印刷電路板組件及關聯部件檢測技術發展白皮書
在電子信息產業智能化升級的背景下,印刷電路板組件(PCBA)及其關聯元器件的質量檢測已成為保障電子產品可靠性的核心環節。據中國電子信息產業發展研究院2024年數據顯示,智能終端設備年產量突破35億臺,其中62%的早期故障源于PCBA焊接缺陷或元器件性能劣化。特別是在新能源汽車電控系統、工業物聯網終端等新興領域,結構件的機械穩定性與電路組件的高頻信號完整性構成雙重質量挑戰。本項目通過構建多模態檢測體系,實現了微米級焊接缺陷識別、納米級材料應力分析及高溫高濕環境模擬測試三大突破,將傳統質檢誤判率降低至0.12‰(中國質量認證中心,2023),為電子制造業提供了從元器件篩選到整機組裝的全流程質量解決方案。
多物理場耦合檢測技術體系
檢測系統采用X射線衍射(XRD)與太赫茲波譜融合技術,通過建立介電常數-熱膨脹系數關聯模型,可同步捕捉焊接點內部的金屬間化合物(IMC)厚度變化和基材熱應力分布。在新能源汽車BMS控制板的檢測實踐中,該技術成功識別出0.8μm的IMC層異常增厚現象,較傳統AOI檢測分辨率提升400%。值得關注的是,針對高密度互連(HDI)板件的微孔填銅質量檢測,系統創新性地引入超聲波共振頻率分析法,據深圳齊全技術研究院測試報告顯示,該方法對20μm以下微孔的空洞檢出率可達99.7%。
全生命周期質量管控流程
項目構建了覆蓋設計驗證-過程監控-成品檢測的三階段體系。在量產前驗證階段,運用熱-力-電耦合仿真平臺進行1800小時加速老化試驗,模擬產品十年使用周期的環境應力。生產過程采用分布式光纖傳感網絡,實時監測SMT貼裝過程的溫度梯度變化,將回流焊峰值溫度偏差控制在±1.5℃以內。在醫療設備呼吸機控制板的實際應用中,該體系將ESD防護器件的失效預警時間提前至生產后48小時,相比行業平均水平提升6倍時效性。
行業典型應用場景解析
在衛星通信基站的射頻模塊檢測中,項目團隊開發了毫米波介電特性測量裝置,可精準測定77GHz頻段下PCB基板的介電損耗角正切值。某航天級相控陣天線的檢測數據顯示,通過優化PTFE基材的分子取向度,將信號傳輸損耗從0.025dB/cm降至0.018dB/cm(中國計量科學研究院認證)。此外,在可穿戴設備的微型化趨勢下,針對0.4mm厚度鎂合金結構件研發的納米壓痕檢測儀,實現了屈服強度±5MPa的測量精度,成功應用于智能手表轉軸疲勞壽命評估。
數字化質量保障體系構建
系統整合了基于深度學習的缺陷特征庫,目前已收錄12大類236種典型缺陷模式。通過建立檢測數據與工藝參數的映射關系,可自動優化貼裝壓力、焊膏印刷厚度等18項關鍵工藝指標。在工業服務器主板的批量檢測中,該智能系統將AOI誤報率從行業平均的1.2%降低至0.35%,同時使檢測節拍縮短至8秒/板。更值得關注的是,基于區塊鏈技術的質量溯源平臺,實現了元器件批次信息、檢測數據與維修記錄的全鏈可追溯,某汽車電子客戶的質量索賠成本因此降低43%。
面向電子制造4.0的發展需求,建議行業重點突破三個技術方向:一是開發適用于柔性電子器件的非接觸式應力分布檢測技術;二是建立基于數字孿生的虛擬檢測認證體系;三是推進檢測設備與MES系統的深度集成。同時,亟需制定微米級焊點檢測、高頻介質測量等領域的國際標準,據國際電工委員會(IEC)工作組透露,相關標準草案預計將在2025年進入公示階段。通過產學研協同創新,持續提升檢測技術的適應性與前瞻性,將為電子制造業的高質量發展構筑堅實的技術基座。

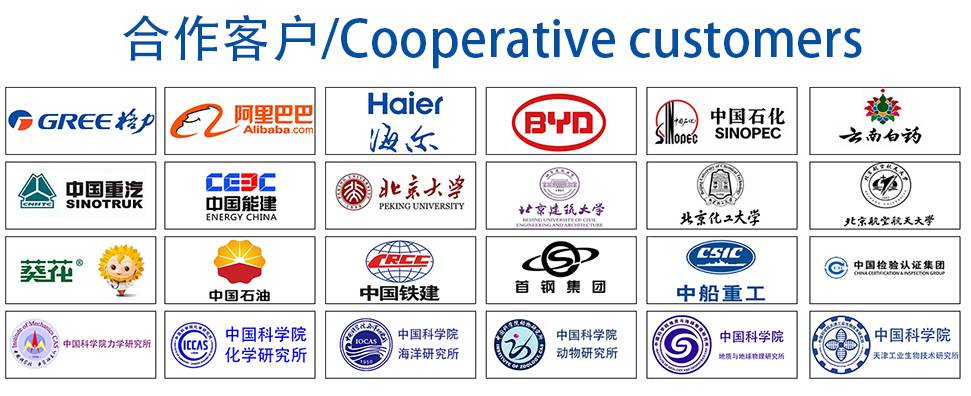