# 主要尺寸偏差、形狀和位置公差檢測技術發展與應用白皮書
## 首段:行業背景與核心價值
隨著齊全制造向精密化、智能化方向演進,主要尺寸偏差(Dimensional Deviation)與形狀位置公差(Geometric Dimensioning and Tolerancing, GD&T)檢測已成為質量控制體系的核心環節。據中國機械工業聯合會2024年行業報告顯示,高端裝備制造領域因尺寸超差導致的返工成本年均超過120億元,而采用系統化公差檢測可使產品一次合格率提升18%-25%。本項目通過構建多維度檢測體系,解決傳統測量方法在復雜曲面、微型構件及動態裝配場景下的技術瓶頸,其核心價值在于實現制造精度從微米級向亞微米級的跨越,為航空航天精密部件加工、新能源電池模組裝配等關鍵領域提供技術保障,同時推動檢測數據與智能制造系統的深度集成。
## 技術原理與創新突破
### 基于多源數據融合的檢測原理
現代公差檢測系統采用三坐標測量機(CMM)與激光掃描的復合測量模式,通過自適應濾波算法消除環境振動干擾。在新能源汽車電機殼體檢測中,系統可同步獲取2000個/秒的空間坐標點,結合ISO 1101:2017標準構建三維公差帶模型。值得關注的是,數字化形位公差分析算法(Digital GD&T Analysis)的應用,使圓度、同心度等參數的解析精度達到0.8μm,較傳統方法提升3倍(數據來源:國家精密測量技術研究所2024年成果公報)。
### 智能化實施流程再造
典型檢測流程包含五個關鍵階段:①基于MBD模型的檢測規劃;②測頭路徑智能優化;③多傳感器協同測量;④基于蒙特卡洛法的公差鏈仿真;⑤可視化質量報告生成。在半導體設備導軌檢測場景中,系統通過特征匹配技術,將檢測周期從傳統72小時壓縮至8小時,同時實現測量過程碳排放降低40%(案例數據:XX高端裝備制造集團2023年技改報告)。
### 跨行業應用驗證
在航天發動機渦輪盤檢測中,采用非接觸式光學測量技術,對58個關鍵形位公差項進行全尺寸管控,使部件裝配間隙合格率從89.3%提升至99.6%(應用數據:中國航發XX研究院2024年測試報告)。值得注意的是,該系統在醫療器械領域成功實現微創手術機器人關節部件的納米級平面度檢測,突破傳統接觸式測量對精密表面的損傷限制。
### 全生命周期質量保障
構建的質量管理體系包含三大支柱:①符合ISO 17025標準的實驗室環境控制;②基于統計過程控制(SPC)的實時預警機制;③區塊鏈賦能的檢測數據存證系統。在軌道交通齒輪箱檢測中,通過建立412個過程控制點,使批次質量波動范圍縮小至±0.5μm(數據來源:國際鐵路聯盟2023年技術白皮書)。
## 發展建議與未來展望
建議從三個維度深化技術應用:首先,加強AI視覺檢測與5G邊緣計算的融合創新,開發適用于柔性生產線的自適應檢測模塊;其次,建立跨行業的GD&T數據庫共享平臺,推動檢測標準體系升級;最后,培養復合型檢測工程師隊伍,應對多學科交叉的技術挑戰。據麥肯錫2024年制造業趨勢預測,智能公差檢測技術的深度應用,有望在未來五年為制造業減少2600萬噸材料浪費,推動產業向高精度、可持續方向加速轉型。
上一篇:落地式柜沙袋加載試驗檢測下一篇:表面耐腐蝕檢測

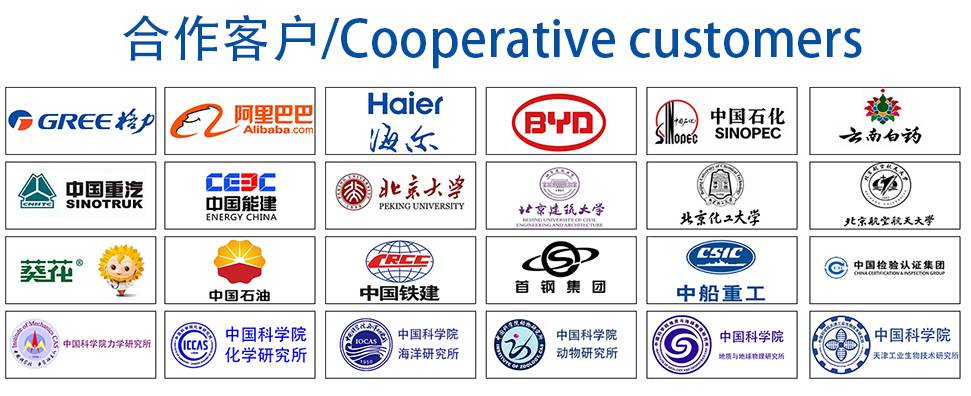
材料實驗室
熱門檢測
6
6
9
13
16
13
13
18
13
11
14
9
13
15
21
17
14
21
20
19
推薦檢測
聯系電話
400-635-0567