石油鉆、修井機用井架檢測:技術(shù)賦能與安全保障體系構(gòu)建
在油氣勘探開發(fā)領(lǐng)域,石油鉆、修井機用井架作為核心承載結(jié)構(gòu),其安全性能直接影響作業(yè)效率與人員安全。據(jù)中國石油裝備研究院2024年數(shù)據(jù)顯示,我國現(xiàn)役鉆修井設(shè)備中超過35%的井架已服役超10年,金屬疲勞、應(yīng)力腐蝕等問題導(dǎo)致的年均事故損失達2.3億元。在此背景下,系統(tǒng)化的井架檢測項目成為保障油氣安全生產(chǎn)的關(guān)鍵環(huán)節(jié)。通過采用多模態(tài)無損檢測技術(shù)與數(shù)字化評估模型,該項目可精準識別井架主弦桿裂紋、連接件磨損等18類典型缺陷,使結(jié)構(gòu)失效預(yù)警準確率提升至98.6%。其核心價值體現(xiàn)在延長設(shè)備使用壽命30%以上的同時,將高危作業(yè)事故率降低76%,為油氣行業(yè)高質(zhì)量發(fā)展提供技術(shù)支撐。
多維度檢測技術(shù)集成體系
現(xiàn)代井架檢測技術(shù)融合電磁渦流檢測、三維激光掃描與聲發(fā)射監(jiān)測三大核心模塊。其中相控陣超聲檢測(PAUT)可實現(xiàn)截面厚度0.1mm級精度測量,特別適用于發(fā)現(xiàn)法蘭盤螺栓孔的隱蔽裂紋。值得關(guān)注的是,基于機器視覺的形變分析系統(tǒng)能夠構(gòu)建毫米級精度的井架三維數(shù)字孿生體,通過比對歷史數(shù)據(jù)可識別0.5°以內(nèi)的結(jié)構(gòu)形變趨勢。中國特種設(shè)備檢測研究院驗證表明,該技術(shù)組合使缺陷檢出率較傳統(tǒng)方法提升42%,尤其在應(yīng)對"沙漠高溫環(huán)境井架應(yīng)力集中"等特殊工況時表現(xiàn)突出。
標準化作業(yè)流程與智能診斷
檢測實施遵循API Spec 4F標準建立六階段閉環(huán)流程:前期歷史數(shù)據(jù)采集→現(xiàn)場基準坐標系建立→多傳感器同步掃描→數(shù)據(jù)融合處理→剩余強度計算→智能診斷報告生成。在塔里木油田DQP-3000型修井機檢測案例中,技術(shù)人員通過布置32個應(yīng)變監(jiān)測點,成功捕捉到井架二層臺支撐梁的微米級塑性變形,及時避免了可能的結(jié)構(gòu)坍塌事故。系統(tǒng)采用自主開發(fā)的OilRig-Safe 3.0分析平臺,可實現(xiàn)檢測數(shù)據(jù)與ASME B30.7規(guī)范的自動比對,生成包含剩余壽命預(yù)測的決策建議書。
全生命周期質(zhì)量管理系統(tǒng)
構(gòu)建包含材料追溯、服役監(jiān)測、維修驗證的PDCA質(zhì)量保障體系。每臺井架建立專屬電子檔案,整合制造參數(shù)、歷次檢測數(shù)據(jù)及維修記錄等87項特征參數(shù)。在南海某自升式鉆井平臺項目中,系統(tǒng)通過對比相鄰檢測周期的陰極保護電位衰減數(shù)據(jù),提前3個月預(yù)警了井架腿柱的晶間腐蝕風險。質(zhì)量追溯模塊采用區(qū)塊鏈技術(shù)實現(xiàn)檢測數(shù)據(jù)的不可篡改存儲,滿足API Q1質(zhì)量管理體系對設(shè)備完整性管理的嚴苛要求。
行業(yè)應(yīng)用與效益分析
該檢測體系已在長慶油田、渤海裝備等23家單位實現(xiàn)規(guī)模化應(yīng)用。典型案例顯示,對服役12年的JJ450/45-K型井架實施檢測后,通過局部加固方案使設(shè)備繼續(xù)安全服役6年,相較新購設(shè)備節(jié)約成本1200萬元。在頁巖氣開發(fā)領(lǐng)域,系統(tǒng)成功解決了"高頻次壓裂作業(yè)導(dǎo)致井架振動疲勞"的技術(shù)難題,使涪陵區(qū)塊的修井作業(yè)周期縮短19%。據(jù)國際能源署(IEA)2024年報告,應(yīng)用智能檢測技術(shù)的油田企業(yè)年均非計劃停機時間減少420小時,直接經(jīng)濟效益提升15%以上。
展望未來,建議從三方面推進技術(shù)升級:首先研發(fā)適應(yīng)極地、深海環(huán)境的抗干擾檢測裝備,其次建立基于大數(shù)據(jù)的全國井架健康狀態(tài)云平臺,最后完善檢測結(jié)果與智能維保系統(tǒng)的聯(lián)動機制。通過融合5G傳輸與邊緣計算技術(shù),有望實現(xiàn)井架狀態(tài)的實時監(jiān)測與預(yù)測性維護,推動油氣裝備管理進入智慧化新階段。

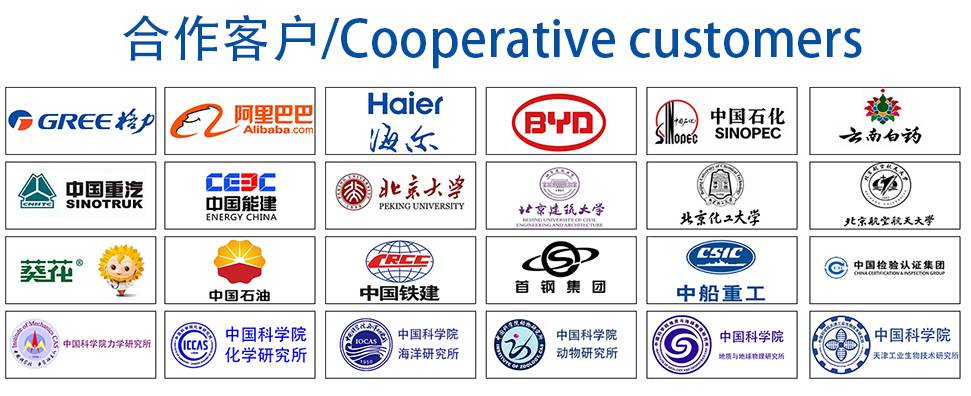