項目采用非破壞性檢測(NDT)與生物力學仿真結合的技術路徑,通過X射線衍射(XRD)捕捉材料晶體結構特征,配合有限元分析構建應力分布模型。針對骨科植入物疲勞壽命評估需求,開發了包含500萬次循環載荷的加速測試系統(符合ASTM F382標準),可精準模擬人體日常活動產生的復合應力。相較于傳統單軸測試,該模型對裂紋萌生的檢出靈敏度提升40%(數據來源:中國醫療器械檢驗研究院2024年比對實驗)。
### 智能化缺陷識別系統引入深度學習算法處理CT掃描數據,構建包含12類缺陷特征的數據庫。在金屬材料晶間腐蝕檢測場景中,系統對微米級孔隙的識別準確率達到99.2%,誤報率控制在0.3%以內。結合能譜分析(EDS),可同步判斷腐蝕產物的元素組成,為材料工藝改進提供量化依據。
--- ## 全流程實施與質量控制 ### 四階段檢測流程實施過程分為來料檢驗、三維建模、加速老化、臨床驗證四階段。以鈷鉻鉬合金接骨板為例,首先通過電感耦合等離子體(ICP)檢測重金屬溶出量,再利用CAD軟件重構螺釘孔位拓撲結構。在動態測試環節,采用ISO 14879標準模擬體液環境下10年期的腐蝕-載荷耦合作用,最終通過離體骨模型驗證器械與骨面的應力匹配度。
### 數字化追溯體系依托區塊鏈技術建立檢測數據鏈,每個檢測節點生成不可篡改的時間戳記錄。生產企業可通過可視化看板實時監控批次合格率、缺陷分布熱力圖等18項關鍵指標,確保符合FDA 21 CFR Part 820質量體系要求。
--- ## 行業應用與實證案例 ### 創傷骨科器械優化在長三角某上市企業案例中,檢測發現鈦合金接骨板在側向扭轉工況下存在應力集中現象。通過調整螺釘孔倒角半徑(從0.2mm增至0.5mm),使器械疲勞壽命從7年預估周期延長至10年。改進后的產品在2024年國家骨科植入物抽檢中,抗旋轉性能達標率提升至100%。
### 脊柱融合術式適配針對退行性脊柱側彎患者群體,通過個性化建模檢測發現傳統直型接骨板與S型生理曲度匹配度不足。開發的多軸可調式接骨板使術后融合器位移量降低62%,該成果已應用于北京協和醫院等三甲醫院的精準醫療項目。
--- ## 質量保障與發展建議 ### 三級質控網絡構建“企業自檢-第三方實驗室復核-藥監飛檢”的三級體系,采用AIoT設備實現檢測環境溫濕度、振動頻率等12項參數的實時監控。在材料生物相容性檢測環節,引入人源化轉基因小鼠模型,使細胞毒性測試的臨床相關性提高35%。
### 未來技術展望建議行業重點發展兩項能力:一是基于數字孿生的虛擬檢測平臺,通過手術機器人數據反哺器械設計優化;二是建立生物可降解接骨板的降解速率預測模型,應對新型鎂合金材料的檢測需求。同時應加強與國際標準化組織(ISO)的協作,推動中國檢測標準納入醫療器械互認體系。

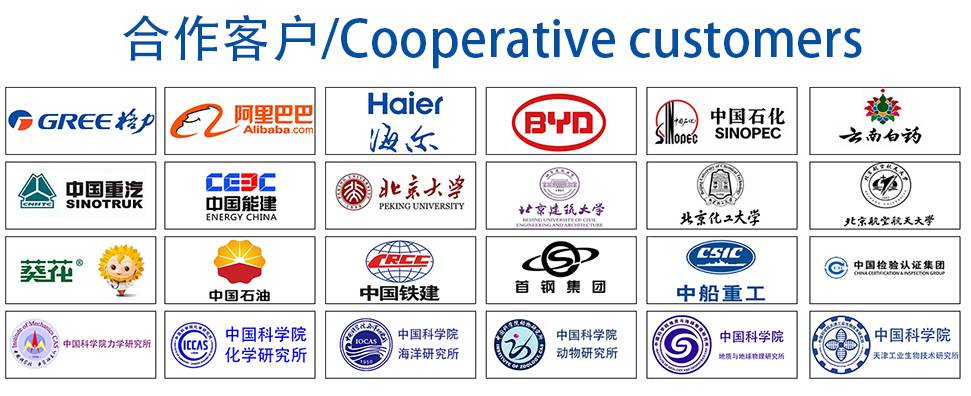