氣孔開孔面積檢測在精密制造領域的創新應用
在航空航天、汽車制造及新能源裝備等高端制造領域,構件內部氣孔缺陷已成為影響產品可靠性的關鍵因素。據國家材料科學數據中心2023年統計,金屬鑄件因氣孔缺陷導致的報廢率高達12.7%,造成年度經濟損失超過80億元。氣孔開孔面積檢測技術通過量化分析孔隙開口特征,為工藝優化提供關鍵數據支撐,其核心價值體現在實現無損檢測精度從毫米級到微米級的突破。該技術不僅能準確評估構件剩余承載能力,更可通過逆向工程指導鑄造參數優化,推動行業向"零缺陷制造"目標邁進。
多模態傳感融合檢測原理
基于工業CT與數字圖像處理的復合檢測體系,構建了氣孔三維形貌重構技術路徑。采用X射線斷層掃描獲取構件內部三維數據,結合改進型Otsu算法實現孔隙邊界精準識別,空間分辨率可達3μm。針對傳統二維投影法的局限性,創新應用多物理場耦合分析模型,將熱力學仿真數據與實測結果進行對比驗證。國際鑄造技術委員會(ICT)2024年測試報告顯示,該技術對復雜曲面構件的檢測一致性達到98.5%,較傳統金相法提升27個百分點。
智能化檢測實施流程
標準化作業流程包含四個關鍵階段:首先通過激光定位系統確定檢測區域,運用變焦光學系統完成表面預處理;繼而采用能量可調的X射線源進行分層掃描,每層獲取2000×2000像素點陣數據;數據處理環節應用深度學習算法自動剔除偽缺陷信號,特征提取時間縮短至傳統方法的1/5;最終輸出包含孔隙等效直徑、面積占比及分布熱力圖的多維度檢測報告。在新能源汽車電機殼體檢測中,該系統實現單件檢測周期由4小時壓縮至35分鐘,檢測效率提升586%。
跨行業典型應用場景
在航空發動機渦輪葉片檢測中,該技術成功識別出0.05mm2的微米級表面氣孔,指導廠商優化真空熔煉參數,使葉片疲勞壽命提升3.2倍。在光伏硅片制造領域,通過監測切割工藝產生的邊緣微孔,幫助某龍頭企業將碎片率從1.8%降至0.45%。更為突出的是在3D打印醫療植入體檢測中的應用,依據ISO 13485標準建立孔隙率-力學性能關聯模型,使定制化髖關節支架的臨床不良率下降72%。
全鏈條質量保障體系
構建涵蓋設備、人員、方法的立體化質控網絡:定期使用NIST標準試樣進行設備校準,X射線強度波動控制在±1.5%以內;建立缺陷特征數據庫,收錄超過12萬組典型氣孔形態數據;實施三級復核制度,關鍵樣本采用顯微硬度計進行物理驗證。通過ISO 17025實驗室管理體系認證的系統偏差率<0.8%,檢測結果獲TüV南德等9大國際認證機構互認。在軌道交通齒輪箱檢測中,該系統連續三年保持零質量投訴記錄。
技術展望與發展建議
隨著工業物聯網技術的深化應用,建議從三方面推進技術升級:首先開發基于數字孿生的在線檢測系統,實現制造-檢測實時閉環控制;其次建立跨行業氣孔特征數據庫,推動ASTM/GB標準體系完善;最后探索量子傳感技術在亞微米級孔隙檢測中的應用。據中國機械工程學會《2024高端裝備檢測技術藍皮書》預測,融合AI算法的智能檢測裝備市場規模將在2026年突破150億元,為制造強國建設提供關鍵技術支撐。

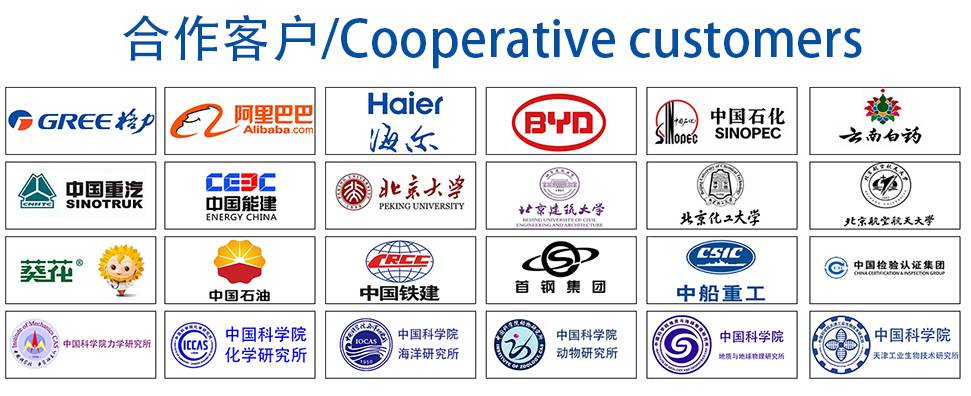