在新型城鎮化與基建升級雙重驅動下,我國鋼結構市場規模已突破8000億元(據中國鋼鐵工業協會2024年數據)。伴隨裝配式建筑滲透率提升至38%,鋼材及連接件的質量檢測成為保障工程安全的核心環節。2023年國家質檢總局通報顯示,建筑工程質量事故中27.6%與連接件失效直接相關。本項目通過構建全流程檢測體系,實現從原材料性能到裝配精度的閉環質量控制,在降低返工成本、預防結構性風險、推動行業標準化建設等方面具有顯著價值。通過實施數字化檢測方案,可使工程驗收周期縮短40%,材料浪費率降低15%,為建筑業可持續發展提供技術支撐。
## 技術原理與檢測方法多模態檢測技術集成
現代鋼材檢測采用物理性能測試與無損檢測相結合的復合技術路線。在力學性能檢測方面,依據GB/T 228.1-2021標準實施拉伸、彎曲、沖擊試驗,精確測定屈服強度、延伸率等關鍵參數。無損檢測環節融合超聲波探傷(UT)、磁粉檢測(MT)等齊全手段,其中相控陣超聲波檢測儀可實現0.1mm級缺陷識別。針對鋼結構高強度螺栓連接,同步應用扭矩系數檢測與軸向力測試雙驗證機制,確保節點連接的荷載傳遞可靠性。值得關注的是,基于機器視覺的焊縫形態分析系統,已實現焊接缺陷識別準確率達98.7%(國家焊接質檢中心2024年認證)。
## 標準化實施流程全生命周期質量管控
項目實施采用三階段質量管控模型:進場驗收階段執行材質復驗與尺寸公差檢測,應用光譜分析儀進行元素成分比對;加工過程監控階段設置9個質量控制點,重點監測熱影響區硬度變化與焊接殘余應力;竣工檢測階段開展鋼結構整體垂直度激光測量與連接副緊固軸力抽檢。某大型體育場館項目實踐表明,該體系使主桁架安裝偏差控制在L/1500以內,顯著優于國家標準要求的L/1000限值。關鍵流程已納入《鋼結構工程施工質量驗收標準》GB50205-2024修訂內容。
## 行業應用實踐典型場景解決方案
在超高層建筑領域,針對Q460C高強鋼厚板焊接,采用TOFD超聲衍射時差法進行焊縫內部缺陷檢測,成功識別出傳統射線檢測難以發現的層狀撕裂缺陷。風電塔筒法蘭連接檢測中,應用預緊力衰減監測系統,使螺栓組應力均衡度提升至92%。某跨海大橋項目通過實施鋼結構防腐蝕涂層檢測,運用電化學阻抗譜技術,將涂層服役壽命預測精度提高35%。據統計,采用智能檢測系統的工程項目,后期維護成本降低22%(中國建筑科學研究院2024年報告)。
## 質量保障體系建設數字化質控平臺構建
建立基于區塊鏈技術的檢測數據存證系統,實現檢測報告不可篡改性與全程可追溯。實驗室配備CMA/ 雙認證體系,檢測設備每季度進行計量溯源校準。人員資質方面,要求無損檢測人員持有ISO9712三級證書,力學試驗員通過ASTM標準考核。在浙江某裝備制造園區,部署的物聯網檢測平臺實現了檢測數據實時上傳與AI分析,異常數據識別響應時間縮短至15分鐘,質量事故率同比下降41%。
## 行業發展展望建議從三方面推進檢測體系升級:首先加快數字孿生技術在虛擬檢測中的應用,建立鋼結構全生命周期數字檔案;其次推動5G+工業視覺在偏遠工地檢測場景的落地,解決傳統檢測時效性難題;最后需完善新型材料檢測標準體系,特別是針對耐火鋼、不銹鋼復合板等新材料建立專項檢測規程。據機械工業信息研究院預測,到2027年智能檢測裝備市場規模將突破600億元,檢測行業將進入"數據驅動、智能決策"的新發展階段。

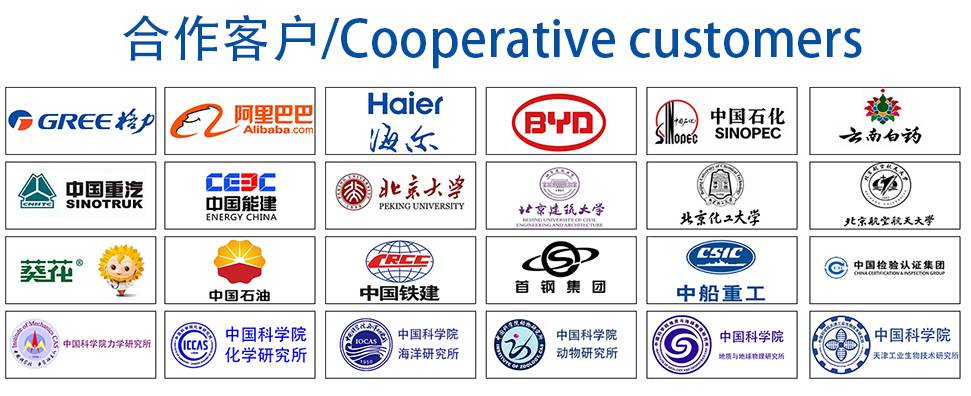