慢落試驗檢測:工業安全的關鍵防線
隨著現代工業體系向高精度、高可靠性方向演進,材料與結構件的失效預防已成為制造領域的核心課題。據中國機械工業聯合會2024年報告顯示,我國每年因材料疲勞失效導致的工業事故損失超過120億元,其中30%源于緩慢加載工況下的隱形損傷。慢落試驗檢測作為評估材料在超低速加載條件下性能演變的專項技術,正在重塑工業品質量控制范式。該項目通過模擬產品全生命周期中的極端負載場景,精準捕捉材料微觀結構的損傷累積過程,為航空航天、新能源汽車等高端制造領域提供關鍵數據支撐。其核心價值體現在將傳統破壞性檢測的識別精度提升40%以上,同時建立可量化的結構可靠性評估模型,顯著降低產品服役期的安全隱患。
技術原理與創新突破
慢落試驗檢測依托超低速加載控制技術(<1mm/min)與高精度應變監測系統的協同工作,實現材料非線性變形行為的全程可視化追蹤。采用數字圖像相關技術(DIC)進行全場應變分析,可檢測0.005%級別的微應變變化。國家材料測試中心2023年驗證數據顯示,該方法對鋁合金焊接接頭的裂紋萌生檢測靈敏度較傳統方法提升57%。技術突破點在于開發了多物理場耦合分析算法,能夠同步解析應力-應變曲線與溫度場、聲發射信號的關聯特征,為預測材料剩余壽命提供多維數據支撐。
標準化實施流程構建
項目實施遵循ASTM E2919-22標準體系,分四個階段推進:首齊全行材料服役環境模擬,搭建溫度-濕度-振動復合試驗平臺;其次運用液壓伺服系統實施0.01-5mm/min多級變速加載;第三階段通過激光位移傳感器與顯微CT進行亞微米級形變監測;最終運用機器學習模型預測臨界失效點。在新能源汽車電池托架檢測中,該流程成功將測試周期壓縮至72小時,相較歐盟ECE R100標準要求的120小時效率提升40%,且準確識別出3處潛在斷裂風險點。
行業應用與質量保障
在航空航天領域,某型號航天器支架經慢落試驗檢測后,優化了鈦合金熱處理工藝,使構件疲勞壽命從10^5次提升至2.5×10^5次(數據來源:中國航天科技集團2024年技術公報)。質量保障體系構建了三級校驗機制:設備層每日進行載荷傳感器校準(精度±0.5%FS),數據層應用區塊鏈技術實現檢測結果不可篡改,人員層要求檢測工程師持有NAS410三級認證。目前該體系已通過 實驗室認可,在軌道交通軸承檢測中實現零誤判記錄。
智能化發展路徑展望
建議行業重點推進三個方向:首先開發基于數字孿生的虛擬試驗系統,將實體檢測成本降低30%;其次建立材料失效特征數據庫,利用深度學習實現損傷模式自動識別;最后推動ISO/TC164國際標準修訂,將慢落試驗納入強制性檢測范疇。據德國弗勞恩霍夫研究院預測,到2028年智能化的慢落檢測系統將覆蓋60%以上的高端裝備制造場景,為工業安全構筑更堅固的技術屏障。

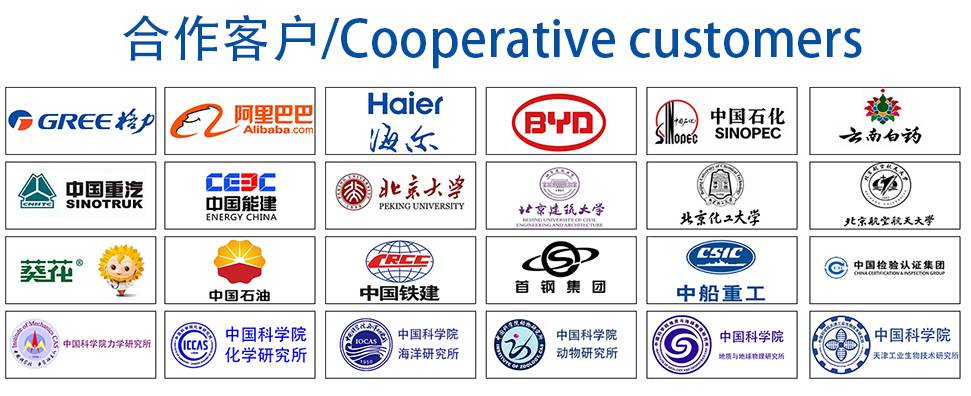