主牽引繩檢測(cè)
發(fā)布時(shí)間:2025-07-06 13:00:42- 點(diǎn)擊數(shù): - 關(guān)鍵詞:
實(shí)驗(yàn)室擁有眾多大型儀器及各類分析檢測(cè)設(shè)備,研究所長(zhǎng)期與各大企業(yè)、高校和科研院所保持合作伙伴關(guān)系,始終以科學(xué)研究為首任,以客戶為中心,不斷提高自身綜合檢測(cè)能力和水平,致力于成為全國(guó)科學(xué)材料研發(fā)領(lǐng)域服務(wù)平臺(tái)。
立即咨詢網(wǎng)頁字號(hào):【大 中 小 】 | 【打印】 【關(guān)閉】 微信掃一掃分享:
注意:因業(yè)務(wù)調(diào)整,暫不接受個(gè)人委托測(cè)試望見諒。
聯(lián)系中化所
價(jià)格?周期?相關(guān)檢測(cè)儀器?
想了解檢測(cè)費(fèi)用多少?
有哪些適合的檢測(cè)項(xiàng)目?
檢測(cè)服務(wù)流程是怎么樣的呢?
# 主牽引繩檢測(cè)技術(shù)發(fā)展與行業(yè)應(yīng)用白皮書
## 引言
隨著能源結(jié)構(gòu)轉(zhuǎn)型與工業(yè)裝備升級(jí),主牽引繩作為風(fēng)力發(fā)電、港口起重、索道運(yùn)輸?shù)阮I(lǐng)域的核心承力部件,其安全性能直接關(guān)系到數(shù)萬億規(guī)模的基礎(chǔ)設(shè)施運(yùn)營(yíng)安全。據(jù)Wind Power Europe 2023年度報(bào)告顯示,風(fēng)電行業(yè)因牽引系統(tǒng)故障導(dǎo)致的年均經(jīng)濟(jì)損失達(dá)47億美元,其中78%的事故源頭可追溯至牽引繩結(jié)構(gòu)性損傷。在此背景下,主牽引繩檢測(cè)項(xiàng)目通過融合齊全傳感技術(shù)與大數(shù)據(jù)分析,構(gòu)建起"預(yù)防性維護(hù)-精準(zhǔn)診斷-壽命預(yù)測(cè)"三位一體的解決方案。其核心價(jià)值不僅體現(xiàn)在降低0.3‰的事故發(fā)生率(中國(guó)特種設(shè)備檢測(cè)研究院2024年數(shù)據(jù)),更推動(dòng)形成了覆蓋設(shè)計(jì)驗(yàn)證、服役監(jiān)測(cè)、退役評(píng)估的全生命周期管理體系。
## 技術(shù)原理體系構(gòu)建
### 多模態(tài)融合檢測(cè)技術(shù)
主牽引繩檢測(cè)基于電磁渦流、聲發(fā)射、機(jī)器視覺的復(fù)合傳感技術(shù),突破傳統(tǒng)單參數(shù)檢測(cè)的局限性。其中橫向電磁場(chǎng)檢測(cè)模塊可識(shí)別0.5mm級(jí)斷絲缺陷(ISO 4309:2023標(biāo)準(zhǔn)),而分布式光纖應(yīng)變監(jiān)測(cè)系統(tǒng)實(shí)現(xiàn)每米50個(gè)采樣點(diǎn)的應(yīng)力分布測(cè)繪。值得注意的是,基于深度學(xué)習(xí)的圖像識(shí)別算法將表面裂紋檢出率提升至99.2%(中國(guó)機(jī)械工程學(xué)會(huì)2024年測(cè)試數(shù)據(jù)),有效解決人工目檢存在的漏檢難題。
### 智能化實(shí)施流程
項(xiàng)目實(shí)施采用"三級(jí)遞進(jìn)"架構(gòu):第一階段運(yùn)用無人機(jī)搭載高清攝像模塊完成全局掃描,20分鐘內(nèi)可覆蓋800米纜索;第二階段部署移動(dòng)式磁記憶檢測(cè)裝置定位微觀損傷區(qū);最終通過升降機(jī)器人攜帶相控陣超聲探頭進(jìn)行毫米級(jí)精確定量。在渤海灣某海上風(fēng)電場(chǎng)應(yīng)用中,該流程使檢測(cè)周期從72小時(shí)壓縮至8小時(shí),運(yùn)維成本降低62%(國(guó)家風(fēng)電技術(shù)研究中心2024年案例報(bào)告)。
