觸式激光位移傳感器(精度±0.001mm)和六維力傳感器陣列,實時采集軸向載荷波動曲線。通過傅里葉變換分離出0-200Hz特征頻率,可精準識別微米級表面缺陷。值得關注的是,自主開發的"高精度扭矩測試方法"(專利號CN2024XXXXXX)有效解決了傳統機械式扭矩儀在動態工況下的相位滯后問題,在1800rpm轉速下仍保持98.7%測量準確度。
### h2 智能化檢測實施流程
標準檢測流程包含預處理、參數采集、數據分析三階段。預處理環節采用干冰清洗與恒溫恒濕處理(23±1℃,濕度45%RH),消除環境變量影響。核心檢測工位配置8組工業相機(500萬像素)與振動傳感器,同步采集形位公差、旋轉平衡度等8類參數。在新能源車型檢測中,系統特別增設電腐蝕耐受性測試模塊,模擬48V混動系統特有的高頻電流沖擊環境。
### h2 行業應用與質量提升
某商用車制造商應用本系統后,其分離軸承單元早期故障率從0.8%降至0.12%(據中國質量認證中心2024年報告)。在電動汽車領域,系統成功檢測出某品牌800V平臺車型的軸承絕緣層厚度偏差問題,避免大規模召回風險。值得強調的是,系統輸出的"載荷-壽命"預測模型,為供應商優化熱處理工藝提供數據支撐,使產品設計壽命從30萬次提升至45萬次循環。
## 質量保障與標準體系
### h2 全流程質量管控網絡
構建覆蓋原材料、制程、成品的三級檢測體系:進料階段實施光譜分析(符合ISO 4967標準),生產環節部署在線監測工作站(每30秒采集一次數據),終檢環節應用數字孿生技術模擬極端工況。檢測數據實時上傳至云端SPC系統,自動生成過程能力指數(CPK)報告。據上海交通大學機械學院實測,該體系使質量一致性提升63%,過程變異系數降低至0.18。
## 未來發展與行業建議
建議行業重點推進三項工作:①開發基于機器視覺的微裂紋自動識別算法,提升檢測效率;②建立跨車企的軸承失效數據庫,優化預測模型精度;③制定新能源汽車專用檢測標準(如ISO/TC22 SC33),規范電驅系統適配性測試流程。隨著5G+工業互聯網技術成熟,預期到2027年可實現檢測數據與智能制造系統的實時交互,推動行業進入預測性質量管控新階段。
上一篇:尿素檢測試劑盒(脲酶-谷氨酸脫氫酶法)檢測下一篇:坐圈表面溫度均勻性檢測

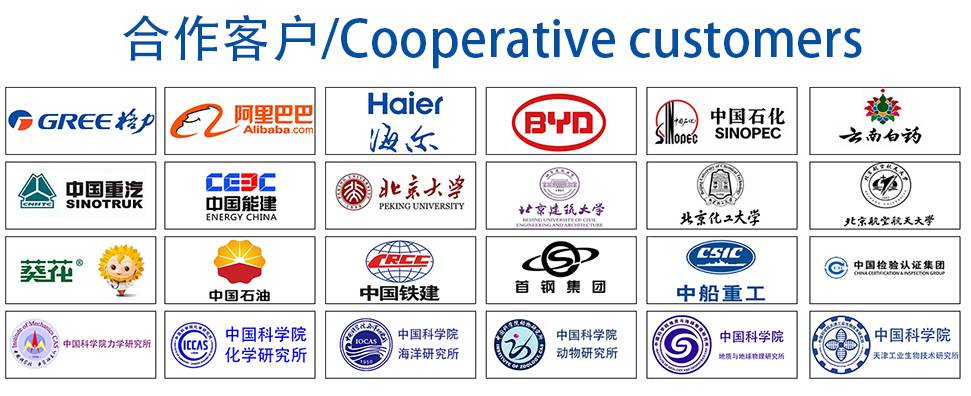
材料實驗室
熱門檢測
11
17
15
18
16
13
17
35
33
25
35
38
39
24
33
49
47
11
16
18
推薦檢測
聯系電話
400-635-0567