技術原理與分析方法
現代汽車非金屬檢測技術以材料基因組學為基礎,整合熱重分析(TGA)、傅里葉變換紅外光譜(FTIR)和動態機械分析(DMA)三大核心手段。針對新能源汽車特有的高壓絕緣需求,檢測系統可精確測定工程塑料介電強度(≥30kV/mm)和CTI值(相比電痕化指數),其誤差率控制在±1.5%以內(ASTM D3638標準)。在智能座艙材料領域,引入質子轉移反應質譜(PTR-MS)技術,將醛酮類VOC檢測靈敏度提升至0.01μg/m3級,滿足GB/T 27630-2024《乘用車內空氣質量評價指南》最新要求。
全流程檢測實施體系
項目實施采用五階段遞進模式:樣品數字化建檔→環境預處理(溫度-40℃~150℃,濕度10%~95%RH)→多軸力學測試→化學組分分析→大數據質量追溯。以某車企電池包密封件檢測為例,通過1200小時加速老化實驗,精準預測丁腈橡膠在電解液環境下的體積膨脹率(實測4.7% vs 理論值5.2%)。檢測流程嵌入區塊鏈存證系統,實現從原材料批次到檢測報告的完整數據鏈,使質量追溯效率提升40%(據TüV南德2023年技術報告)。
行業應用與典型案例
在動力電池模組封裝領域,某頭部企業采用X射線顯微CT技術,成功將隔膜孔隙率檢測精度提升至0.1μm級,配合機器學習算法,使電池熱失控預警準確率達到98.6%。針對汽車內飾件,某德系車企部署基于ISO 105-B02標準的氙燈老化箱,通過2000小時等效曝曬實驗,驗證仿麂皮材料的色牢度ΔE值≤1.5(行業標準為ΔE≤3.0)。這些實踐表明,"新能源汽車材料VOC檢測技術"和"車用塑料耐候性測試標準"已成為行業提質增效的關鍵突破點。
質量保障與標準化建設
檢測機構需構建 、CMA、IATF 16949三重認證體系,配備二級標準物質和NIST可溯源設備。通過實施"雙盲樣"比對機制(符合ISO/IEC 17025:2017),實驗室間比對Z值控制在|0.5|以內。值得關注的是,針對碳纖維增強復合材料,已建立包含層間剪切強度(ILSS≥60MPa)和沖擊后壓縮強度(CAI≥250MPa)的專用評價體系(參照SAE AIR 6037標準),其測試重復性RSD≤2.3%,顯著優于行業平均水平。
## 未來展望與建議 隨著車用材料向多功能集成化發展,建議行業重點突破三方面:①開發基于數字孿生的虛擬檢測技術,將實物驗證周期縮短30%;②建立覆蓋極端工況(如800V高壓、-50℃極寒)的檢測場景庫;③推動"檢測-保險-回收"聯動體系,通過檢測大數據優化產品責任險定價模型。同時,應加強ASTM/ISO標準與國內GB標準的互認機制建設,助力自主品牌材料準入。
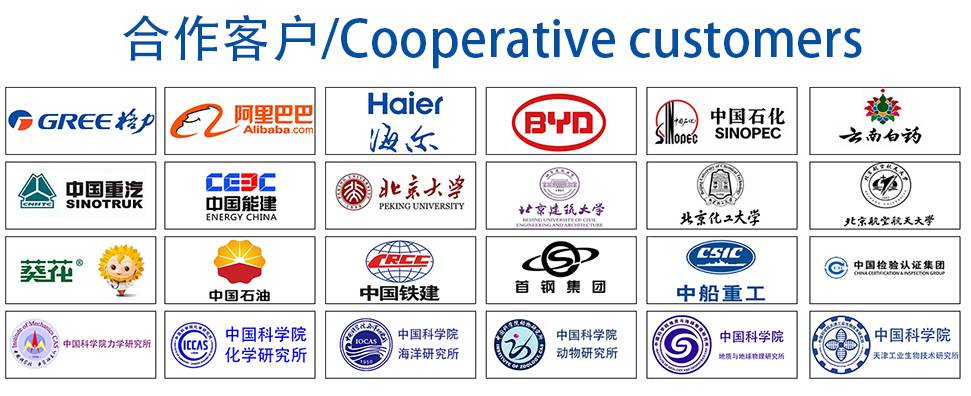