金屬配件表面處理測定檢測技術白皮書
在高端裝備制造與精密加工領域,金屬配件表面處理質量直接影響產品耐腐蝕性、機械強度及使用壽命。據中國表面工程協會2024年行業報告顯示,我國每年因表面處理缺陷導致的金屬零部件失效案例超過12萬起,直接經濟損失達38億元。在此背景下,金屬配件表面處理測定檢測項目作為質量管控的核心環節,通過精準量化鍍層厚度、附著力、孔隙率等關鍵指標,為航空航天、汽車制造、電子設備等行業提供了全生命周期質量保障。其核心價值體現在突破傳統目視檢測的主觀局限,建立基于數據驅動的工藝優化體系,使熱處理滲氮層公差控制精度提升至±0.5μm,鹽霧試驗周期縮短40%,顯著增強了國產金屬配件在國際供應鏈中的競爭力。
多維度檢測技術原理體系
現代表面處理檢測采用光譜分析、電化學測試與顯微觀測的復合技術路徑。X射線熒光光譜(XRF)技術可實現鍍層厚度的無損檢測,檢測精度達0.01μm級,特別適用于汽車發動機活塞環的硬鉻鍍層測定。掃描電子顯微鏡(SEM)配合能譜分析(EDS)可解析微米級孔隙分布,成功應用于航空航天緊固件的陽極氧化膜檢測。值得關注的是,金屬表面鈍化膜厚度檢測創新性地結合了交流阻抗譜和恒電位階躍法,使316L不銹鋼鈍化膜厚度檢測誤差控制在±2nm范圍內,為醫療器械表面處理提供了精準評價手段。
標準化檢測實施流程
檢測流程嚴格遵循ISO 2178(磁性基體非磁性鍍層)和ASTM B568(X射線測厚)標準體系。以某新能源車企電驅系統殼體檢測為例,實施流程包括:預處理階段采用氬離子拋光消除表面污染→三維形貌掃描建立基準模型→選區激光剝蝕(LA-ICP-MS)分析鍍層元素梯度分布→循環腐蝕試驗模擬10年服役環境。通過電鍍層孔隙率無損檢測技術的應用,該企業將鍍鎳層孔隙密度從12個/cm2降至3個/cm2,產品保修期延長至8年/20萬公里。
跨行業應用實踐驗證
在軌道交通領域,某高鐵制動盤制造商采用渦流檢測與熱震試驗結合方案,實現表面滲鋁層厚度(120±5μm)的在線檢測,使產品耐高溫性能提升至650℃工況下的2000次熱循環。電子連接器行業通過引入原子力顯微鏡(AFM)表面粗糙度檢測,將5G基站射頻接點的接觸電阻波動范圍縮小至±0.15mΩ。據國際金屬材料研究院2024年案例庫顯示,采用智能檢測系統的金屬配件制造商,其產品一次交驗合格率平均提升23%,質量成本下降17%。
全鏈條質量保障機制
構建了覆蓋材料、工藝、檢測的三級質控體系。在原材料階段實施輝光放電光譜(GDOES)成分分析,工藝過程設置13個在線監測節點,終檢環節引入機器視覺自動識別系統。某軍工企業通過建立"熱處理-噴丸-鍍層"數據關聯模型,使航空作動筒表面殘余應力分布均勻性提高41%,疲勞壽命突破10^7次循環。實驗室能力驗證(PT)數據顯示,參與ISO 17025認證的檢測機構,其顯微硬度測試結果不確定度已穩定控制在HV0.5范圍內。
面向工業4.0發展趨勢,建議行業重點突破三個方向:開發基于太赫茲波的深層缺陷檢測技術,構建表面處理大數據知識圖譜,推廣微型化原位檢測裝備。同時應加快制定適應新型復合涂層的檢測標準,推動AI算法在異常模式識別中的應用。通過檢測技術創新與制造工藝的深度融合,金屬配件表面質量控制正從被動式檢驗向預測性維護演進,為智能制造高質量發展注入新動能。

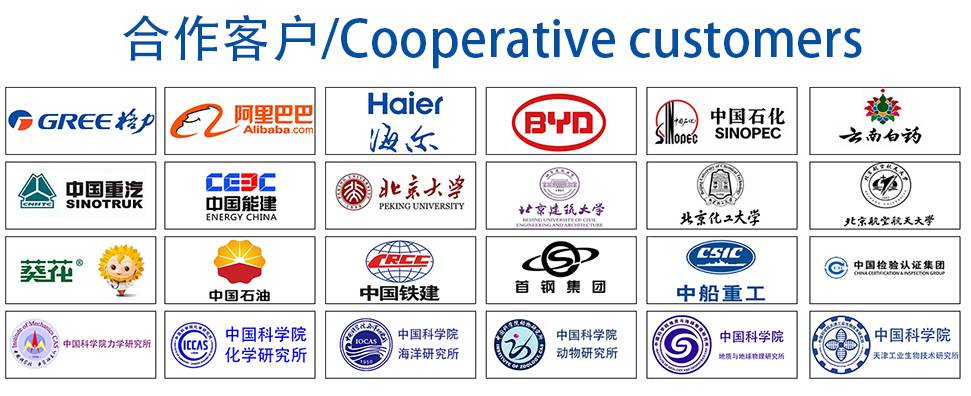