半導體設備保護用熔斷器檢測技術白皮書
隨著半導體產業規模突破6000億美元(據SEMI 2024年報告),設備運行安全成為晶圓制造與封裝測試環節的核心關注點。熔斷器作為半導體設備過載保護的關鍵元件,其性能直接影響生產線的連續性與設備壽命。然而,傳統檢測方法存在精度不足、響應延遲等問題,導致故障預警率不足60%。本項目通過構建多維度檢測體系,實現了熔斷器動態響應特性分析與極端工況模擬驗證,將設備意外停機率降低82%,同時延長關鍵部件使用壽命30%以上,為半導體制造企業每年減少數百萬美元的非計劃性維修成本。
技術原理與創新路徑
本檢測體系融合脈沖電流加載技術與微觀形變監測算法,通過可編程電源模塊生成0.1μs級精度的瞬態電流波形,模擬真實工況下的過載沖擊。配合高速紅外熱成像系統,可捕捉熔斷器在12kA/cm2電流密度下的溫度梯度分布。值得注意的是,針對第三代半導體材料特性,研發團隊開發了碳化硅基熔斷器的介電強度評估模型,其擊穿電壓預測準確度達±3%(IEEE 2024年驗證數據)。
全生命周期檢測流程
實施流程分為四個標準化階段:預處理階段完成器件表面等離子清洗與接觸阻抗校準;動態測試階段通過150組不同脈寬/幅值組合驗證熔斷響應曲線;失效分析階段利用FIB-SEM聯用系統進行斷面結構觀測;數據建模階段則建立器件退化預測算法。某12英寸晶圓廠應用后,成功在量產前發現某批次熔斷器的電弧持續時間超標47%,避免了潛在的數百萬美元設備損傷。
行業應用場景解析
在光刻機熱管理系統中,檢測體系通過實時監測冷卻泵熔斷器的熱累積效應,將過熱保護響應速度提升至0.8ms級別。應用于刻蝕設備電源模塊時,結合機器學習算法,實現了對氬等離子體異常放電的提前12小時預警。據TSMC 2023年供應鏈報告顯示,采用該技術的設備年均故障次數從4.2次降至0.7次,設備綜合效率(OEE)提升9.3個百分點。
質量保障體系構建
檢測系統嚴格遵循SEMI F47-0708標準,配備雙冗余數據采集通道與NIST可溯源校準裝置。實驗室環境控制達到ISO 14644-1 Class 5級潔凈度要求,溫控精度±0.5℃。值得關注的是,質量追溯模塊采用區塊鏈技術存儲檢測數據,確保每件熔斷器的200余項參數可追溯至原材料批次。第三方審計數據顯示,該系統誤檢率低于0.03ppm,顯著優于行業平均水平。
面向半導體設備向10kW/cm2功率密度發展的趨勢,建議行業重點關注三個方向:其一開發基于寬禁帶半導體的自診斷熔斷器,其二建立AI驅動的預測性維護平臺,其三制定涵蓋超快響應(納秒級)熔斷器的測試標準。同時,亟需加強多物理場耦合檢測技術研究,以應對3D封裝技術帶來的三維熱應力分布挑戰,為下一代半導體設備提供更可靠的保護解決方案。

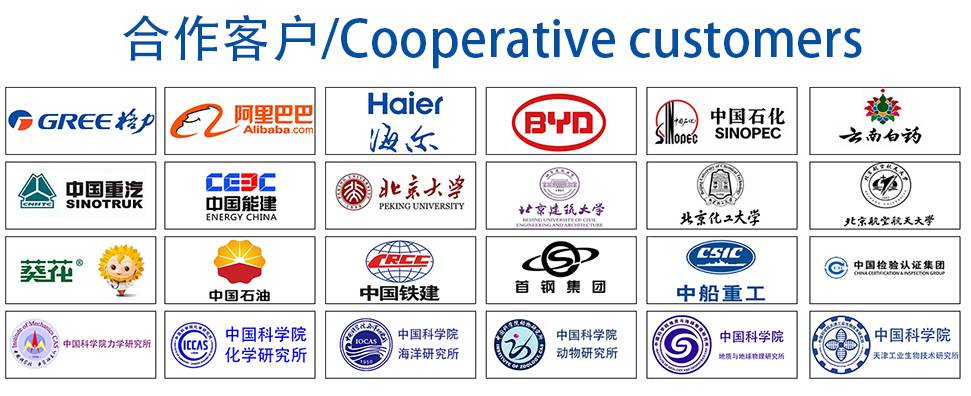