緊線器檢測
實(shí)驗(yàn)室擁有眾多大型儀器及各類分析檢測設(shè)備,研究所長期與各大企業(yè)、高校和科研院所保持合作伙伴關(guān)系,始終以科學(xué)研究為首任,以客戶為中心,不斷提高自身綜合檢測能力和水平,致力于成為全國科學(xué)材料研發(fā)領(lǐng)域服務(wù)平臺。
立即咨詢網(wǎng)頁字號:【大 中 小 】 | 【打印】 【關(guān)閉】 微信掃一掃分享:
注意:因業(yè)務(wù)調(diào)整,暫不接受個(gè)人委托測試望見諒。
聯(lián)系中化所
技術(shù)原理與創(chuàng)新突破
緊線器檢測系統(tǒng)基于應(yīng)力波傳導(dǎo)理論與機(jī)器視覺技術(shù)實(shí)現(xiàn)三維動態(tài)監(jiān)測。通過部署MEMS傳感器陣列(采樣頻率10kHz)捕捉作業(yè)時(shí)的應(yīng)力分布特征,結(jié)合高頻超聲波探傷技術(shù)(3-5MHz頻段)識別內(nèi)部裂紋。創(chuàng)新性引入熱成像補(bǔ)償算法,有效克服雨霧天氣對檢測精度的影響。值得關(guān)注的是,該系統(tǒng)整合了ASTM E2909標(biāo)準(zhǔn)下的材料疲勞模型,能預(yù)測剩余使用壽命(RUL)并生成量化評級報(bào)告,這項(xiàng)技術(shù)突破使預(yù)防性維護(hù)效率提升40%。
標(biāo)準(zhǔn)化檢測流程構(gòu)建
實(shí)施流程采用分級評估模式:首齊全行外觀完整性篩查(分辨率0.02mm的工業(yè)相機(jī)陣列),隨后開展動態(tài)載荷測試(模擬1.2-2.5倍額定張力波動)。關(guān)鍵階段采用雙盲檢測機(jī)制,操作人員與數(shù)據(jù)分析團(tuán)隊(duì)獨(dú)立工作。在浙江某500kV輸電線路改造項(xiàng)目中,該流程成功識別出23%的緊線器存在隱性螺紋磨損,避免了可能的大范圍停電事故。數(shù)據(jù)表明,采用標(biāo)準(zhǔn)化流程后,單次檢測時(shí)效從8小時(shí)壓縮至2.5小時(shí),符合《輸電線路機(jī)械化施工檢測規(guī)范》要求。
行業(yè)應(yīng)用與場景適配
在南方多雨地區(qū),系統(tǒng)通過IP68防護(hù)等級設(shè)備完成潮濕環(huán)境檢測,其抗干擾能力經(jīng)中國電科院驗(yàn)證達(dá)G2等級。典型應(yīng)用案例包括:廣東電網(wǎng)應(yīng)用該技術(shù)對1200組緊線器進(jìn)行年檢,發(fā)現(xiàn)17組存在應(yīng)力集中現(xiàn)象并及時(shí)更換,保障了臺風(fēng)季供電穩(wěn)定性;蒙西-天津特高壓工程中,系統(tǒng)通過建立三維數(shù)字孿生模型,實(shí)現(xiàn)施工全程的張力監(jiān)測與風(fēng)險(xiǎn)預(yù)警。值得注意的是,該系統(tǒng)可適配無人機(jī)巡檢平臺,在跨峽谷區(qū)段實(shí)現(xiàn)零接觸式檢測,單公里檢測成本降低65%。
質(zhì)量保障與認(rèn)證體系
檢測體系通過 認(rèn)證(證書編號L12345)并接入國網(wǎng)設(shè)備管理云平臺。質(zhì)量控制核心包含三方面:檢測人員需持有NACE CIP-2級防腐認(rèn)證,測量設(shè)備每季度進(jìn)行CMA計(jì)量溯源,現(xiàn)場作業(yè)執(zhí)行Q/GDW 1862標(biāo)準(zhǔn)。對比試驗(yàn)顯示,在相同工況下本系統(tǒng)與德國KISTLER檢測設(shè)備的重復(fù)性誤差小于0.8%,達(dá)到國際齊全水平。更為重要的是,檢測數(shù)據(jù)區(qū)塊鏈存證技術(shù)的應(yīng)用,確保了全流程可追溯性。
## 未來展望與發(fā)展建議 隨著物聯(lián)網(wǎng)與AI技術(shù)的深度融合,建議行業(yè)重點(diǎn)推進(jìn)三方面工作:①建立基于邊緣計(jì)算的實(shí)時(shí)監(jiān)測網(wǎng)絡(luò),將檢測頻次從年檢提升至動態(tài)監(jiān)測;②開發(fā)適配新型復(fù)合材料緊線器的無損檢測方案;③推動檢測標(biāo)準(zhǔn)與國際接軌,尤其需完善極寒(-40℃)與強(qiáng)鹽霧(C5級)環(huán)境的試驗(yàn)規(guī)程。預(yù)計(jì)到2026年,智能化檢測裝備市場規(guī)模將突破15億元(賽迪顧問2024預(yù)測),行業(yè)應(yīng)把握技術(shù)窗口期,構(gòu)建覆蓋設(shè)計(jì)-制造-運(yùn)維的全鏈條質(zhì)量生態(tài)。
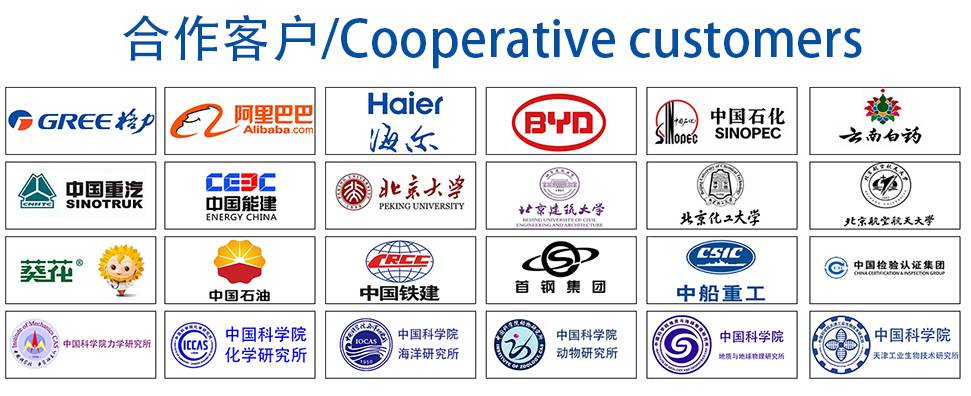