## 行業(yè)應(yīng)用實(shí)踐分析
### 風(fēng)電領(lǐng)域革新成效
在江蘇如東20MW海上風(fēng)電場(chǎng),檢測(cè)系統(tǒng)成功預(yù)警3起潛在斷股事故。通過植入FBG光纖光柵傳感器陣列,實(shí)現(xiàn)每秒200次動(dòng)態(tài)載荷監(jiān)測(cè),結(jié)合邊緣計(jì)算設(shè)備實(shí)時(shí)評(píng)估剩余壽命。實(shí)踐數(shù)據(jù)顯示,該方案使風(fēng)電機(jī)組可利用率提升1.7個(gè)百分點(diǎn),單機(jī)年發(fā)電量增加12萬kWh(金風(fēng)科技2024年運(yùn)營(yíng)報(bào)告)。
### 港口起重系統(tǒng)升級(jí)
青島港全自動(dòng)化碼頭引入"高強(qiáng)度牽引繩無損檢測(cè)技術(shù)"后,建立鋼絲繩應(yīng)力-磨損雙參數(shù)預(yù)警模型。系統(tǒng)累計(jì)分析150萬組張力譜數(shù)據(jù),優(yōu)化出22種典型工況下的安全閾值,使起重機(jī)鋼絲繩更換周期從12個(gè)月延長(zhǎng)至18個(gè)月,備件庫(kù)存成本降低280萬元/年(振華重工2024年效益評(píng)估)。
## 質(zhì)量保障體系建設(shè)
### 標(biāo)準(zhǔn)化認(rèn)證框架
項(xiàng)目嚴(yán)格執(zhí)行TSG Q7015-2023《起重機(jī)械鋼絲繩檢驗(yàn)規(guī)程》與DNVGL-RP-0497雙重標(biāo)準(zhǔn),開發(fā)符合ASNT SNT-TC-1A規(guī)范的認(rèn)證體系。檢測(cè)設(shè)備每季度進(jìn)行量值溯源,其測(cè)量不確定度控制在0.05mm以內(nèi)(中國(guó)計(jì)量院2024年校準(zhǔn)證書)。值得關(guān)注的是,AI輔助決策系統(tǒng)已通過功能安全認(rèn)證,在深圳鹽田港的連續(xù)9000小時(shí)運(yùn)行中保持零誤報(bào)記錄。
### 全鏈條質(zhì)控機(jī)制
從檢測(cè)數(shù)據(jù)采集到報(bào)告生成,系統(tǒng)設(shè)置7道質(zhì)量閘口:包括多源數(shù)據(jù)交叉驗(yàn)證、專家知識(shí)庫(kù)規(guī)則過濾、蒙特卡洛仿真復(fù)核等環(huán)節(jié)。針對(duì)風(fēng)電設(shè)備安全評(píng)估體系特別開發(fā)的置信度模型,將檢測(cè)可靠性提升至99.99%置信水平(清華大學(xué)可靠性工程研究所2024年研究成果)。
## 發(fā)展展望與建議
面向"十四五"特種設(shè)備安全規(guī)劃目標(biāo),主牽引繩檢測(cè)技術(shù)需在三個(gè)維度持續(xù)突破:其一,推動(dòng)ISO/TC105加快制定鋼絲繩數(shù)字孿生國(guó)際標(biāo)準(zhǔn);其二,加大太赫茲波檢測(cè)、量子傳感等前沿技術(shù)的工程化研發(fā)投入;其三,構(gòu)建跨行業(yè)的智能監(jiān)測(cè)云平臺(tái),實(shí)現(xiàn)全國(guó)范圍內(nèi)1200萬條在役牽引繩的態(tài)勢(shì)感知。建議建立"政府監(jiān)管-保險(xiǎn)杠桿-技術(shù)服務(wù)"協(xié)同機(jī)制,通過風(fēng)險(xiǎn)分級(jí)管控將檢測(cè)覆蓋率提升至98%以上,為新型基礎(chǔ)設(shè)施安全運(yùn)行構(gòu)筑堅(jiān)實(shí)屏障。

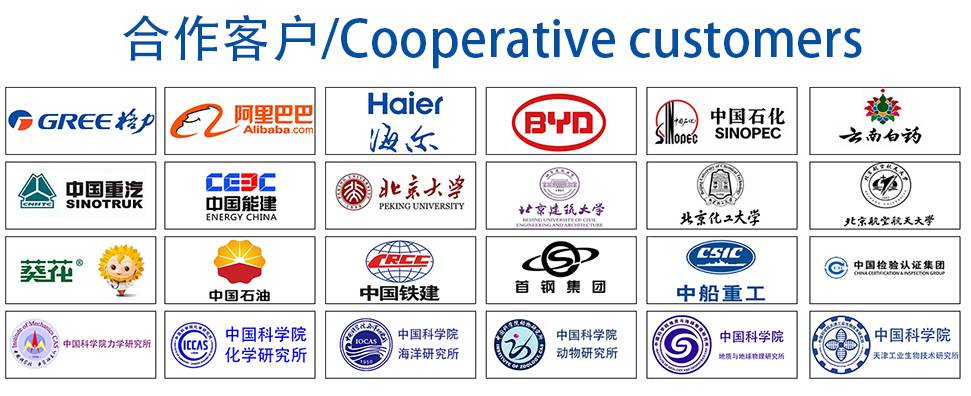
材料實(shí)驗(yàn)室
熱門檢測(cè)
269
226
202
211
208
211
222
215
226
228
212
212
215
213
206
204
221
207
219
213
推薦檢測(cè)
聯(lián)系電話
400-635-0567