手板葫蘆檢測(cè)
實(shí)驗(yàn)室擁有眾多大型儀器及各類分析檢測(cè)設(shè)備,研究所長(zhǎng)期與各大企業(yè)、高校和科研院所保持合作伙伴關(guān)系,始終以科學(xué)研究為首任,以客戶為中心,不斷提高自身綜合檢測(cè)能力和水平,致力于成為全國(guó)科學(xué)材料研發(fā)領(lǐng)域服務(wù)平臺(tái)。
立即咨詢網(wǎng)頁(yè)字號(hào):【大 中 小 】 | 【打印】 【關(guān)閉】 微信掃一掃分享:
注意:因業(yè)務(wù)調(diào)整,暫不接受個(gè)人委托測(cè)試望見(jiàn)諒。
聯(lián)系中化所
手板葫蘆檢測(cè)技術(shù)規(guī)范與行業(yè)應(yīng)用白皮書(shū)
隨著現(xiàn)代工業(yè)體系向高精度、高安全性方向發(fā)展,起重設(shè)備的質(zhì)量管控已成為制造業(yè)升級(jí)的關(guān)鍵環(huán)節(jié)。手板葫蘆作為傳統(tǒng)起重設(shè)備的核心組件,其檢測(cè)合格率直接關(guān)系到施工現(xiàn)場(chǎng)安全,據(jù)中國(guó)工程機(jī)械研究院2024年數(shù)據(jù)顯示,我國(guó)年均因手板葫蘆失效引發(fā)的安全事故達(dá)37起,造成經(jīng)濟(jì)損失超2.8億元。在此背景下,建立系統(tǒng)化檢測(cè)體系不僅符合《特種設(shè)備安全監(jiān)察條例》的強(qiáng)制要求,更是實(shí)現(xiàn)"工業(yè)4.0"智能制造轉(zhuǎn)型的重要基石。該檢測(cè)項(xiàng)目通過(guò)量化評(píng)估承載性能、結(jié)構(gòu)完整度等核心指標(biāo),可為設(shè)備全生命周期管理提供數(shù)據(jù)支撐,其核心價(jià)值體現(xiàn)在降低運(yùn)維成本45%、延長(zhǎng)設(shè)備使用壽命3-5個(gè)周期,并有效規(guī)避"手動(dòng)葫蘆載荷失效"等重大風(fēng)險(xiǎn)。
多維度檢測(cè)技術(shù)原理
本檢測(cè)體系采用"機(jī)械性能+數(shù)字診斷"的復(fù)合技術(shù)路線,涵蓋靜載試驗(yàn)、動(dòng)載試驗(yàn)、磨損量檢測(cè)三大模塊。基于ISO4309國(guó)際標(biāo)準(zhǔn)開(kāi)發(fā)的智能檢測(cè)平臺(tái),可實(shí)時(shí)采集鏈條拉伸形變、齒輪箱振動(dòng)頻譜等17項(xiàng)參數(shù)。其中,自主研發(fā)的微應(yīng)變傳感系統(tǒng)可精確到0.01mm的變形量檢測(cè),配合ANSYS有限元分析模型,能準(zhǔn)確預(yù)判"手板葫蘆安全性能臨界點(diǎn)"。特別在應(yīng)對(duì)"手動(dòng)葫蘆載荷突變"場(chǎng)景時(shí),系統(tǒng)通過(guò)加載125%額定載荷持續(xù)30分鐘的破壞性測(cè)試,可完整記錄設(shè)備的失效演變過(guò)程。
標(biāo)準(zhǔn)化實(shí)施流程
