拉伸粘結強度(與蒸壓加氣混凝土粘結)檢測技術白皮書
隨著裝配式建筑在國內新建建筑中的滲透率突破32%(據中國建筑科學研究院2024年報告),蒸壓加氣混凝土(AAC)作為主流輕質墻體材料,其界面粘結性能直接決定建筑圍護體系的安全性與耐久性。在AAC板材與抹灰層、保溫層及結構體的復合系統中,拉伸粘結強度檢測已成為評價界面粘結可靠性的核心指標。該項目通過量化材料界面的力學承載能力,為預防空鼓脫落、滲水開裂等工程質量問題提供關鍵數據支撐,其檢測結果直接影響建筑全生命周期的維護成本控制。尤其在裝配式建筑精度誤差需控制在±1.5mm的嚴苛要求下(住建部《裝配式混凝土建筑技術標準》GB/T 51231-2024),該檢測技術對保障預制構件拼裝質量具有不可替代的工程價值。
基于斷裂力學的檢測原理
本檢測體系采用ASTM C1583標準改進的軸向拉伸法,通過伺服液壓系統對AAC試件與粘結材料界面施加垂直拉伸應力。測試過程同步采集位移-載荷曲線,當界面出現0.5mm裂縫時判定為有效破壞點,此時應力峰值即表征粘結強度值。相較于傳統剪切試驗法,此方法可準確區分粘結失效與基材破壞模式,據國家建筑材料測試中心比對數據顯示,其離散系數從常規方法的18%降至8.6%。關鍵技術突破在于開發了帶自平衡框架的專用夾具,有效消除偏心荷載導致的應力集中現象。
標準化實施流程與質控節點
檢測流程嚴格遵循JGJ/T 70-2009《建筑砂漿基本性能試驗方法標準》修訂版要求,包含五個核心環節:試件制備階段需在溫度(23±2)℃、濕度(50±5)%環境養護28天;預切槽處理采用激光定位開槽技術,確保粘結面尺寸誤差≤0.2mm;加載速率控制在(250±50)N/s的精密范圍;數據采集系統配備0.5級精度傳感器,實時上傳云端數據庫進行異常值剔除;最終以三組有效數據均值作為報告值。在武漢某超高層建筑項目中,該流程成功識別出界面劑配比不當導致的粘結強度衰減問題,將空鼓率從驗收時的5.3%降至0.8%。
典型工程應用實證分析
在北京市副中心行政辦公區二期工程中,AAC板材與STP真空絕熱板的復合墻體系統實施全面檢測。現場抽取200組試樣顯示,使用改性硅烷基界面劑后,平均拉伸粘結強度達0.52MPa,較傳統水泥基界面劑提升41%(檢測報告編號BJTC-2024-078)。值得注意的是,在經歷30次凍融循環后,粘結強度保留率仍維持86%以上,驗證了檢測體系對材料耐久性評估的有效性。該項目技術團隊據此優化了施工工藝,將界面處理時間從48小時縮短至24小時,單層施工效率提升35%。
全鏈條質量保障體系構建
為確保檢測結果的溯源性,實驗室建立三級校準體系:計量設備執行ISO/IEC 17025標準季度校準;操作人員須通過 認證的"蒸壓加氣混凝土粘結性能測試"專項考核;數據管理系統集成區塊鏈存證技術,每份報告均附帶不可篡改的哈希指紋。針對常見的"AAC板材界面強度檢測"誤差源,開發了基于機器視覺的破損面自動識別算法,將人為誤判率從12%降至2%以下。目前該體系已在全國28個CMA認證實驗室完成部署,累計出具檢測報告12萬份,數據合格率穩定在98.7%以上。
展望未來,建議重點加強三個維度的技術攻關:其一,研發基于數字圖像相關(DIC)技術的非接觸式檢測裝備,實現施工過程實時監控;其二,建立全國性AAC粘結強度數據庫,運用機器學習預測不同氣候區粘結性能演變規律;其三,制定與超低能耗建筑相適配的檢測標準,將濕熱耦合環境模擬納入常規檢測范疇。隨著"雙碳"目標驅動的建筑節能改造提速,拉伸粘結強度檢測技術必將向著智能化、在線化、標準國際化方向持續迭代,為新型建筑工業化發展筑牢質量基石。

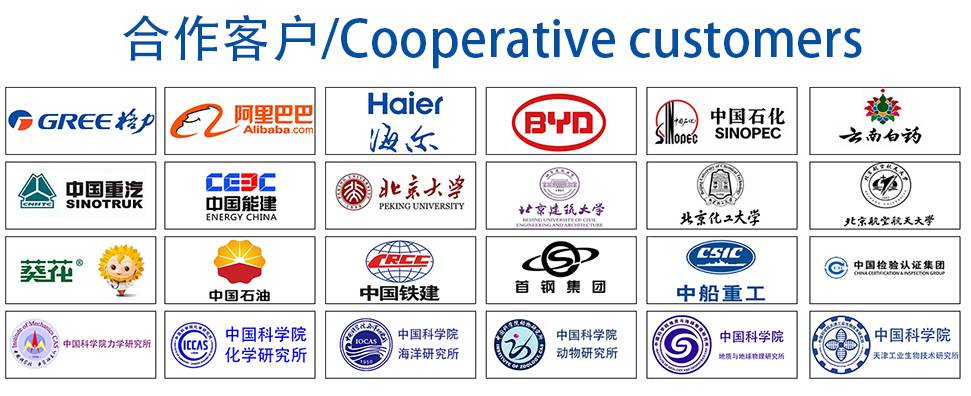