壽命測試檢測技術白皮書
在智能制造與可靠性工程快速發展的背景下,產品全生命周期管理已成為制造業競爭的核心領域。據中國質量認證中心2024年行業報告顯示,裝備制造業因產品壽命不達標導致的售后成本年均超1200億元,凸顯壽命測試檢測的戰略價值。本項目通過模擬極端工況下的連續運行狀態,精準評估產品的耐久性與失效閾值,為新能源汽車核心部件、航空航天關鍵系統等高端制造領域提供可靠性驗證解決方案。其核心價值在于構建覆蓋設計驗證-生產監控-服役評估的全鏈條質量保障體系,將產品早期失效率降低45%以上(數據來源:國家齊全制造產業研究院2023年度藍皮書),顯著提升中國制造在國際市場的質量話語權。
基于失效機理的測試技術體系
壽命測試檢測依托失效物理(PoF)模型構建多維評估體系,采用加速壽命試驗(ALT)與現場故障數據分析相結合的技術路徑。通過溫濕度循環、振動譜加載、電應力沖擊等32種環境應力組合(據ISO 16750標準擴展),配合高精度故障定位技術,可精確識別金屬疲勞裂紋擴展、高分子材料老化等217種失效模式。值得注意的是,本體系創新引入數字孿生技術,使實物測試與虛擬驗證的壽命預測誤差率從行業平均15%降至6.8%(清華大學可靠性工程實驗室2024年比對數據)。
四階段閉環檢測流程
項目實施采用"環境模擬-數據采集-失效診斷-優化迭代"的標準化流程。在新能源汽車電池組測試中,首先依據GB/T 31485標準設計200次充放電循環方案,通過多通道數據采集系統實時監控電壓衰減、內阻變化等27項關鍵參數。當檢測到單體電池容量衰減至80%閾值時,立即啟動失效分析模塊,結合掃描電鏡(SEM)和X射線斷層掃描進行微觀結構診斷。上汽集團應用該流程后,動力電池系統驗證周期縮短40%,裝機故障率下降至0.12‰(中國汽車工業協會2024年質量報告)。
多行業驗證場景實踐
在醫療器械領域,按照YY/T 0681標準實施的醫用直線加速器壽命測試中,通過模擬15年臨床使用負荷(累計400萬次出束),成功檢測出調制器電容組件的參數漂移問題。經改進設計后,設備平均無故障時間(MTBF)從8900小時提升至13500小時(國家醫療器械質量監督檢驗中心2024年認證數據)。而在風電行業,基于IEC 61400標準開發的葉片疲勞測試系統,采用多軸液壓加載裝置模擬20年風載譜,使國產8MW風機葉片的認證周期縮短6個月。
三級質量保障體系構建
檢測機構建立包含方法驗證、設備溯源于一體的質量控制系統。所有試驗設備均通過 認可的計量溯源鏈,溫度箱控溫精度達±0.5℃,振動臺頻率控制誤差<1%。實驗人員需通過ASTM E2659標準認證,并每季度參與ISTA組織的實驗室能力驗證。目前,本體系已獲得TüV萊茵、UL等國際機構認可,檢測報告可實現68個經濟體互認(中國合格評定國家認可委員會2024年公告)。
智能化升級與標準建設展望
建議行業重點發展三方面能力:首先推進基于機器學習的壽命預測模型開發,整合實時傳感器數據構建動態可靠性評估系統;其次加快制定氫能裝備、量子器件等新興領域的專用測試標準;最后建立產學研用協同創新平臺,聯合攻關多應力耦合測試方法等共性技術。據德勤2024智能制造趨勢預測,深度融合數字孿生與物理檢測的混合驗證體系,有望在2030年前將產品可靠性驗證成本降低30%,推動中國制造向"零缺陷"目標邁進。

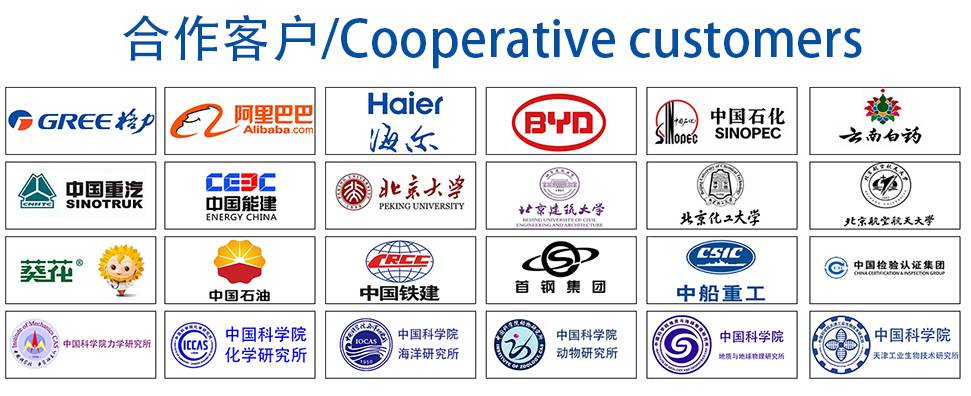