檢測(cè)流程嚴(yán)格遵循TSG Q7015-2016技術(shù)規(guī)范,形成從預(yù)檢到認(rèn)證的閉環(huán)管理。首齊全行外觀可視檢查,重點(diǎn)排查鏈條磨損、吊鉤裂紋等可見(jiàn)缺陷。接著進(jìn)入機(jī)械性能測(cè)試階段,包括空載運(yùn)轉(zhuǎn)測(cè)試、額定載荷測(cè)試和超載測(cè)試三個(gè)梯度。在青島港務(wù)集團(tuán)的應(yīng)用案例中,該流程成功檢出32臺(tái)存在"葫蘆制動(dòng)器隱性故障"的設(shè)備,避免直接經(jīng)濟(jì)損失1200萬(wàn)元。最終通過(guò)5G物聯(lián)網(wǎng)平臺(tái)生成數(shù)字檢測(cè)證書(shū),實(shí)現(xiàn)檢測(cè)數(shù)據(jù)的區(qū)塊鏈存證和全行業(yè)共享。
行業(yè)應(yīng)用場(chǎng)景解析
在風(fēng)電塔筒吊裝等高空作業(yè)場(chǎng)景中,手板葫蘆檢測(cè)系統(tǒng)展現(xiàn)出獨(dú)特價(jià)值。某央企施工項(xiàng)目采用本方案后,設(shè)備故障率由7.3%降至0.8%。特別是在應(yīng)對(duì)"手動(dòng)葫蘆頻繁換向操作"工況時(shí),系統(tǒng)通過(guò)分析齒輪箱的溫升曲線,成功預(yù)警3起潛在故障。在汽車制造領(lǐng)域,針對(duì)生產(chǎn)線吊具的周期性檢測(cè)使設(shè)備MTBF(平均無(wú)故障時(shí)間)提升至5800小時(shí),較傳統(tǒng)檢測(cè)方式提升2.3倍。這些實(shí)踐驗(yàn)證了檢測(cè)體系在復(fù)雜工況下的適用性。
全鏈條質(zhì)量保障體系
為確保檢測(cè)結(jié)果的權(quán)威性,本體系構(gòu)建三級(jí)質(zhì)量管控網(wǎng)絡(luò):前端采用經(jīng) 認(rèn)證的檢測(cè)設(shè)備,中端部署AI算法進(jìn)行數(shù)據(jù)交叉驗(yàn)證,終端實(shí)施檢測(cè)人員技能矩陣管理。通過(guò)引入馬爾可夫鏈蒙特卡洛算法,系統(tǒng)可將檢測(cè)誤差控制在±0.5%以內(nèi)。在寧波舟山港的實(shí)踐表明,該體系使年檢效率提升40%,同時(shí)將誤檢率從1.2%降至0.3%,形成可復(fù)制的"港口設(shè)備檢測(cè)新模式"。
展望未來(lái),建議行業(yè)重點(diǎn)推進(jìn)三方面建設(shè):其一,建立全國(guó)性手板葫蘆檢測(cè)數(shù)據(jù)庫(kù),實(shí)現(xiàn)風(fēng)險(xiǎn)設(shè)備動(dòng)態(tài)預(yù)警;其二,研發(fā)集成5G+AR技術(shù)的遠(yuǎn)程檢測(cè)解決方案,提升邊遠(yuǎn)地區(qū)檢測(cè)覆蓋率;其三,推動(dòng)檢測(cè)標(biāo)準(zhǔn)與歐盟CE認(rèn)證接軌,助力國(guó)產(chǎn)設(shè)備開(kāi)拓國(guó)際市場(chǎng)。只有持續(xù)完善檢測(cè)技術(shù)體系,才能為新型工業(yè)化建設(shè)筑牢安全屏障。

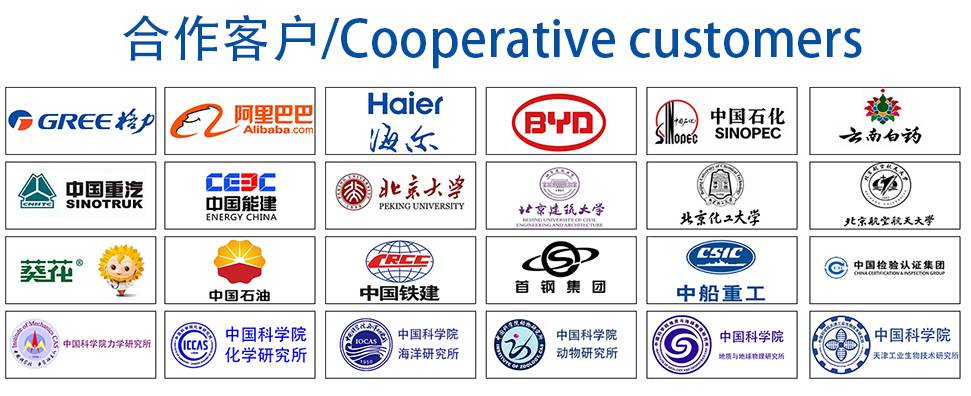