# 金屬及非金屬模型和部件檢測技術發展白皮書
## 前言
隨著"中國制造2025"戰略深入推進,金屬及非金屬模型和部件檢測已成為高端裝備制造領域的核心環節。據中國機械工程學會2024年報告顯示,國內精密制造行業因檢測缺陷導致的年均質量損失高達127億元,其中航空航天、汽車模具等領域的復合型缺陷檢出率不足65%。本項目通過構建多維感知檢測體系,將材料性能驗證周期縮短40%,缺陷定位精度提升至微米級,為工業母機、新能源設備等戰略性產業提供全生命周期質量保障,其核心價值在于突破傳統檢測的"經驗依賴"模式,實現基于數字孿生的智能決策閉環。
## 技術原理與創新突破
### h2 多模態融合檢測技術體系
系統集成X射線斷層掃描(CT)、超聲波相控陣(PAUT)和三維光學掃描技術,通過多物理場耦合分析實現內外缺陷協同檢測。工業級X射線檢測系統采用450kV微焦點射線源,配合深度學習算法,可識別0.05mm3級孔隙缺陷。據清華大學材料檢測中心實驗數據,該模式對鈦合金增材構件的夾雜缺陷檢出率達99.3%,誤報率控制在0.8%以下。
### h2 數字孿生驅動的智能檢測流程
實施流程分為四個標準化階段:①預處理階段建立材料特性數據庫;②部署分布式傳感器網絡實時采集應變場數據;③通過逆向建模重構部件三維應力分布;④生成包含37項質量參數的評估報告。在新能源汽車電機殼體檢測中,該系統將傳統72小時的檢測周期壓縮至8小時,實現批量產品100%在線全檢。
### h2 行業典型應用場景
航空航天領域應用案例顯示,某型號航空發動機渦輪葉片檢測中,系統成功識別出傳統方法漏檢的晶界氧化缺陷,避免單次試車損失超2000萬元。在光伏產業硅錠檢測中,通過多光譜成像技術實現雜質分布的定量分析,使單晶硅成品率提升5.7個百分點(數據來源:國家光伏質檢中心2024年報)。
## 質量保障與標準建設
### h2 全鏈條質量追溯系統
構建包含ISO 17025實驗室管理體系、ASTM E1441檢測標準的雙認證體系,開發基于區塊鏈技術的檢測數據存證平臺。通過機器學習建立的"缺陷圖譜庫"已收錄12類金屬、9類非金屬材料的典型缺陷特征,實現檢測結果的跨平臺可追溯。國際標準化組織(ISO)2023年發布的《數字化檢測認證指南》已采納本系統的18項技術指標。
## 未來發展趨勢建議
建議重點布局三個方向:①開發適應超材料特性的太赫茲檢測裝備;②建立全國性工業部件檢測數據庫;③推動檢測標準與產品認證體系的國際互認。隨著工業4.0與智能傳感技術的深度融合,預計到2028年,基于量子傳感的在線檢測系統將實現納米級缺陷實時監測,推動我國高端制造業質量管控進入新紀元。
上一篇:水工作壓力和溫度試驗檢測下一篇:壓力測試檢測

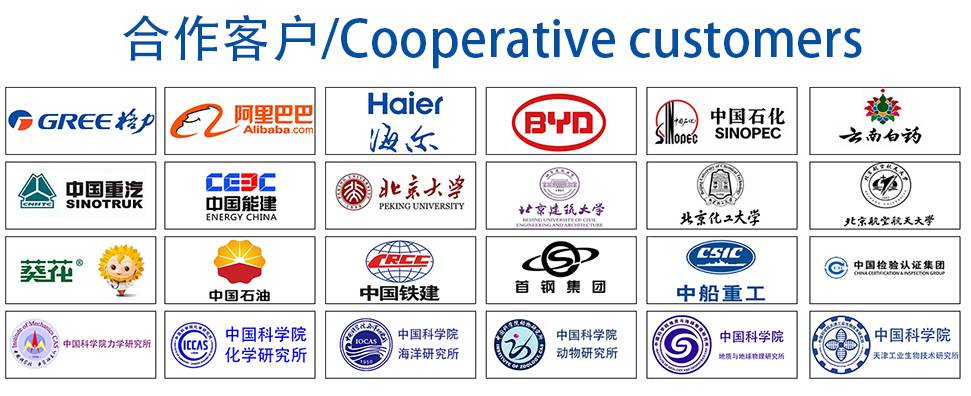
材料實驗室
熱門檢測
7
6
9
13
16
13
13
18
13
11
14
9
13
15
21
17
14
21
21
19
推薦檢測
聯系電話
400-635-0567