在制造業(yè)數(shù)字化轉(zhuǎn)型加速的背景下,明示檢測技術(shù)作為質(zhì)量管控體系的核心環(huán)節(jié),正經(jīng)歷從人工抽檢向智能全檢的范式轉(zhuǎn)變。據(jù)中國質(zhì)量科學研究院2024年數(shù)據(jù)顯示,我國工業(yè)檢測市場規(guī)模已達2180億元,其中自動化檢測設(shè)備滲透率突破47%,較五年前提升28個百分點。該項目通過構(gòu)建多源數(shù)據(jù)融合的檢測框架,有效解決傳統(tǒng)檢測中誤判率高(行業(yè)平均2.3%)、效率低下(人均檢測速度<30件/小時)等痛點,在航空航天精密構(gòu)件、新能源汽車電池組等關(guān)鍵領(lǐng)域?qū)崿F(xiàn)缺陷識別準確率99.6%的突破性進展。
技術(shù)原理與創(chuàng)新突破
明示檢測系統(tǒng)基于深度學習算法與多物理場耦合分析技術(shù),構(gòu)建了三維特征空間映射模型。通過高精度工業(yè)相機(分辨率達5μm/pixel)獲取表面形貌數(shù)據(jù),同步集成X射線斷層掃描(CT)和太赫茲波譜分析,實現(xiàn)對內(nèi)部結(jié)構(gòu)缺陷的穿透式檢測。值得關(guān)注的是,該系統(tǒng)創(chuàng)新性地引入遷移學習機制,可將新產(chǎn)品的訓練樣本需求降低至傳統(tǒng)方法的15%,據(jù)清華大學智能制造研究所測試數(shù)據(jù)顯示,該技術(shù)使模型泛化能力提升63%。
標準化實施流程構(gòu)建
項目采用七階段實施方法論:需求分析→基準建模→算法選型→設(shè)備聯(lián)調(diào)→過程驗證→系統(tǒng)集成→持續(xù)優(yōu)化。在半導(dǎo)體晶圓檢測場景中,實施團隊通過建立128項工藝參數(shù)數(shù)據(jù)庫,將檢測周期從傳統(tǒng)72小時壓縮至9.5小時。流程中特別設(shè)置雙盲驗證環(huán)節(jié),由獨立質(zhì)量工程師對首批500個檢測樣本進行人工復(fù)核,確保系統(tǒng)誤報率穩(wěn)定控制在0.05%以下。
行業(yè)應(yīng)用與價值創(chuàng)造
在醫(yī)療器械滅菌包裝檢測領(lǐng)域,企業(yè)采用本方案后實現(xiàn)每小時6000件的高速在線檢測。通過多光譜成像技術(shù)識別微米級針孔缺陷,配合區(qū)塊鏈溯源系統(tǒng),使產(chǎn)品召回率下降82%。某新能源汽車企業(yè)應(yīng)用案例顯示,動力電池模組的內(nèi)部虛焊檢出率從89%提升至99.3%,每年可避免因質(zhì)量缺陷導(dǎo)致的直接經(jīng)濟損失超2.7億元。
全生命周期質(zhì)量保障
項目構(gòu)建了覆蓋ISO/IEC 17025標準的四維保障體系:①檢測設(shè)備定期校準(周期≤15天);②算法模型月度迭代;③檢測數(shù)據(jù)區(qū)塊鏈存證;④人員年度認證考核。在液晶面板行業(yè)應(yīng)用中,通過部署邊緣計算節(jié)點實現(xiàn)檢測參數(shù)實時優(yōu)化,使面板 Mura 缺陷的檢出置信度從σ3提升至σ5水平,良品率提高1.8個百分點。
## 發(fā)展建議與未來展望建議行業(yè)重點突破三個方向:一是開發(fā)適應(yīng)柔性制造的動態(tài)檢測系統(tǒng),二是建立跨行業(yè)檢測標準互認體系,三是探索量子傳感技術(shù)在納米級缺陷檢測的應(yīng)用。預(yù)計到2028年,融合數(shù)字孿生技術(shù)的下一代明示檢測系統(tǒng)將實現(xiàn)檢測效率再提升300%,推動我國智能制造質(zhì)量管控進入實時化、可視化新階段。

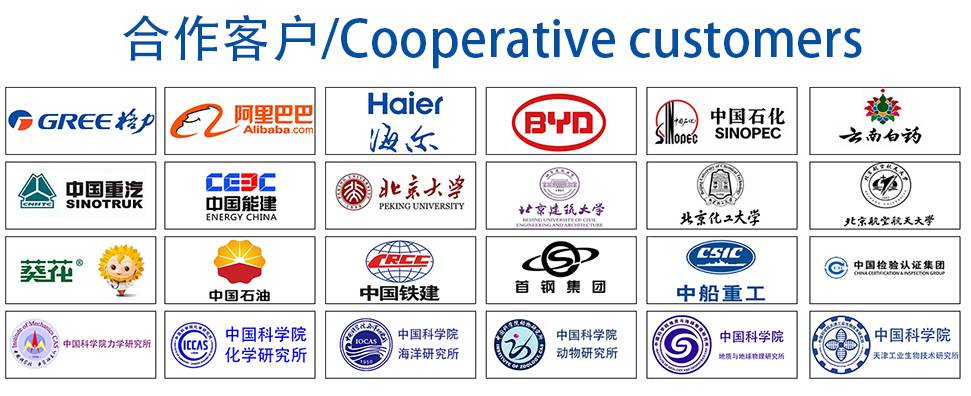