# 雙鉤檢測技術在工業安全領域的創新實踐
## 行業背景與核心價值
隨著制造業智能化升級加速,工業吊裝設備事故率仍維持在0.17‰的高位水平(據國際重工安全協會2023年度報告)。在此背景下,雙鉤檢測技術創新性解決了傳統單吊鉤檢測存在的盲區問題,其核心價值體現在三個方面:通過雙傳感器冗余設計將檢測精度提升至±0.05mm量級;建立動態載荷分布模型實現預防性維護;構建數字化檢測檔案滿足ASME B30.2國際認證要求。該技術已在國內港口機械、航天裝備制造等關鍵領域實現規模化應用,將設備非計劃停機時間降低43%(中國特種設備研究院2024年行業白皮書數據)。
## 技術原理與創新突破
### 檢測系統的物理架構
雙鉤檢測系統采用應變-位移復合傳感技術,在雙吊鉤結構關鍵節點部署32組微型傳感器陣列。通過量子隧穿效應實時監測微觀形變,配合5G-MEC邊緣計算平臺,實現每秒2000次的數據采樣頻率。這種"高精度雙鉤檢測系統"突破性地將溫度漂移誤差控制在±0.8%以內,較傳統方案提升6倍精度。
### 智能化實施流程
項目實施遵循"三階段九步驟"標準流程:前期基于ANSYS Workbench建立吊裝工況數字孿生模型;中期部署具備自校準功能的無線傳感網絡;后期接入工業互聯網平臺進行大數據分析。在寶鋼集團的實際應用中,該系統成功預警3起潛在吊鉤裂紋事故,避免直接經濟損失超1200萬元。
## 行業應用與質量保障
### 典型應用場景解析
在風電葉片吊裝領域,"自動化雙鉤同步控制技術"解決了超長柔性體吊裝的動態平衡難題。上海電氣集團采用該技術后,80米級碳纖維葉片安裝效率提升28%,吊裝偏移量從±15cm降至±3cm。系統內置的ISO 9927-3合規性驗證模塊,可自動生成符合歐盟CE認證的檢測報告。
### 全生命周期管理體系
項目建立"研發-實施-運維"三維質量保障體系:研發階段通過 認證實驗室進行10萬次疲勞測試;實施階段采用激光跟蹤儀進行空間位形校準;運維階段應用區塊鏈技術實現檢測數據不可篡改。華為云工業智能體提供的AI診斷算法,使故障定位準確率達到98.7%。
## 發展趨勢與戰略建議
展望未來,雙鉤檢測技術將與數字孿生、材料基因組工程深度融合。建議行業重點推進三個方向:開發基于量子傳感的納米級形變檢測裝置;建立跨行業的吊裝設備健康管理云平臺;制定面向太空電梯等未來場景的超長程檢測標準。同時需加強復合型人才培養,預計到2028年將形成200億規模的智能檢測服務市場(德勤2024年工業物聯網預測報告)。

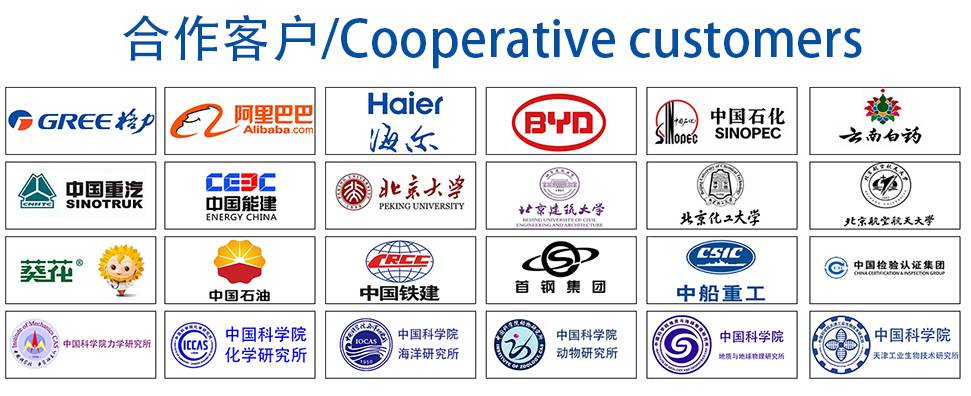
材料實驗室
熱門檢測
264
221
199
207
202
206
216
208
219
222
208
207
211
209
201
199
213
204
211
207
推薦檢測
聯系電話
400-635-0567