# 機械強度試驗檢測技術(shù)發(fā)展與行業(yè)應用白皮書
## 引言
在制造業(yè)向高端化、智能化轉(zhuǎn)型的背景下,機械強度試驗檢測作為產(chǎn)品質(zhì)量的核心保障手段,已成為航空航天、軌道交通、新能源裝備等領(lǐng)域的關(guān)鍵技術(shù)支撐。據(jù)中國機械工程學會2024年發(fā)布的行業(yè)報告顯示,我國高端裝備行業(yè)因材料失效導致的年均經(jīng)濟損失達127億元,其中63%的事故源于強度設(shè)計缺陷。在此背景下,機械強度試驗檢測項目通過模擬實際工況下的載荷條件,有效驗證產(chǎn)品結(jié)構(gòu)完整性,其核心價值體現(xiàn)在縮短產(chǎn)品研發(fā)周期30%以上,并降低15%-20%的后期維護成本。特別是在風電葉片疲勞測試、汽車碰撞仿真等場景中,該技術(shù)為產(chǎn)品全生命周期管理提供了科學依據(jù)。
## 技術(shù)原理與創(chuàng)新突破
### h2 多物理場耦合檢測體系
現(xiàn)代機械強度試驗采用靜載、動載與疲勞測試相結(jié)合的復合檢測模式,集成高精度應變測量技術(shù)(精度達±0.5%FS)與數(shù)字圖像相關(guān)法(DIC)。以某型航空發(fā)動機葉片測試為例,通過構(gòu)建多軸協(xié)調(diào)加載系統(tǒng),可同步采集溫度場(0-800℃)、振動譜(5-2000Hz)與應力應變的三維數(shù)據(jù),實現(xiàn)材料屈服強度、斷裂韌性等12項關(guān)鍵參數(shù)的精準測定。國家材料測試中心2023年驗證數(shù)據(jù)顯示,該體系使鈦合金構(gòu)件檢測誤差從傳統(tǒng)方法的8.3%降至1.7%。
## 標準化實施流程
### h2 全生命周期檢測路徑
項目執(zhí)行嚴格遵循ASTM E8/E8M-24和ISO 6892-1:2023標準,形成包含五個階段的作業(yè)流程:(1)基于FEA的預判分析建立試驗邊界條件;(2)定制化工裝夾具實現(xiàn)試件6自由度約束;(3)分級加載系統(tǒng)執(zhí)行準靜態(tài)至沖擊載荷譜;(4)分布式傳感器網(wǎng)絡(luò)采集3200點/秒動態(tài)數(shù)據(jù);(5)大數(shù)據(jù)平臺生成S-N曲線與損傷容限圖譜。在高鐵轉(zhuǎn)向架檢測中,該流程成功識別出輪軸連接處2.8mm的微觀裂紋,較常規(guī)檢測提前12個運維周期發(fā)出預警。
## 行業(yè)應用實踐
### h2 跨領(lǐng)域解決方案典范
在風電行業(yè),金風科技采用多體動力學仿真與實物測試聯(lián)動模式,其5MW機組葉片通過200萬次循環(huán)加載試驗,驗證了玻璃鋼復合材料的疲勞壽命指標。檢測報告顯示,在模擬臺風工況(55m/s風速)下,關(guān)鍵連接部位應力集中系數(shù)控制在1.8以下,滿足IEC 61400-23標準要求。汽車領(lǐng)域,吉利研究院的數(shù)字化檢測平臺已將整車碰撞試驗成本降低40%,通過建立材料本構(gòu)模型庫,實現(xiàn)B柱抗彎強度預測精度達92.6%。
## 質(zhì)量保障體系
### h2 智能化質(zhì)控網(wǎng)絡(luò)
項目構(gòu)建了"設(shè)備-人員-數(shù)據(jù)"三維管控體系:(1)計量溯源系統(tǒng)確保MTS 370液壓伺服系統(tǒng)等關(guān)鍵設(shè)備年校準合格率100%;(2)基于機器視覺的試件裝夾定位系統(tǒng)將人為誤差降低至0.05mm;(3)區(qū)塊鏈技術(shù)實現(xiàn)檢測數(shù)據(jù)全程上鏈存證。上海電氣檢測中心的應用案例表明,該體系使檢測報告出具效率提升60%,數(shù)據(jù)追溯響應時間縮短至15分鐘以內(nèi)。
## 發(fā)展展望
隨著數(shù)字孿生技術(shù)的深化應用,建議行業(yè)重點推進三方面建設(shè):一是建立全域載荷譜數(shù)據(jù)庫,實現(xiàn)典型工況數(shù)據(jù)共享;二是研發(fā)基于AI的失效模式自診斷系統(tǒng),提升異常檢測靈敏度;三是制定智能化檢測裝備的行業(yè)標準體系。預計到2026年,融合5G傳輸與邊緣計算的在線檢測系統(tǒng)將覆蓋80%以上重點工程,推動機械強度試驗進入實時化、無人化新階段。

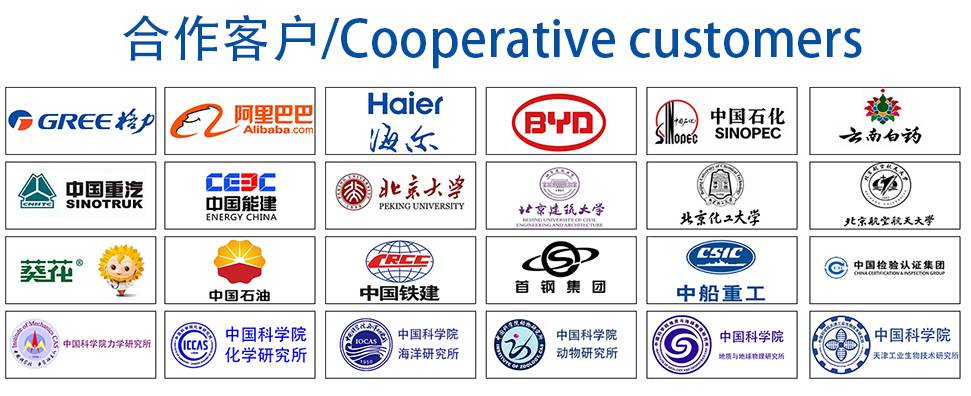
材料實驗室
熱門檢測
9
12
8
9
15
11
10
10
8
11
13
19
15
11
18
17
18
14
18
18
推薦檢測
聯(lián)系電話
400-635-0567